3D-Drucken mit Beton: „An die Grenzen der Kinematik gehen“ Robotergesteuerte Produktion in einzigartiger Anlage
Es klingt außergewöhnlich: Bauen mit Beton ohne Schalbretter, Baugerüste und Maurerkellen! Was wäre, wenn diese Arbeit ein Roboter und eine Fräse übernehmen? Wissenschaftlerinnen und Wissenschaftler der Technischen Universität Braunschweig forschen zum 3D-Betondruck in der Digital Building Fabrication Laboratory (DBFL) des Instituts für Tragwerksentwurf (ITE). Ich habe Hendrik Lindemann getroffen, der sich bestens mit der Anlage auskennt.
„Kann man hier wirklich von 3D-Betondruck sprechen?“ frage ich Hendrik Lindemann, der gerade seine Doktorarbeit über generative Fertigung an der TU Braunschweig schreibt. „Das, was man oft unter 3D-Druck versteht, ist genau genommen nur 2,5D-Druck. Unser Roboterarm kann aus allen Richtungen den Beton spritzen, also in 3D.“ Während ein herkömmlicher 3D-Drucker schichtweise Material aufträgt, kann die Anlage im DFBL die Betondüse über insgesamt neun Achsen steuern.
Das Verfahren nennt sich „Shotcrete 3D Printing“, kurz SC3DP, und wurde am ITE in Zusammenarbeit mit dem Institut für Baustoffe, Massivbau und Brandschutz (iBMB) und dem Institut für Werkzeugmaschinen und Fertigungstechnik (IWF, beide TU Braunschweig) sowie dem Institut für Montagetechnik (MATCH) der Leibniz Universität Hannover entwickelt.
Die Anlage basiert auf CNC-Fräse mit fünf Freiheitsgraden aus der Marmorindustrie der Firma OMAG. Dazu gesellt sich ein Sechsachs-Roboterarm, ein Stäubli-TX200, an einer Dreiachs-Kinematik. Diese Kombination ist einzigartig. Mit diesen zwei frei im Raum orientierbaren Bearbeitungsköpfen erlaubt das DBFL sowohl den additiven Aufbau im Betonspritzverfahren als auch die subtraktive Nachbearbeitung, zum Beipiel durch Sägen oder Fräsen zum Herstellen von millimetergenauen Fügungen.
Das Einschalen vor dem Betongießen, das jeder von der Baustelle kennt, scheint passé. Die Vorteile liegen auf der Hand: eine kosteneffektivere, nachhaltigere Fertigung von individuellen Bauteilen mit hoher Präzision und kurzen Umrüstzeiten.
