Mehr als ein Betondrucker Interview mit einem Großgerät: das DBFL
16 Meter lang, neun Meter breit und ein Arbeitsraum von 370 Kubikmetern: Das Digital Building Fabrication Laboratory (DBFL) des Instituts für Tragwerksentwurf (ITE) der Technischen Universität Braunschweig ist ein echtes Großgerät. Es schlicht 3D-Betondrucker zu nennen, greift zu kurz. Für Dr. Jeldrik Mainka vom ITE ist es das „größte Schweizer Taschenmesser“, das er kennt. Warum das so ist, hat das DBFL unserer Redakteurin Bianca Loschinsky selbst erzählt.
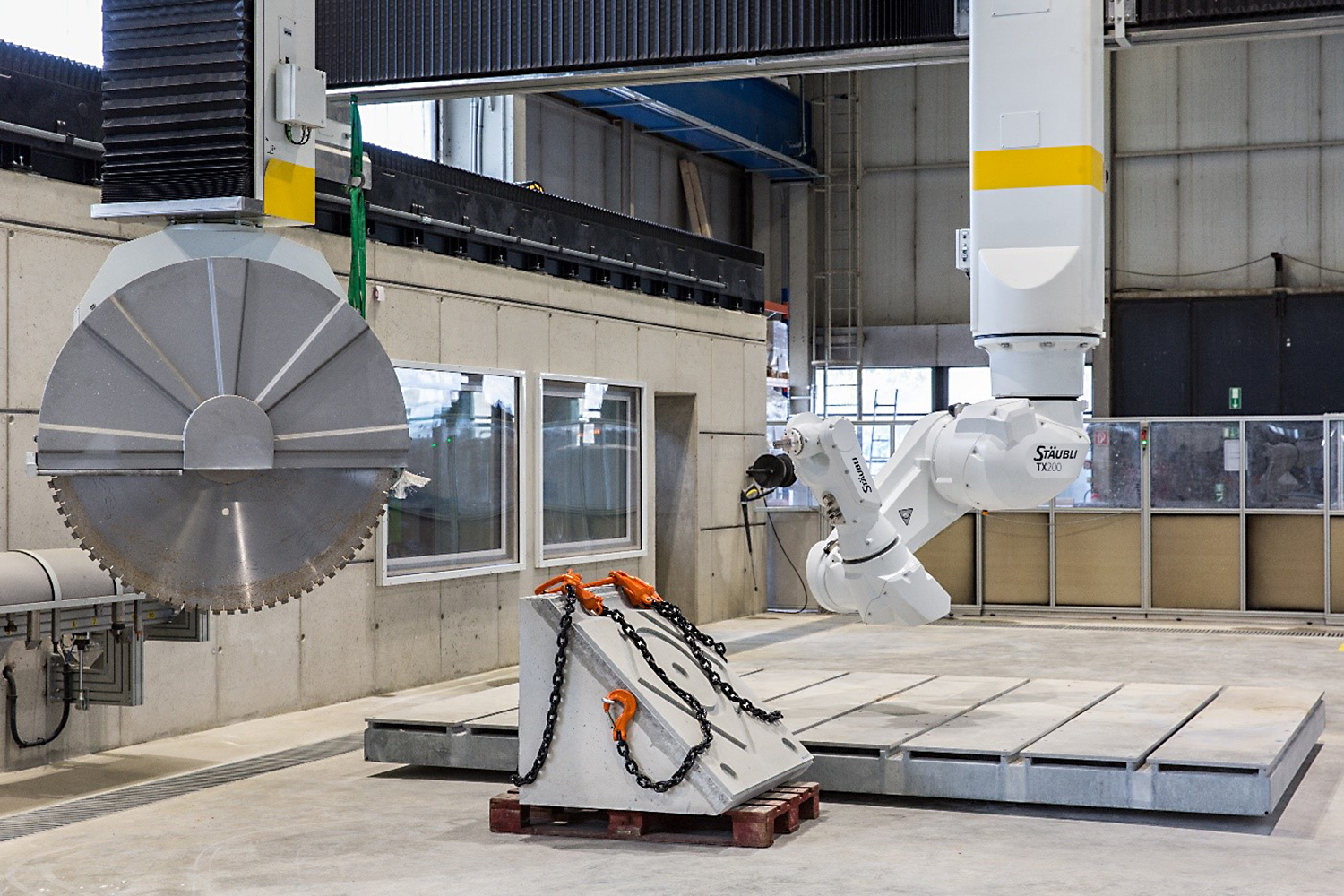
DBFL: „Das bin ich. Links ist mein Portal 1 mit dem riesigen Sägeblatt zu sehen und rechts mein Sechsachs-Roboterarm. Bildnachweis: ITE/TU Braunschweig
Am Tag unseres Besuchs ist es ungewöhnlich ruhig in der Versuchshalle des Leichtweiß-Instituts für Wasserbau, in dem das DBFL seinen Platz hat. Das Großgerät wird gerade gewartet. Einige Fettleitungen sind blockiert. Anja Stümmler, technische Mitarbeiterin am ITE und die „gute Seele“ des DBFL, ist gerade dabei, alle Leitungen zu überprüfen und zu reinigen. Wir treffen das DBFL also in einem entspannten und sauberen Zustand und haben uns vorher mit dem Gerät auf das „Du“ geeinigt.
