Ein Koloss für den Leichtbau TU Braunschweig weiht Testanlage für große Leichtbauteile ein
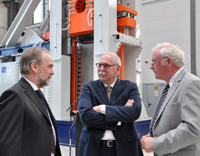
Prof. Dr.-Ing. Peter Horst, Leiter des Instituts für Flugzeugbau und Leichtbau, Prof. Dr.-Ing. Matthias Kleiner, Präsident der DFG, Prof. Dr.-Ing. Jürgen Hesselbach, Präsidenten der TU Braunschweig
Leichtbauverfahren haben ein hohes Zukunftspotenzial im Flugzeug- und Fahrzeugbau. Sie können dazu beitragen, dass das Fliegen und Fahren günstiger, energieeffizienter und gleichzeitig sicherer werden. Forscher und Entwickler arbeiten daher mit Hochdruck an neuen Faserverbundwerkstoffen, neuen Bauweisen und entsprechend neuen Fertigungskonzepten. Wie aber kann man die im Leichtbau häufig sperrigen und großen Bauteile für künftige Flugzeuge und Fahrzeuge unter realistischen Bedingungen testen?
Mit der von der Deutschen Forschungsgemeinschaft geförderten neuen „Multiaxialen Panel Testanlage“ der Technischen Universität Braunschweig wird dies möglich. Eine vergleichbare Technologie stand bisher in Deutschland nicht zur Verfügung. Die etwa 1,3 Millionen Euro teure und beeindruckende 7,4 Meter hohe Prüfmaschine wurde heute, am Mittwoch, 2. Mai 2012, feierlich eingeweiht.
Zum Hintergrund:
Die TU Braunschweig war bei der Deutschen Forschungsgemeinschaft (DFG) im Rahmen der Großgeräteinitiative „Prüfanlagen für Lastkombinationen zur Lebensdauervorhersage von komplexen Leichtbaustrukturen“ erfolgreich. Das Institut für Flugzeugbau und Leichtbau (Prof. Peter Horst) und das Institut für Füge- und Schweißtechnik (Prof. Klaus Dilger) sowie das Institut für Faserverbundleichtbau und Adaptronik des DLR (Prof. Martin Wiedemann) haben dabei einen der zwei deutschlandweit erfolgreichen Anträge gestellt. Die Anlage wurde an der TU Braunschweig selbst entwickelt und wird künftig beim Test großer und komplexer Leichtbaustrukturen zum Einsatz kommen. Bislang war es in Deutschland nur unter eng umrissenen Randbedingungen (Platten oder Schalen) möglich, die Belastbarkeit solcher Bauteile zu prüfen und den Nachweis ihrer Sicherheit zu erbringen.