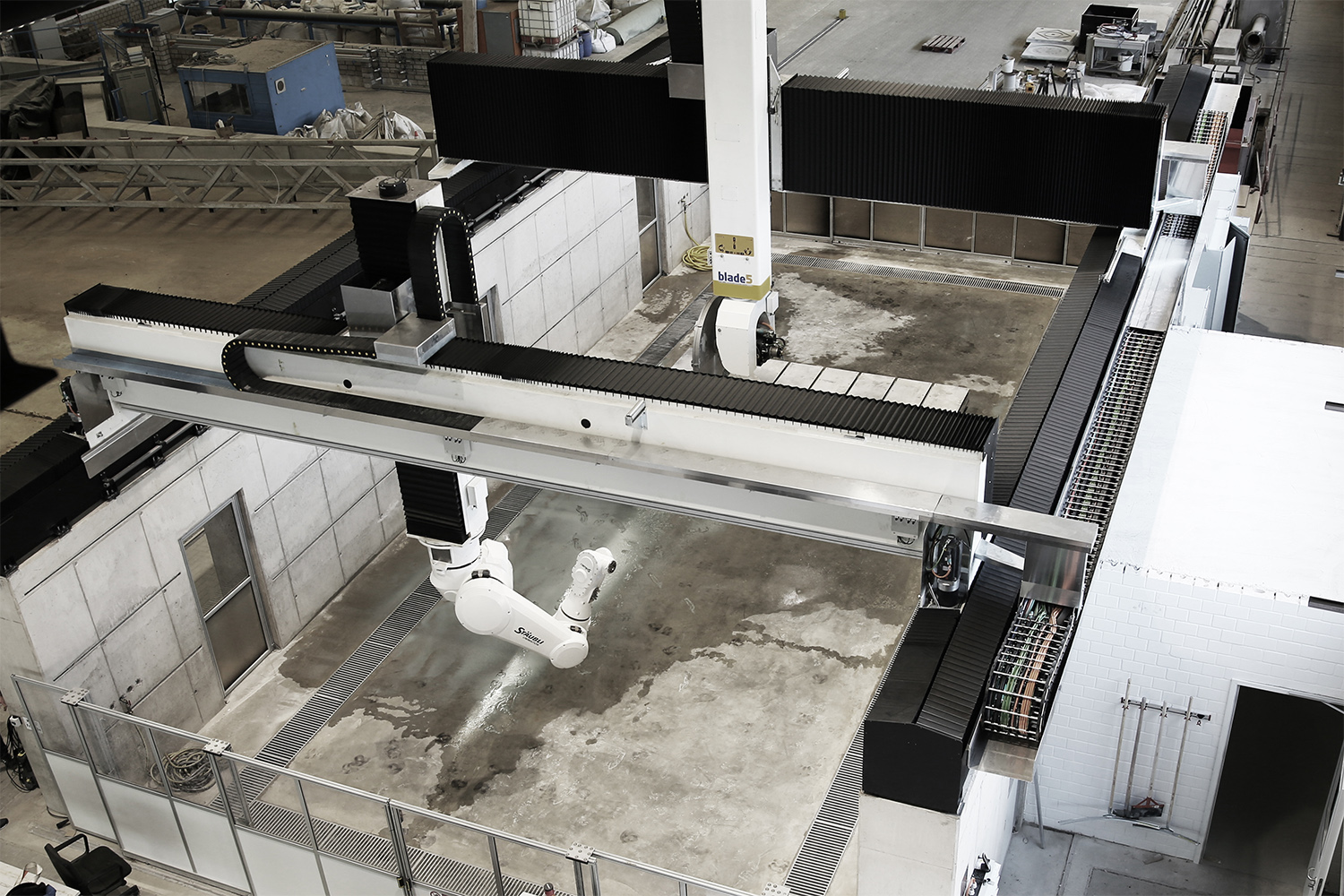
Blick von oben auf das DBFL: Gut zu erkennen sind die beiden Achswege der beiden Portale für CNC-Fräse und Roboterarm, Bildnachweis: Justus Hoven/TU Braunschweig
Noch nicht vollautomatisch
Als ich vor dem DBFL stehe, blicke ich auf eine Anlage mit einer Länge von über 16 Metern und einer Breite von über sieben Metern, eingekleidet in hohe Betonwände an den beiden langen Seiten und geschützt durch transparente Tore an den kurzen. Darin befinden sich zwei sogenannte Portale, die die Bearbeitungsköpfe tragen und ihnen noch mehr Bewegungsmöglichkeiten verschaffen.
Rechts davon ist ein Kontrollraum, von dem ich den Arbeitsbereich überblicken kann. Dort liegt kaum Staub und kleben keine angetrockneten Betonreste. Das wird sicher nicht immer so sein. „Die Reinigung ist noch sehr aufwändig. Es arbeiten viele Leute daran, dass die Anlage nach jedem Versuch wieder sauber ist“, sagt Lindemann. Ob es noch andere praktische Herausforderungen gibt, frage ich. Wir gehen hinter die Anlage, dort lagert alles, was man zum Anmischen des Betons benötigt: eine Spezialbetonmischung als Sackware, ein Zwangsmischer, eine Pumpe. „Wir mischen den Beton derzeit noch manuell. Wenn die Mischung fertig gerührt ist, schaufeln drei Hiwis den Mörtel in die Pumpe. Das ist harte Arbeit und definitiv ein Bereich, für den noch eine Automatisierung entwickelt werden muss.“
So wird der Roboter programmiert
Vor einem Fertigungsprozess erstellt Lindemann am Computer ein Linienmodell, das sich an der Form des Objekts orientiert. Die Linien stellen die Bewegungen des Roboterkopfes dar, der im Abstand von 20 Zentimetern vom zu fertigenden Objekt Beton aufträgt. „Das Besondere ist, die Roboterfahrt kann simuliert werden“ – Lindemann zeigt mir den virtuellen Arbeitsraum mit dem Roboter, der die vorher gezeichneten Linien abfährt.