Hallo DBFL, Dr. Jeldrik Mainka hat sehr begeistert von dir berichtet, deinen verschiedenen Werkzeugen und deinen zahlreichen Einsatzmöglichkeiten. Erzähl doch mal selbst!
Nun ja, ich bin so etwas wie ein digitales Baufabrikationszentrum. Keinesfalls möchte ich einfach nur Betondrucker genannt werden. Ich kann so viel mehr! Natürlich können sich viele unter Betondruck etwas vorstellen. Obwohl es auch da ganz unterschiedliche Varianten gibt. Ich mache hier hauptsächlich Extrusionsdruck unter Zugabe von Druckluft. Das ist das Besondere. Ich lege nicht nur Schichten ab, sondern schieße sie mit Druckluft richtig zusammen, um den Verbund herzustellen. Das Ganze nennt sich dann SC3DP –Shotcrete 3D Printing und wurde hier an der TU Braunschweig entwickelt.
Aber vielleicht mal von vorn: Was habe ich alles zu bieten? Zunächst eine CNC-Fräse aus der Marmorindustrie. CNC steht für Computerized Numerical Control. Meine Fräse ist also computergesteuert und kann mit hoher Präzision auch komplexe Formen digital bearbeiten. Mit der Fräse kann ich Beton, Naturstein, Holz, Kunststoffe und sogar Stahl fräsen, schneiden, zerspanen. Übrigens wurden die Fassadenelemente des Braunschweiger Schlosses von meiner Schwester einer baugleichen Fräse gefräst. Das ist mein Portal 1. Dazu kommt ein Sechsachs-Roboterarm, ein Stäubli-TX200: mein Portal 2. Mein Roboterarm kann aus allen Richtungen den Beton spritzen, also in 3D. Und ich kann mit verschiedensten Endeffektoren, Werkzeugen am Ende meines Roboterarms, arbeiten. Diese Kombination ist wirklich einzigartig.
Ist das nicht etwas dick aufgetragen?
Nein, definitiv nicht! So wie ich hier stehe und ausgestattet bin, mit meinen beiden Portalen und damit den zwei frei im Raum orientierbaren Bearbeitungsköpfen, mit meiner Genauigkeit und Robustheit, bin ich tatsächlich weltweit einmalig.
Die Betonwände um mich herum sind sehr dick, nicht weil ich so schwer bin, sondern weil ich ein hochpräzises Gerät bin und die Verformungen möglichst gering sein müssen. Die Wände sind fast 70 Zentimeter breit, die Bodenplatte hat eine Dicke von einem guten Meter. Das ist notwendig, weil meine Fräse und mein Roboterarm eine Wiederholgenauigkeit in diesem riesigen Raum von einem Zehntelmillimeter haben.
Wenn also große Wände nach der Erstellung wie Legosteine zusammenpassen sollen, kann ich die Fügungen, die zwischen den Bauteilen sind, auf Zehntelmillimeter genau herstellen. In dieser Präzision kann das kein Mensch. Was nicht heißt, dass ich den Menschen auf dem Bau ersetzen will. Ganz im Gegenteil: Ich schaffe die Voraussetzungen für neue Facharbeitsprofile.
Dazu habe ich richtig Power. Allein die Spindel des Motors für die Fräse hat 64 KW, das sind 100 PS – nur um richtig Abzudrehen, wenn ich will. Das Sägeblatt hat einen Durchmesser von 1,30 Meter und der größte Fräskopf einen Durchmesser von zehn Zentimetern. Das ist doch schon mal was!
