More than a concrete printer Interview with a large-scale device: the DBFL
16 metres long, nine metres wide and a workspace of 370 cubic metres: the Digital Building Fabrication Laboratory (DBFL) of the Institute of Structural Design (ITE) at Technische Universität Braunschweig is really a large-scale device. Simply calling it a 3D concrete printer falls short. For Dr Jeldrik Mainka of the ITE, it is the “largest Swiss army knife” he knows. The DBFL itself told our editor Bianca Loschinsky why this is so.
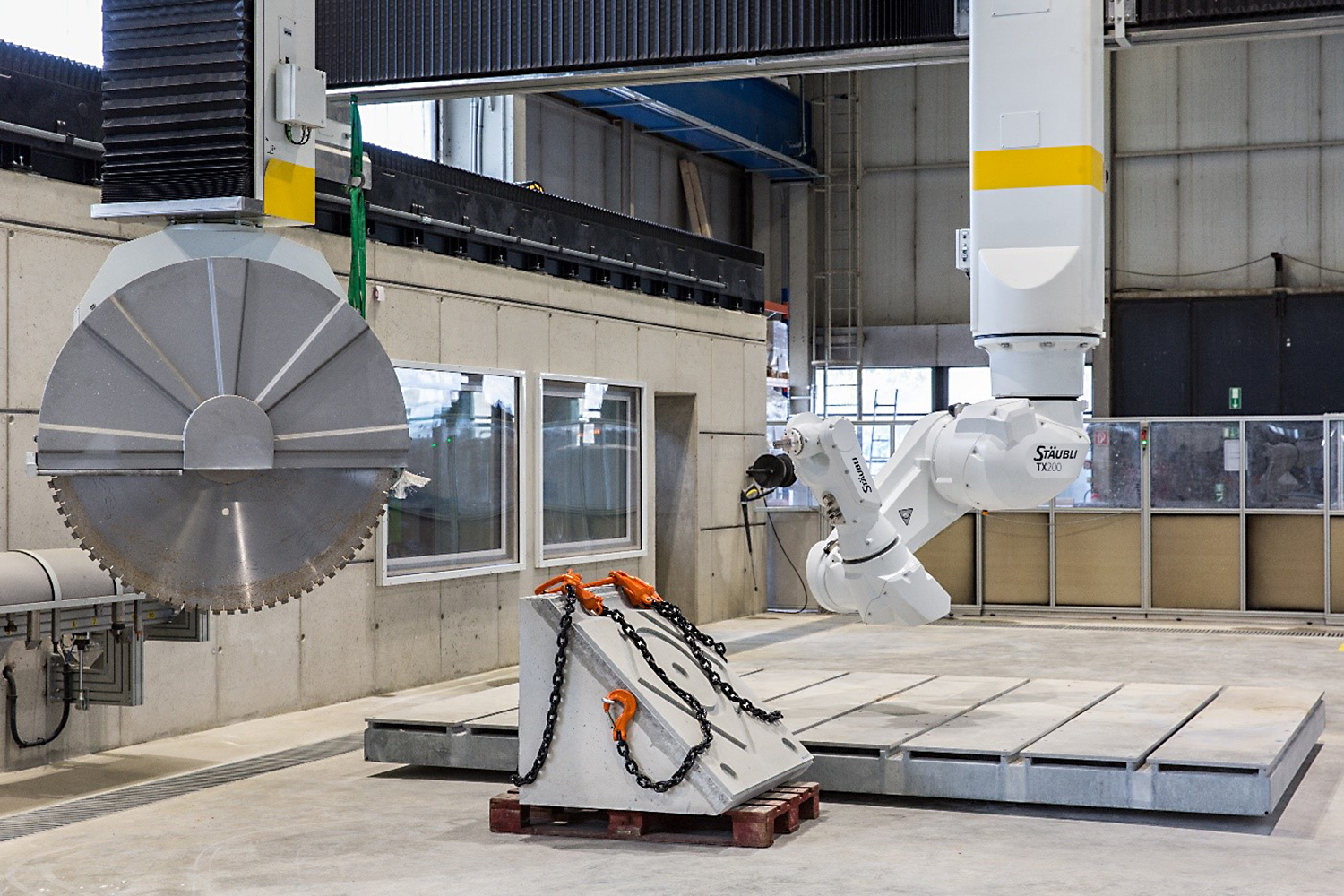
DBFL: “This is me. On the left is my Portal 1 with the huge saw blade and on the right you can see my six-axis robot arm. Photo credit: ITE/TU Braunschweig
On the day of our visit, it is unusually quiet in the laboratory of the Leichtweiß Institute for Hydraulic Engineering and Water Resources, where the DBFL is located. The large-scale device is being serviced. Some grease lines are blocked. Anja Stümmler, technical employee at the ITE and the “good soul” of the DBFL, is busy checking and cleaning all the lines. So we are meeting the DBFL in a relaxed and clean state and have made a prior agreement with the device to speak informally to each other.