Danach stellt er in einer anderen Software zum visuellen Programmieren viele Parameter ein, zum Beispiel für den Luftdruck oder die Menge des Trocknungsbeschleunigers, der in der Düse zugeführt wird. Die Parameterwerte und ihre Abhängigkeiten voneinander scheinen das Kniffligste am Betondruck zu sein. „Parametrisches Design“ nennen das Lindemann und seine Kollegen, das sie in vielen Experimenten ausloten, um komplizierte Formen, eine gewünschte Steifigkeit oder Oberfläche herstellen zu können. Denn die Forschungsanlage ist eine, die nicht nur für einen bestimmten Zweck gebaut wurde. Die Forscher können viele Prozesse ausprobieren, bevor sie für den industriellen Bereich spezialisiert werden. „Wir sind schon oft an die Grenzen der Kinematik des Sechs-Achs-Roboters gegangen“, erinnert sich Lindemann, zum Beisiel beim Aufbau von Überhängen.
Produktion jederzeit anpassbar
Spritzbeton ist als Verfahren seit rund 100 Jahren bekannt und wird in der Tunnelsanierung, bei der Stabilisierung von Felswänden oder beim Bau von Kletteranlagen verwendet. Die Arbeit des Düsenführers wird zertifiziert und ist eine körperlich anspruchsvolle Tätigkeit. Firmen bieten die Technik als Spezialdienstleistung an. Gut, das machen dann künftig Roboter? Ich lasse mir das lieber noch einmal erklären. Das „Shotcrete 3D Printing“ verstehen die Braunschweiger Forscher nicht als Ersatz der herkömmlichen Herangehensweise. Sie vereinen die besten Methoden – die erprobte Technik mit Automatisierung und Präzision, so dass ein neues Verfahren entsteht.
„Das geht nur, wenn wir bisherige Fertigungsprozesse in Frage stellen“, sagt Lindemann. Während üblicherweise zu Beginn ein Desigentwurf vorläge, für das eine geeignete Produktionsmethode ermittelt werden würde, ginge man mit SC3DP genau umgekehrt heran. Die Produktion könne hier so angepasst werden, dass das erforderliche Design umgesetzt werden kann. „Die Idee dahinter ist, dass die Produktion selbst zum Designfaktor wird.“