Das klingt tatsächlich sehr beeindruckend. Aber ohne menschliche Unterstützung bist du doch eher hilflos.
Darüber rede ich eigentlich nicht so gern. Aber ja, allein kann ich nichts. Über den Kontrollraum steuern meist Wissenschaftlerinnen und Wissenschaftler meine beiden Portale. Doch zuvor müssen sie am Computer für die verschiedenen Objekte Linienmodelle erstellen und viele Parameter eingeben, zum Beispiel für den Luftdruck oder die Menge des Erstarrungsbeschleunigers, der in der Düse zugeführt wird. Das ist tatsächlich auch das Kniffligste: Alle Parameter gleichzeitig zusammenzubringen, von der Bahnplanung über die Materialzufuhr, die Kontrolle des Materials selbst.
Ein Beispiel: Wenn ich eine zwei Meter hohe Wand drucken soll – Beton wiegt ja einiges – funktioniert es in den unteren 30 Zentimetern noch ganz gut. Aber was passiert, wenn im oberen Bereich die Last immer größer wird und unten der Beton noch nicht hart ist? Im schlimmsten Fall fällt die Wand um, weil die Last zu groß wird. Aber es kann auch sein, dass sich der weiche Beton einfach nur selbst zusammendrückt. Dann ist jedoch der Punkt, der im digitalen Modell vorhanden ist, nicht mehr da, wo er im Realen sein sollte, weil sich das Material verformt hat. Ich muss nun also erkennen, wo das geplante Bauteil gerade wirklich in Raum und Zeit ist. Für Menschen ist das kein Problem, die sehen das. Mir müssen die Wissenschaftlerinnen und Wissenschaftler das aber erklären. In diesem Fall mit vielen Sensoren, z.B. einem Laserscanner, mit dem ich messen kann.
Bei den Versuchen sind immer sehr viele Menschen dabei: der Projektleiter, unsere Technikerin Anja Stümmler, eine Wissenschaftlerin oder ein Wissenschaftler, die oder der meine Bewegungen steuert, jemand, der für das Material zuständig ist und noch mindestens ein Team-Mitglied, das alles überwacht. Bei einem Druckversuch laufen also einige Personen herum. Natürlich wollen alle sehen, wie ich eine Wand entstehen lasse und die Prozesse in der Grundlage erforsche.
Wofür benötigen dich die Wissenschaftlerinnen und Wissenschaftler?
Mein Team vom ITE möchte gern wissen, wie man Prozesse im Bauwesen nicht nur in der Planung digitalisieren kann, sondern auch in der Fabrikation. In der Automobilindustrie ist die automatisierte Fertigung sehr weit fortgeschritten, im Bauwesen hat sich in den vergangenen Jahrzehnten aber nicht viel getan. Es wird immer noch Stein auf Stein, Wand auf Wand gebaut. Das liegt daran, dass wir im Bauwesen immer Unikate bauen. Und das ist die Herausforderung. Roboter wie mich kann man anlernen, einen Prozess immer zu wiederholen, aber bei einem Bauwerk ist das nicht gegeben. Professor Harald Kloft und Professor Norman Hack vom ITE versuchen zu erforschen, wie man Automatisierung und digitale Fertigung im Bauwesen etablieren kann, um Unikate herzustellen, die möglichst materialeffizient sind. Sie sagen dazu auch „serielles Unikat“.
Mit mir erforschen die Wissenschaftlerinnen und Wissenschaftler hochpräzises Arbeiten, wie Bauberufe sinnvoll ergänzt werden können und wie insgesamt effizienter gebaut werden kann. Wusstest du, dass die Betonproduktion mehr CO2-Emissionen verursacht als der gesamte Verkehr – Luftfahrt, Schiff und Auto – zusammen? Das liegt vor allem an der energieintensiven Zementherstellung. Mit digitalen Prozessen kann das Material besser eingesetzt und deutlich weniger verbraucht werden. Ziel ist es, künftig Beton nur da abzulegen, wo es im Bauteil gebraucht wird. Wenn man anfängt, im Kleinen einzusparen und auf das Große transferiert, ist die Hoffnung meines Teams, dass wir etwas bewegen und für Umwelt und Klima tun.
Du bist in den vergangenen vier Jahren, die du existierst, oft in Betrieb gewesen. Und zwar für ganz unterschiedliche Projekte. An welche erinnerst du dich?