Hello DBFL, Dr. Jeldrik Mainka has spoken very enthusiastically about you, your various tools and your many uses. Why don’t you tell us about them yourself?
Well, I am something of a digital building fabrication centre. By no means do I want to be called just a concrete printer. I can do so much more! Of course, many people have an idea of what concrete printing is. Although there are also very different variations. I mainly do extrusion printing with the addition of compressed air here. That’s what makes it special. I don’t just lay down layers, I really shoot them together with compressed air to create the bond. The whole thing is called SC3DP – Shotcrete 3D Printing and was developed here at TU Braunschweig.
But maybe let’s start from the beginning: What do I have to offer? First of all, a CNC milling machine from the marble industry. CNC stands for Computerised Numerical Control. So my milling machine is computer-controlled and can digitally process even complex shapes with high precision. With the milling machine, I can mill, cut and machine concrete, natural stone, wood, plastics and even steel. By the way, the façade elements of Braunschweig Schloss were milled by my sister with a milling machine of the same design. That’s my Portal 1. Added to that is a six-axis robot arm, a Stäubli-TX200: my Portal 2. My robot arm can spray the concrete from all directions, so in 3D. And I can work with a wide variety of end effectors, tools at the end of my robot arm. This combination is really unique.
Isn’t that laying it on a bit thick?
No, definitely not! As I stand here and am equipped, with my two portals and thus the two processing heads that can be oriented freely in space, with my precision and robustness, I am indeed unique in the world.
The concrete walls around me are very thick, not because I’m so heavy, but because I’m a high-precision machine and the deformations have to be as small as possible. The walls are almost 70 centimetres wide and the floor slab is a good metre thick. This is necessary because my milling machine and my robot arm have a repeat accuracy in this huge space of a tenth of a millimetre.
So if large walls are to fit together like Lego bricks after they have been created, I can produce the joints that are between the components with an accuracy of a tenth of a millimetre. No human being can do that with such precision. Which doesn’t mean that I want to replace people on the construction site. Quite the opposite: I create the conditions for new skilled work profiles.
I have real power for this. The spindle of the motor for the milling cutter alone has 64 KW, that’s 100 hp – just to really turn the wheel when I want to. The saw blade has a diameter of 1.30 metres and the largest milling head has a diameter of ten centimetres. That’s quite something!
That sounds very impressive indeed. But without human support you are rather helpless.
I don’t really like to talk about that. But yes, I can’t do anything on my own. My two portals are usually controlled by scientists in the control room. But before that, they have to create line models for the various objects on the computer and enter many parameters, for example for the air pressure or the amount of solidification accelerator that is fed into the nozzle. That is actually also the trickiest thing: bringing all the parameters together at the same time, from the path planning to the material feed, the control of the material itself.
Example: If I have to print a two-metre-high wall—concrete obviously weighs a lot—it still works quite well in the lower 30 centimetres. But what happens when the load increases in the upper area and the concrete is not yet hard at the bottom? In the worst case, the wall falls down because the load is too heavy. But it’s also possible that the soft concrete simply compresses itself. But then the point that is there in the digital model is no longer where it should be in the real one because the material has deformed. So now I have to recognise where the planned component really is in space and time. That’s no problem for humans, they can see that. But the scientists have to explain it to me. In this case with many sensors, for example a laser scanner, with which I can measure.