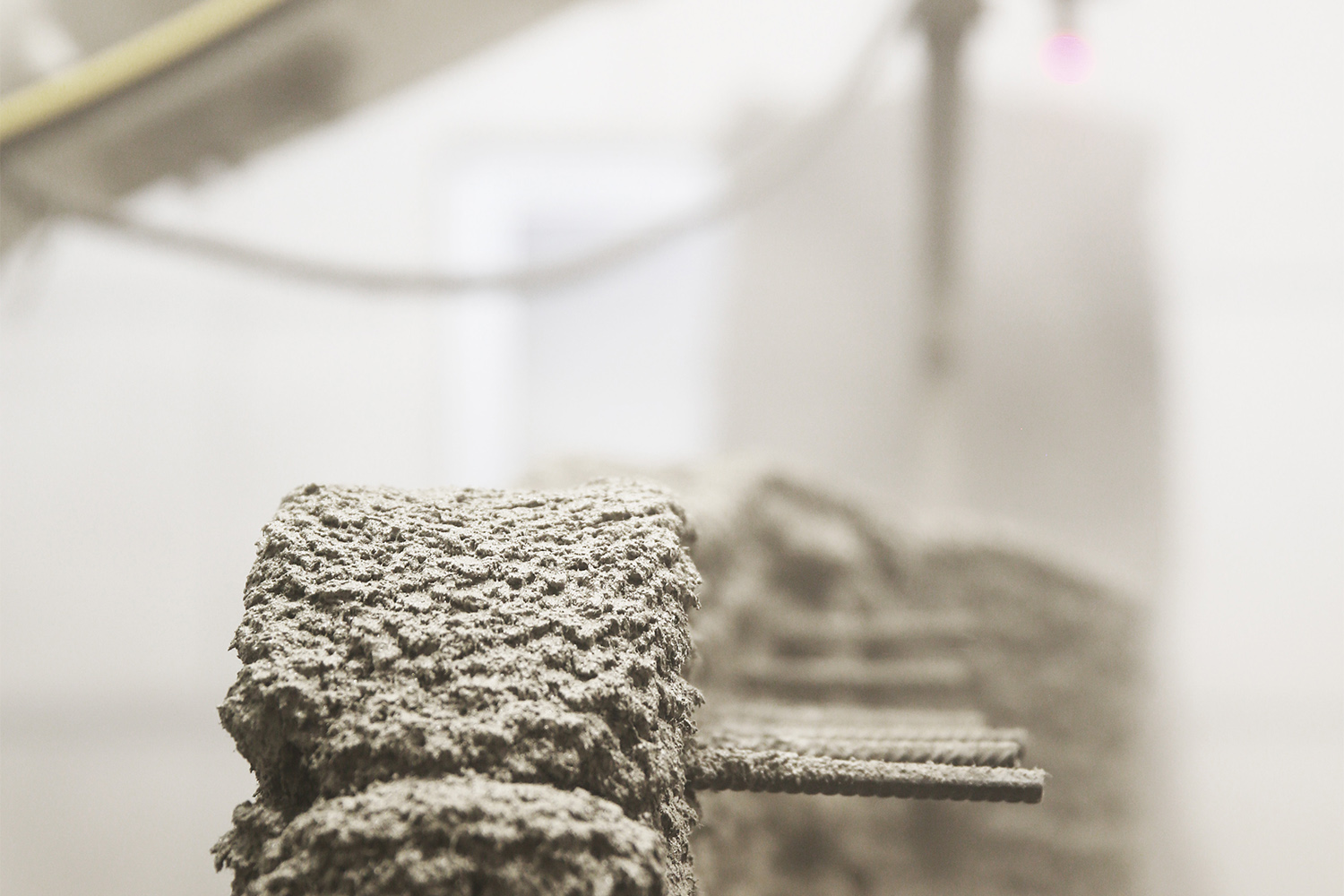
Spitzen mit Beton: Detail eines additiven Aufbaus; Bildnachweis: Jan Leonard Goldenbaum/TU Braunschweig
Neue Herausforderungen
Mit dem Bau der Produktionshalle hat das ITE einen erster goßen Schritt in diese Richtung getan. Pläne für die Zukunft haben die Forschenden reichlich. Zum Beispiel könnte eine Lasermessung dabei helfen, die abgegebene Betonmenge an der Düse bei Unebenheiten auf dem Objekt zu regulieren. Daran arbeitet das ITE gemeinsam mit Kollegen vom IWF der TU Braunschweig und von MATCH der Leibniz Universität Hannover.
Bisher wird in einem Fertigungsprozess eine Betonart zugeführt. Was ist aber, wenn stellenweise festeres oder feineres Material geeigneter wäre? Und wenn wir gerade beim Material sind: Welche Zusatzstoffe, welche Mischverhältnisse sind optimal? Auch daran möchte das DBFL-Team zusammen mit Teams vom iBMB der TU Braunschweig und vom Institut für Nichtmetallische Werkstoffe der TU Clausthal forschen. Besonders offensichtlich ist auch der Wunsch nach einer effektiveren Oberflächenbearbeitung: Wann ist der beste Zeitpunkt zum Glätten des Spritzbetons – im erdfeuchten Zustand, halb oder ganz durchgetrocknet? Welche Frässcheibe eignet sich dazu am besten?
Was noch sehr viel Zeit raubt, ist die objektbezogene Herstellung von Bewehrungen, also das Armieren des Betons mit Stahl, um eine hohe Tragfähigkeit zu gewährleisten. Ob man das auch automatisieren könnte, frage ich. Daraufhin zeigt mir Lindemann etwas, das gerade erst angeliefert wurde und die Anlage um eine ganz neue Funktion erweitert: ein Industrieschweißgerät. Es sieht so aus, als reicht der Begriff „3D-Betondruck“ bald kaum noch aus.

Der Roboterarm, ausgestatt mit Kamera und Lasermesseinheit, um Unebenheiten beim Spitzen auszugleichen; Bildnachweis: Jan Leonard Goldenbaum/TU Braunschweig