Poren gegen Turbulenzen Treibstoff sparen durch neu gestaltete Flügeloberflächen
Forscherinnen und Forscher des Exzellenzclusters SE²A entwickeln neue Ideen für eine nachhaltige und energieeffiziente Luftfahrt. In verschiedenen Projekten wird das Flugzeug der Zukunft in fast jedem Detail analysiert und optimiert. Die beiden Nachwuchswissenschaftler Siby Jose und Hendrik Traub arbeiten zum Beispiel an verbesserten Tragflächen. Mit additiven Verfahren wollen sie Flügel mit besseren Strömungseigenschaften herstellen, um Verwirbelungen zu reduzieren und damit Treibstoff zu sparen.
Die Tragflächen eines herkömmlichen Flugzeugs weisen einige aerodynamische Nachteile auf. An der Flügelvorderkante ist die Luftströmung durch eine sogenannte laminare Strömung gekennzeichnet: Während hier die Luft die Form des Flügels glatt und ohne Wirbel umströmt, verändert sich kurz danach dieser Strömungszustand: Die Strömung beginnt chaotischere Bewegungen auszuführen, durch Wirbel wird eine laminare zu einer turbulenten Strömung. Durch die Änderung des Strömungszustandes erhöht sich der Luftwiderstand, was wiederum zu einem höheren Treibstoffverbrauch führt.
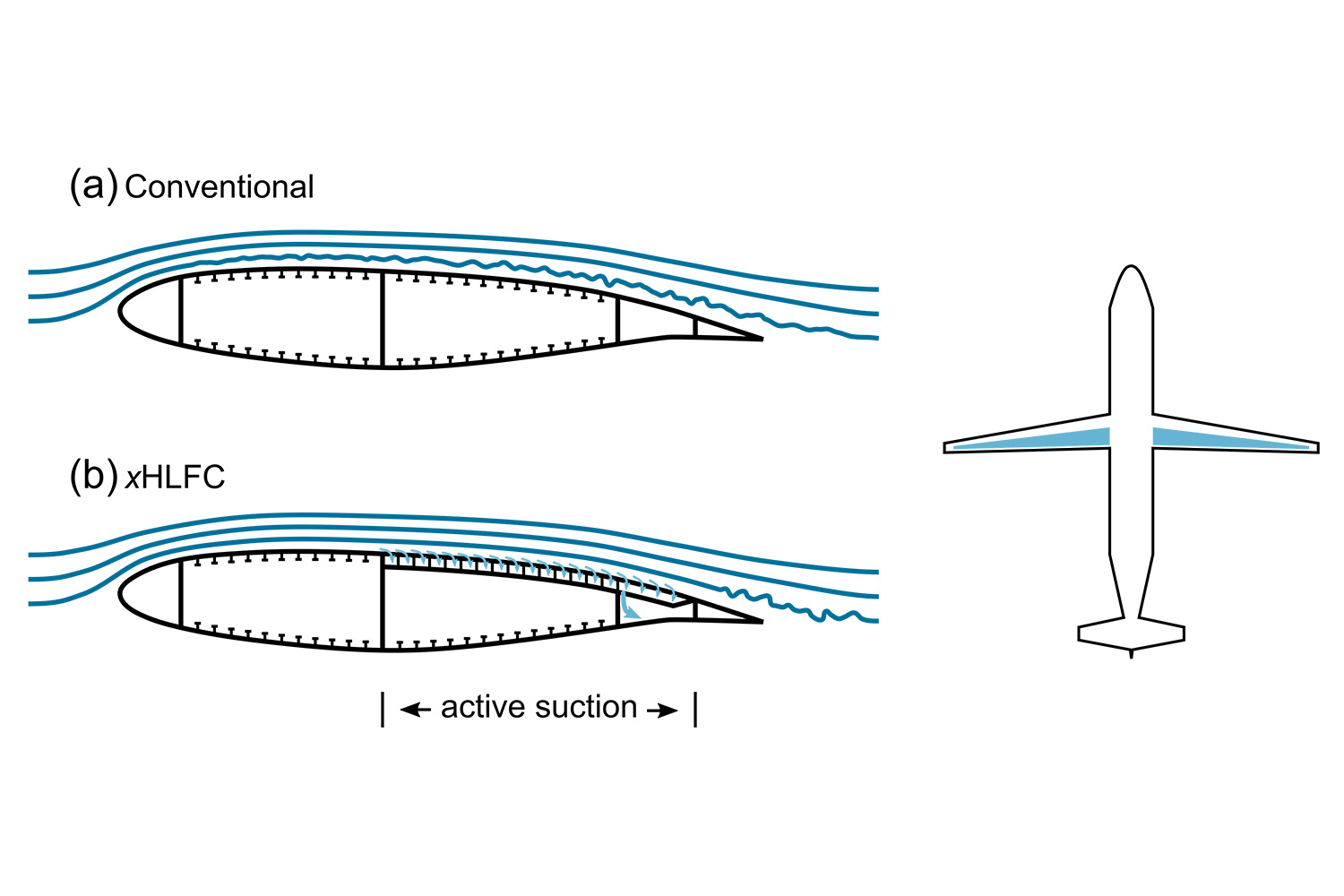