Da sind inzwischen seit meinem offiziellen Geburtstag am 13. September 2016 einige zusammen gekommen. Mit Dr. Jeldrik Mainka, der mich mit geplant hat, habe ich eine nachhaltige freigeformte Beton-Schalung aus großen Wachsblöcken hergestellt. Dazu habe ich riesige Mengen Wachs gefräst. Später konnte man die Wachsspäne wieder zu neuen Blöcken einschmelzen, also eine Non-Waste-Wachsschalung.
Außerdem habe ich mit meinem Roboterportal ein völlig neues Verfahren für die automatisierte Herstellung von Stampflehm ausprobiert. Das funktioniert so gut, dass wir mit dem Verfahren unter die drei Finalisten beim diesjährigen DGNB Sustainability Challenge in der Kategorie Forschung gekommen sind.
Sehr spannend und ganz neu waren für mich Arbeiten zusammen mit den Professoren Nils Goseberg und Jochen Aberle vom Leichtweiß-Institut für Wasserbau. Wer hätte gedacht, dass ich einmal Modelle der pazifischen Auster fräse oder verschiedene Modellabschnitte eines gescannten Tunnels in einem norwegischen Berg, um strömungsmechanische Simulationen zu validieren?
Sogar Stahl kann ich drucken. Hast du die Vase gesehen, die meine Kolleginnen und Kollegen designt haben? Das ist doch fast Kunst. Vier Stunden habe ich dafür vor mich hin gedruckt.
Besonders wichtig bin ich natürlich für den Sonderforschungsbereich TRR 277 „Additive Manufacturing in Construction (AMC) – The Challenge of Large Scale“. Hier komme ich richtig in Fahrt und unterstütze die Grundlagenforschung zur additiven Fertigung. Nach den drei Förderperioden sollen Prozesse stehen, die man in die Bauindustrie übernehmen kann, zum Beispiel eine optimierte Brücke zu drucken oder Häuser, die ganz anders aussehen und mit viel weniger Material hergestellt werden.
Vermutlich sprichst du auch darüber nicht so gern. Aber hast du irgendwelche Macken?
Hm. Das können nicht viele Geräte, aber wie ihr Menschen könnte ich mich selbst zerstören. Falls jemand versehentlich einen falschen Parameter eingibt, dann könnte mein Roboterarm mit dem, was ich in der „Hand halte“, gegen die Betonwand schlagen. Und mein Portal 1 könnte locker mit der Säge den Arm meines Roboters absägen. Wenn ich arbeite, darf niemand in meine Nähe kommen. Dafür gibt es Schutztore und –mechanismen. Ich stehe sozusagen unter totaler Überwachung: Vom Steuerstand aus haben mich die Wissenschaftlerinnen und Wissenschaftler und natürlich Anja, mein Schutzengel, unter Kontrolle.
Hier sieht es gerade sehr sauber aus. Du machst doch sicherlich viel Schmutz?
Das kann man wohl sagen. An einem Drucktag verbrauche ich bis zu 20 Tonnen Beton. Da gibt es auch viel Lärm, Schmutz und Staub. Deshalb habe ich zusätzlich zu den hohen Wänden an den Längsseiten noch Vorhänge an den kurzen Seiten erhalten und eine Absaugvorrichtung, damit sich der Staub nicht in der Halle verteilt.
Und wer macht dich sauber?
Reinigen muss Spaß machen, hat mir Jeldrik gesagt. Wenn es in einer WG keine Spülmaschine gibt, dann hat man schon verloren. Ich habe Ablaufrinnen und auch einen richtigen Feuerwehrschlauch, mit dem man alles abspritzen kann. Das lieben nicht nur die Hiwis! Zusätzlich habe ich einen eingebauten Hochdruckreiniger, der kribbelt so herrlich am Spanntisch. Und das ITE hat eine Kehrmaschine gekauft. Also alles, was das Reinigen erleichtert. Mal fällt auch eine Wand um, weil irgendein Parameter nicht gestimmt hat. Das gehört einfach dazu, daraus kann man ja lernen. Da liegen dann 500 Kilogramm Beton und müssen weggeschaufelt werden. (lacht!) Nach so einem Tag sind meine Kolleginnen und Kollegen ziemlich erschöpft. Auch die Chefs, Professor Kloft und Professor Hack, haben schon geschaufelt. Außer mir müssen alle mal schaufeln (lacht nochmal!). Leider haben die Wissenschaftlerinnen und Wissenschaftler versprochen, dass sie mir das Schaufeln und Reinigen auch noch beibringen wollen. Egal, wir sind ja ein Team!