Breaking GaN Präzise Maschinen für die nächste Generation von LED-Chips
Der Weg zu neuen LED-Technologien erfolgt Schicht für Schicht und ist wortwörtlich ätzend. Damit am Institut für Halbleitertechnik etwa blaue LEDs aus Galliumnitrid (GaN) entstehen können, braucht es daher hochspezialisiertes Reinraum-Equipment. Mit zwei neuen Geräten öffnen sich jetzt weitere Wege für die Halbleitertechnik, von denen vor allem auch Verbünde wie das Exzellenzcluster QuantumFrontiers und das Quantum Valley Lower Saxony (QVLS) profitieren. Dahinter stehen mehrere Jahre Arbeit. Schließlich hat jede der Maschinen ihre Eigenheiten, denen nur ein Elektronenmikroskop auf die Schliche kommt.
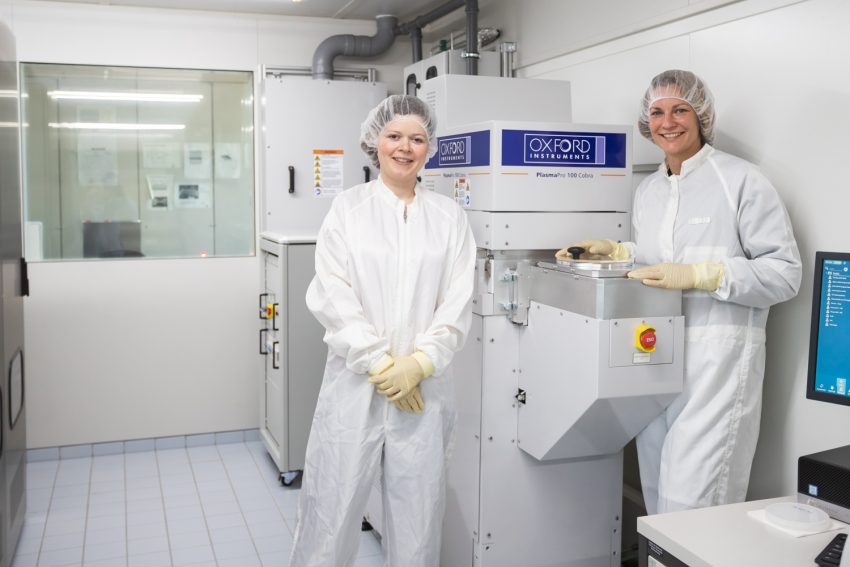
Dr. Jana Hartmann und Juliane Breitfelder (v.l.) im neu ausgestatteten Reinraum des Instituts für Halbleitertechnik. Bildnachweis: Max Fuhrmann/TU Braunschweig
Allein der Einbau der zwei neuen Großgeräte – Oxford Plasma Pro 100 und Plasma Pro 80 – ist kostenintensiv. Neue Gasanschlüsse, Druckminderer, Sicherheitstechnik und vieles mehr. Zusammen mit dem Preis für die Geräte kommen knapp eine Millionen Euro zusammen, finanziert vom Cluster QuantumFrontiers, der DFG und vom Institut für Halbleitertechnik der TU Braunschweig. Doch was machen diese Geräte überhaupt? Die Frage stellt man am besten Dr. Jana Hartmann. Als Nachwuchsgruppenleiterin koordiniert sie die Arbeit an den neuen Stars im Reinraum des Instituts.
Dr. Jana Hartmann: „Die Plasma Pro 80 ist eine ‚Plasma Enhanced Chemical Vapor Deposition‘, kurz PECVD. Mit ihr bringen wir dünne Halbleiterschichten auf Wafern auf, der Fertigungsplatte für Chips. Die Plasma Pro 100, eingesetzt für ‚reactive ion etching by inductively coupled plasma’ oder kurz RIE-ICP, ist auf dem Wafer für das Gegenteil verantwortlich: Sie ätzt Material gezielt mit Chlorgasen weg. Wer mit Chips arbeitet, braucht unbedingt beides. Entsprechend profitieren im Grunde alle Projekte des Instituts von den neuen Geräten.“
Chipentwicklung an einem Ort
Geätzt wurde im Institut auch schon vorher mit einer ICP. Allerdings mit Fluorgasen. Diese greifen aber Materialien wie Galliumnitrid und Aluminiumnitrid gar nicht chemisch an. Dabei stehen gerade diese Halbleiterverbindung als Basisstoffe für LEDs im Zentrum der Forschungsaktivitäten. „Wir haben bisher gewissermaßen falsch geätzt, um dennoch mit den Nitriden arbeiten zu können. Statt der passenden chemischen Komponenten nutzten wir vielmehr rohe Gewalt, um Material abzutragen. Entsprechend sahen die Ergebnisse aber auch aus – voller Defekte und Unebenheiten“, erklärt Dr. Hartmann. „Mit der neuen Trockenätzmaschine bekommen wir dagegen ganz glatte Oberflächen und Seitenwände in die Wafer geätzt und können auch viel tiefer strukturieren. Sogar das viel härtere Aluminiumnitrit, das wir für UV-LEDs brauchen, ist jetzt formbar. Früher war spätestens bei Galliumnitrid Schluss.“
- Ein Wafer kommt in die Vakuumschleuse der neuen Trockenätzmaschine. Bildnachweis: Max Fuhrmann/TU Braunschweig
- Im Innern ätzt das neue Großgerät mit Chlorgasen feine Strukturen in die eingeführten Halbleiter, wie Galliumnitrid. Bildnachweis: Max Fuhrmann/TU Braunschweig
Völlig neu am Institut ist dagegen die PECVD, die Siliziumoxid- oder Siliziumnitrid-Schichten auf die Wafer abscheidet. Bisher mussten die Forschenden am Institut ihre Wafer aus dem Reinraum rausholen und an Jemanden mit einer solchen Beschichtungsanlage verschicken. Abgesehen vom Aufwand sammeln die Wafer dabei unweigerlich Staub und Verunreinigungen. Jetzt kann dagegen alles in einem Reinraum bleiben.