(a) Luftströmung eines konventionellen Flugzeugs mit chaotischen Luftbewegungen entlang der Tragfläche. (b) Ansatz im Exzellenzcluster: Tragfläche mit laminarer Strömung und einem aktiven Saugsystem für einen verzögerten Übergang. Bildnachweis: Hendrik Traub/TU Braunschweig
Strömung am Flügel stabiliseren
Ein Ziel des Exzellenzclusters SE²A ist deshalb, die laminare Strömung aufrechtzuerhalten und den Übergang zu chaotischen Bewegungen zu verzögern. Eine Idee besteht darin, eine Art Luftabsaugung am hinteren Teil des Flügels zu realisieren, bei dem die Strömung ansonsten turbulent umschlagen würde. Hierfür wird eine Porenoberfläche auf dem Tragwerk angebracht, um die Strömung durch Absaugung zu stabilisieren und den laminaren Strömungszustand aufrecht zu erhalten.
3D-Druck komplexer Strukturen
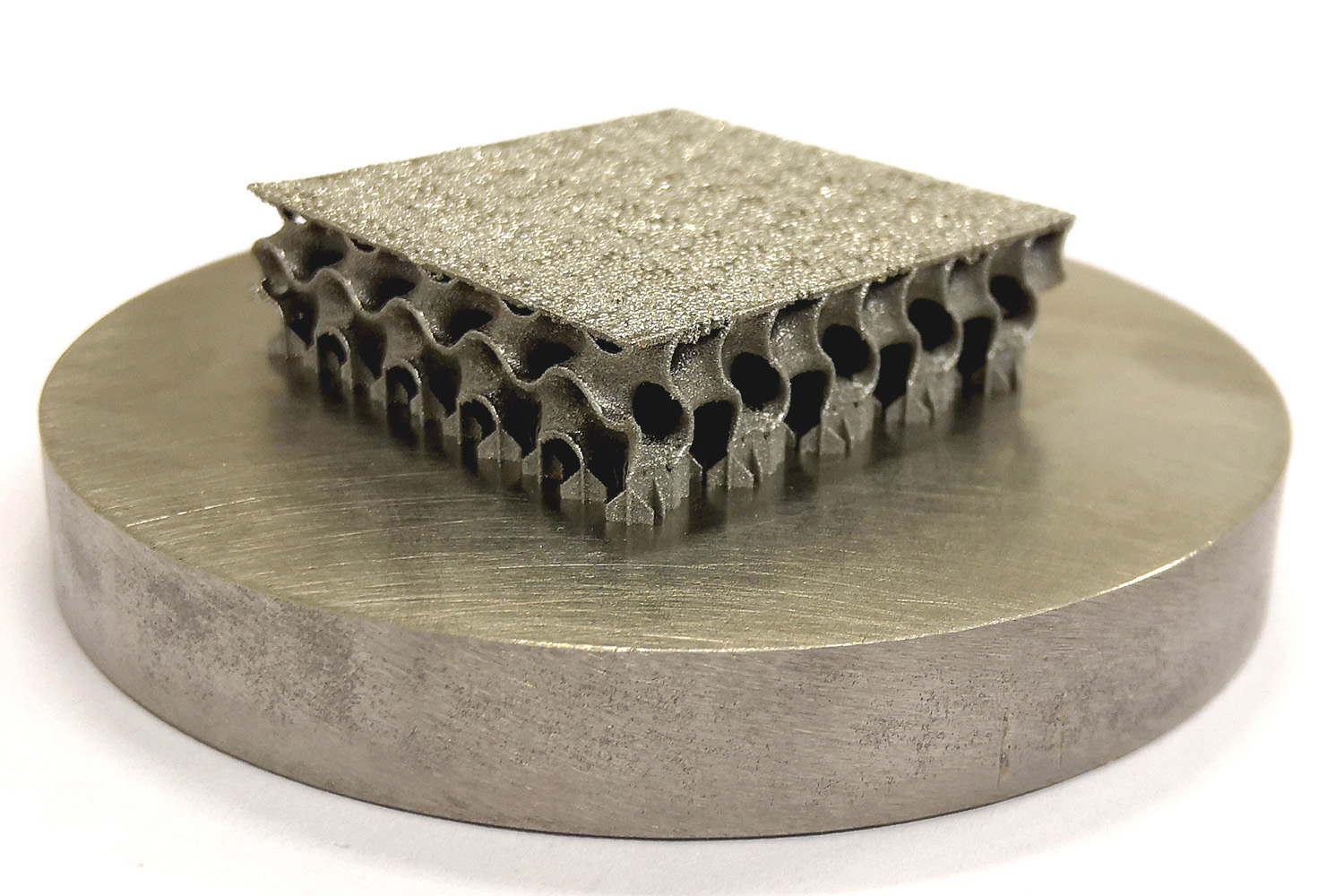
Titanteil, gefertigt mit dem 3D-Druckverfahren Selective Laser Melting-Technologie (SLM). Sichtbar ist die Hautstruktur, die submillimetergroße Löcher zur Druckverteilung aufweist, sowie die TPMS-Unterstruktur, die die Außenhaut des Flügels stützt. Bildnachweis: Siby Jose/TU Braunschweig