There are always a lot of people involved in the experiments: the project leader, our technician Anja Stümmler, a scientist who controls my movements, someone who is responsible for the material and at least one more team member who monitors everything. So there are a few people running around during a print test. Of course, everyone wants to see how I create a wall and research the processes in the foundation.
What do the scientists need you for?
My team at ITE would like to know how to digitise processes in construction not only in planning, but also in manufacturing. In the automotive industry, automated manufacturing is very advanced, but in construction not much has happened in the past decades. We still build brick on brick, wall on wall. That’s because in construction we always build one-offs. And that’s the challenge. Robots like me can be trained to repeat a process over and over again, but that’s not a given with a building. Professor Harald Kloft and Professor Norman Hack from ITE are trying to research how automation and digital manufacturing can be established in the building industry to produce one-offs that are as material-efficient as possible. They also call this “serial one-off”.
With me, the scientists are researching high-precision work, how construction jobs can be supplemented in a meaningful way and how construction can be more efficient overall. Did you know that concrete production causes more CO2 emissions than all transport— aviation, shipping and cars—combined? This is mainly due to the energy-intensive production of cement. With digital processes, the material can be used better and consumed much less. The goal is to only deposit concrete where it is needed in the component in the future. If you start saving on a small scale and transfer it to a large scale, my team’s hope is that we will make a difference and do something for the environment and the climate.
You have been in operation many times in the past four years that you have existed. And for very different projects. Which ones do you remember?
There have been quite a few since my official birthday on 13 September 2016. With Dr. Jeldrik Mainka, who helped plan me, I made a sustainable free-form concrete formwork out of large wax blocks. For this I milled huge amounts of wax. Later, the wax shavings could be melted down again to make new blocks, so it was a non-waste wax formwork.
I also tried out a completely new process for the automated production of rammed earth with my robot portal. It works so well that we were one of the three finalists in this year’s DGNB Sustainability Challenge in the research category.
The work I did with Professors Nils Goseberg and Jochen Aberle from the Leichtweiß Institute for Hydraulic Engineering and Water Resources was very exciting and completely new for me. Who would have thought that one day I would be milling models of the Pacific oyster or different model sections of a scanned tunnel in a Norwegian mountain to validate fluid mechanics simulations?
I can even print steel. Have you seen the vase my colleagues designed? It’s practically art. I spent four hours printing for it.
Of course, I’m particularly important for the Collaborative Research Centre TRR 277 “Additive Manufacturing in Construction (AMC) – The Challenge of Large Scale”. This is where I really get going and support basic research on additive manufacturing. After the three funding periods, the aim is to have processes that can be adopted in the construction industry, for example printing an optimised bridge or houses that look completely different and are made with much less material.
You probably don’t like to talk about this either. But do you have any flaws?
Hm. Not many devices can do this, but like you humans, I could self-destruct. If someone accidentally enters a wrong parameter, my robot arm could hit the concrete wall with what I’m “holding in my hand”. And my Portal 1 could easily saw off my robot’s arm with the saw. When I’m working, no one is allowed near me. There are protective gates and mechanisms for that. I’m under total surveillance, so to speak: from the control stand, the scientists and of course Anja, my guardian angel, have me under control.
It looks very clean here right now. Surely you make a lot of dirt?
You could say that. On a printing day I use up to 20 tonnes of concrete. There’s also a lot of noise, dirt and dust. That’s why, in addition to the high walls on the long sides, I was given curtains on the short sides and an extraction system so that the dust doesn’t spread around the hall.
And who cleans you?
Cleaning has to be fun, Jeldrik told me. If there’s no dishwasher in a shared flat, you’ve already lost. I have drainage channels and a real fire hose that you can use to hose everything down. It’s not just the research assistants who love it! In addition, I have a built-in high-pressure cleaner that tingles so wonderfully on the clamping table. And the ITE has bought a sweeper. So everything that makes cleaning easier. Sometimes a wall falls down because some parameter is wrong. That’s just part of it, you can learn from it. Then there are 500 kilograms of concrete that have to be shovelled away. (laughs!) After a day like that, my colleagues are pretty exhausted. Even the bosses, Professor Kloft and Professor Hack, have shovelled before. Except for me, everyone has to shovel (laughs again!). Unfortunately, the scientists have promised to teach me how to shovel and clean as well. Whatever, we’re a team after all!