Große Geräte für große Fortschritte
Was das konkret für ein Projekt bedeutet, zeigt die aktuelle Arbeit von Julian Kaßmann. Als Doktorand stellt er winzige, sogenannte Distributed Feedback Laser her. Die Laser sollen zukünftig Ionen in den Quantencomputern auslesen, die gerade im Quantum Valley Lower Saxony entstehen. Dafür kommen unter anderem feine Schichten aus Siliciumoxid auf die Wafer. Vor allem aber müssen filigrane, ebene Strukturen sehr tief in die Wafer geätzt werden. Jede Unebenheit würde den Laser ein Stück seiner Leuchtkraft kosten. Eine Zielsetzung, die erst mit den neuen Geräten überhaupt in Reichweite gerät.
Ebenso profitieren Aktivitäten im Exzellenzcluster QuantumFrontiers. Etwa ordnen die Forschenden Micro- und NanoLEDs in Rastern an, um schnelle, strukturierte Beleuchtung für verschiedenste Anwendungen zu entwickeln. Gerade wenn im Projekt SMILE die Galliumnitrid-Elemente auf einen CMOS-Chip kommen sollen, braucht es sehr dicht aneinanderliegende Kontakte. Die neue Trockenätzmaschine macht genau das möglich.
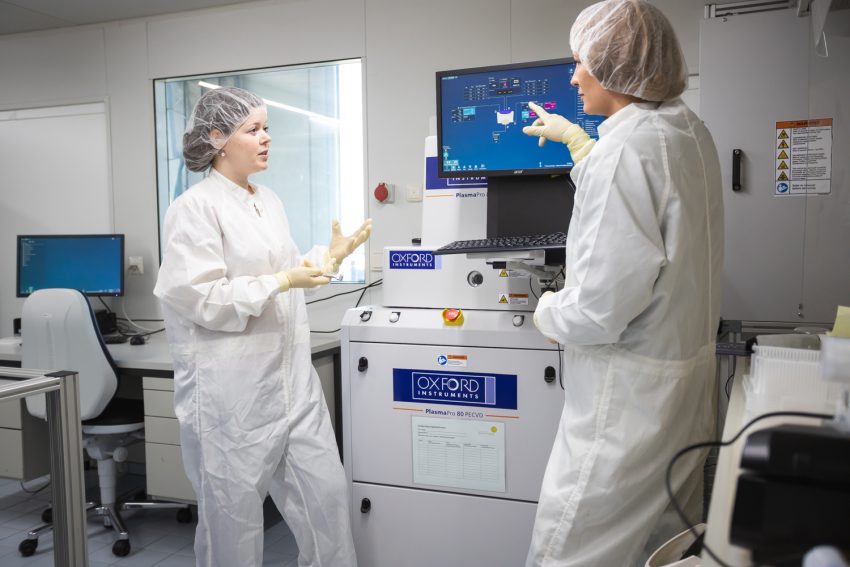
Während die eine Anlage ätzt, bringt diese PECVD neue Halbleiterschichten auf die Wafer des Instituts. Bildnachweis: Max Fuhrmann/TU Braunschweig
Auf dem Weg zum besten Halbleiter-Reinraum
Für Großgeräte wie die ICP und die PECVD gibt es kein universelles Nutzerhandbuch. Zwar machen die Anlagen grundsätzlich, was sie sollen. Die Ergebnisse aber hängen im Detail von vielen Faktoren ab (wie Leitungslänge, Gaszusammensetzung oder Abpumpraten). Entsprechend fahren die Forschenden am Institut aktuell die Geräte Stück für Stück ein und optimieren die Prozesse. „Da es dabei auf Nanometer ankommt, braucht man bereits ein Rasterelektronenmikroskop, um Ergebnisse zu kontrollieren. Wenn wir dann noch etwas wie den Flankenwinkel einer Ätzung kontrollieren wollen, müssen wir die Proben zusätzlich mit einer FIB durchschneiden. Gut, dass wir so viel High-End-Equipment im LENA haben!“, sagt Dr. Jana Hartmann.
Zukünftig sollen zudem noch weitere Investitionen folgen. Dr. Jana Hartmann: „Wir sind gerade dabei, einen neuen Elektronenstrahl-Aufdampfer und eine CMP (Chemical-Mechanical Polishing) zu beschaffen. Ersterer bringt Metalle auf Wafer, letztere bekommt selbst härteste Materialien wie Saphir poliert. Außerdem sind noch weitere Geräte in Planung. Zusammen mit den bereits vorhandenen Epitaxie- und Prozessierungsanlagen öffnen uns die ICP und die PECVD viele neue Wege, um optische Komponenten herzustellen. Die geplanten Ergänzungen werden die Qualität unserer Bauteile nochmals verbessern, was insbesondere für Laser in Quantencomputern den entscheidenden Unterschied macht.