Allerdings ist die Herstellung eines solchen Flügelaufbaus nicht ganz einfach. Die beiden Nachwuchsforscher Siby Jose und Hendrik Traub gehen die Herausforderungen in der Fertigung des optimierten Flügels an.
Um die spezifische Druckverteilung für die Absaugung zu modellieren, schlagen sie komplexe innere Strukturen des Flügels vor. Da die traditionellen Herstellungstechniken in der Ausführung dieser Strukturen begrenzt sind, wählen sie den 3D-Druck als additive Fertigungsmethode.
Verschiedene Druckverfahren
Die beiden arbeiten vor allem im Metalldruck mit der Selective Laser Melting-Technologie (SLM) sowie beim Kunststoffdruck mit der Stereolithographie (SLA) sowie der Fused Deposition Modeling (FDM)-Technologie. Beim Selektiven Laserschmelzen wird schichtweise der Werkstoff in Pulverform dünn auf einer Grundplatte aufgebracht und mit Laserstrahlung aufgeschmolzen. Die Stereolithographie ist ebenfalls eine laserbasierte Technologie. Als Werkstoff wird ein UV-empfindliches Flüssigharz verwendet. Beim Druckvorgang härtet ein UV-Laserstrahl das Harz selektiv – entsprechend dem Querschnitt des Objektes – Schicht für Schicht aus. Bei der Schmelzschichtung (FDM) wird ein Objekt schichtweise aus einem schmelzfähigen Kunststoff hergestellt.
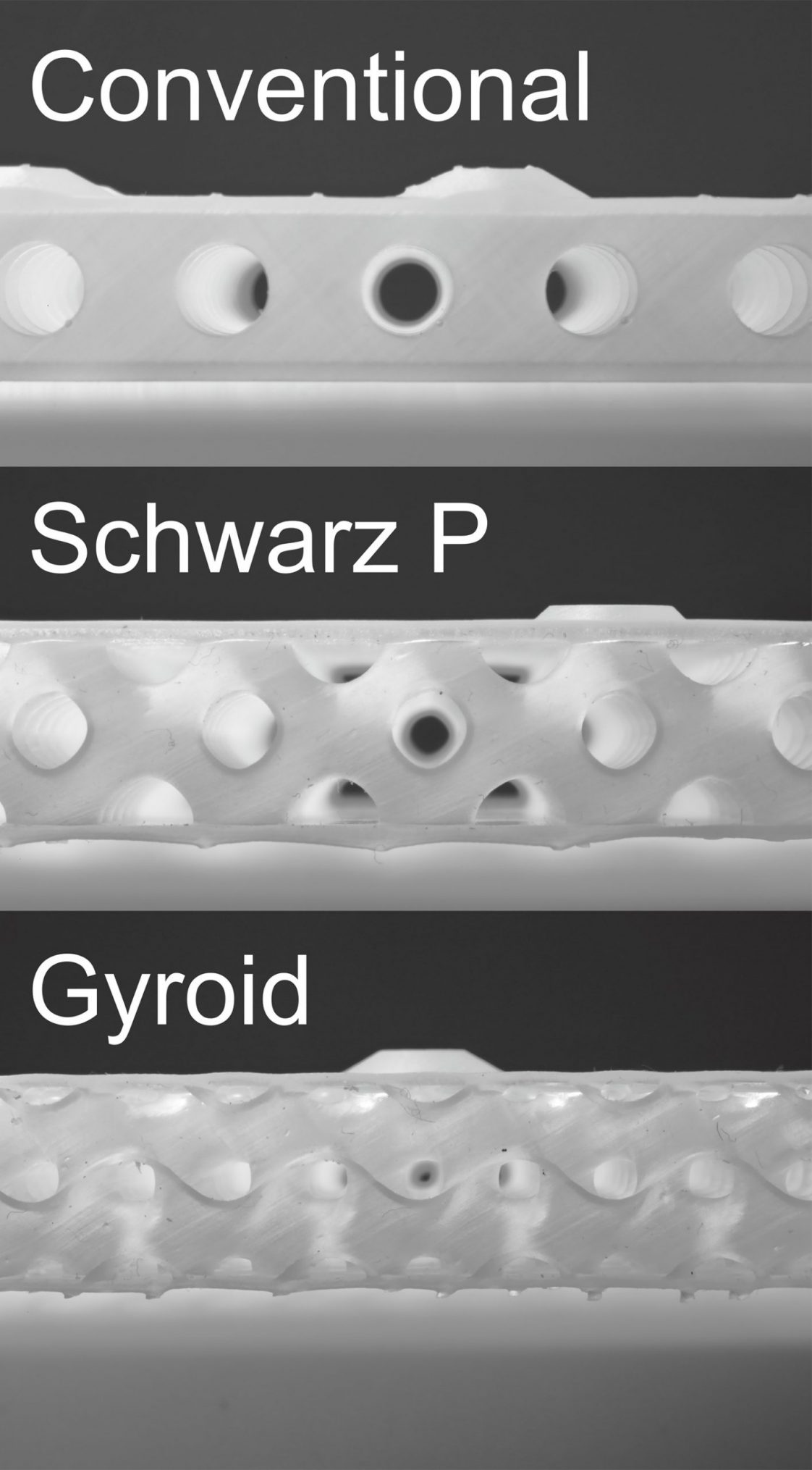
Strukturen innerhalb des Flügels: Konventionelle und TPMS-Designs (Schwarz P und Gyroid), hergestellt mit dem 3D-Druckverfahren Stereolithographie (SLA). Bildnachweis: Hendrik Traub/TU Braunschweig
Jose und Traub haben die drei Verfahren hinsichtlich der aerodynamischen Eigenschaften ihrer gedruckten Strukturen verglichen. Aktuell wird außerdem an der Optimierung der submillimetergroßen Löcher der Haut gearbeitet, die die spezifische Druckverteilung für die Luftansaugung liefern. Dazu müssen Prozessparameter wie Laserfleckgröße und Geschwindigkeit des Lasers variiert werden, um den komplexen Herstellungsprozess zu ermöglichen. Für die innere Struktur werden verschiedene Designs verglichen, um die am besten geeignete Struktur mit guten strukturellen und aerodynamischen Eigenschaften zu erhalten.
“Gegenwärtig untersuchen wir auch Eigenschaften von Triply Periodic Minimal Surfaces (TPMS) als Sandwich-Kernstrukturen im Leichtbau und die Möglichkeit, sie als Luftkanäle im Flügelbau zu verwenden“, sagt Traub. TPMS-Strukturen könnten als dreidimensionale Stützstruktur eingesetzt werden und auch den Transport von Medien wie Luft im Inneren des Bauteils ermöglichen – im Vergleich zum Beispiel zu herkömmlichen Wabenstrukturen.
„Nach der Optimierung des Saugsystems hinsichtlich aerodynamischer und struktureller Eigenschaften testen wir die gesamte Konstruktion im Windkanal, um weitere Ideen für die Optimierung zu erhalten“, so Jose.
Text: Siby Jose, Hendrik Traub