Neues Bauen: extrem leicht, extrem frei, extrem gedruckt Professor Dirk Lowke über eine Vision für die Bauwirtschaft
Wie können wir mit Beton eine extrem leichte räumliche Gebäudestruktur drucken? Daran forschen das Institut für Baustoffe, Massivbau und Brandschutz (iBMB) und das Institut für Tragwerksentwurf (ITE) der TU Braunschweig. Wir haben mit Professor Dirk Lowke, Leiter des Fachgebiets Baustoffe am iBMB, über das Projekt „Beyond 3D Printing“ gesprochen.
Herr Professor Lowke, der Titel Ihres Forschungsprojekts ist „Beyond 3D Printing“. Was bedeutet „beyond“ in diesem Zusammenhang?
Wenn wir das 3D-Drucken genauer betrachten, fällt auf, dass wir eigentlich nicht in 3D drucken. Wir können immer nur auf eine bestehende Schicht draufdrucken. Im einfachsten Fall drucken wir also vertikal nach oben oder – wenn wir etwas mutiger sind – versetzen wir die Schichten etwas, so dass eine schräge Struktur entsteht. Letzten Endes ist dies dann „2,5D-Drucken“. Mit dem Verfahren, das wir im Projekt entwickeln, sind wir jedoch wirklich frei in der Positionierung des Materials. Wir können die Struktur in einer beliebigen Ausrichtung in den Raum hineindrucken. Das wäre dann das „echte“ 3D-Drucken, eine Materialisierung im Raum. Das ist der entscheidende Unterschied. Das gibt es so im Bauwesen bislang nicht. In anderen Bereichen verfolgt man solche Ansätze bereits in der Forschung, zum Beispiel in der Medizin, wo Gewebestrukturen gedruckt werden sollen.
Hätten Sie ein Beispiel aus dem Bauwesen?
Das erste 3D-gedruckte Haus ist ein schönes Beispiel. Es ist vertikal nach oben Strang für Strang aufgesetzt. Aber bei der Fensteraussparung steht man vor einem Problem: Was mache ich, wenn ich am oberen Ende des Fensters angekommen bin? An dieser Stelle kann ich nicht einfach nach oben in die Luft drucken. Hier werden die Grenzen des Schichtverfahrens deutlich.
In Ihren Versuchen drucken Sie zunächst im kleinen Maßstab Strukturen mit dem „Injection 3D Concrete Printing“ einen Betonstrang in ein Stütz-Gel hinein. Wie könnte das Verfahren in der Bauindustrie angewandt werden?
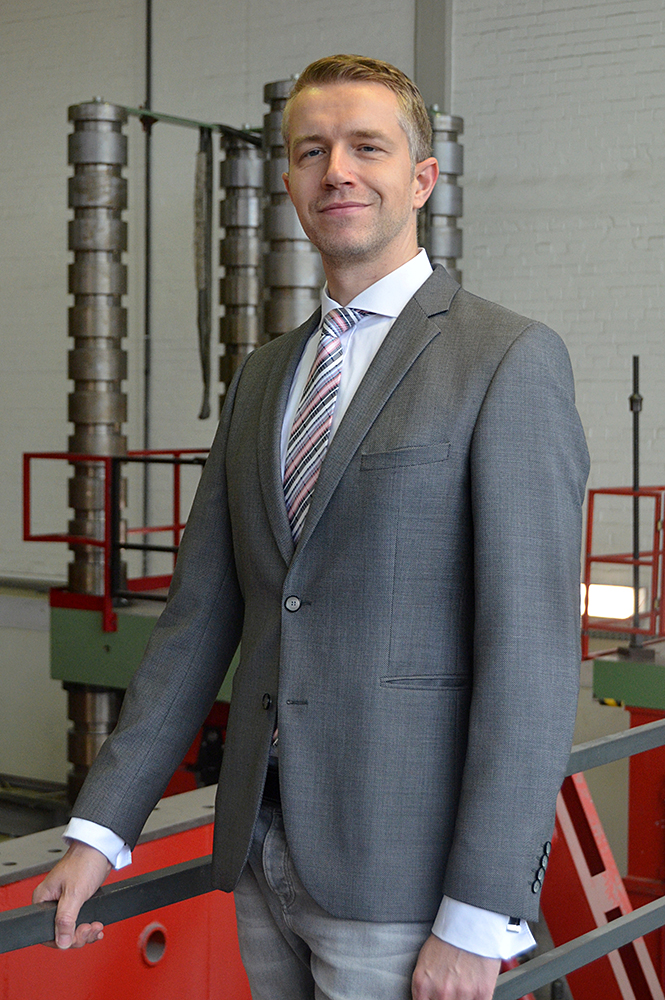
Professor Dirk Lowke leitet das Fachgebiet Baustoffe des Instituts für für Baustoffe, Massivbau und Brandschutz (iBMB). Bildnachweis: Daniela Klar/TU Braunschweig
Für eine großtechnische Anwendung ist das Gel natürlich weniger geeignet, weil es unter anderem sehr teuer ist. Wir ersetzen das Gel durch eine mineralische Suspension, die günstiger ist, ökologisch unschädlich und in großem Maßstab recycelbar. Die Trägerflüssigkeit – eine Gesteinsmehlsuspension, die ähnlich wie eine Schlammpackung aussieht – kann abgelassen und wiederverwendet werden.
Der Fokus liegt auf dem Fertigteilbau, zum Beispiel von Brückenbauteilen. Die einzelnen Segmente werden in der Fabrik gedruckt, zum Baugeschehen transportiert und vor Ort zusammengefügt. In der Fabrik benötigt man dann einen entsprechend großen Container, um diese Fertigteile herzustellen.
Doch zunächst wollen wir hier an der TU Braunschweig in größerem Maßstab drucken. Das Digital Building Fabrication Laboratory (DBFL) des Instituts für Tragwerksentwurf (ITE) hat entsprechende Abmessungen, um solche Strukturen und Fertigteile drucken zu können.
Vor zwei Jahren haben Sie das Injection 3D Concrete Printing patentieren lassen.
Ja, genau. Unser Patent (gemeinsam mit Professor Norman Hack und Professor Harald Kloft) geht noch über das hinaus, was ich bereits berichtet habe. Das Trägermaterial, in welches die freie Struktur gedruckt wird, könnte auch ein sehr günstiger und ökologisch wenig belastender Beton sein. Damit könnte man den Container füllen, der bereits die Form eines normalen konventionellen Bauteils hat, wie zum Beispiel einen Balken, den ich von einer Stütze zur nächsten lege. Da der weniger leistungsstarke Beton die Last nicht abtragen kann, würden wir in dieses Trägermaterial dann eine räumliche Struktur mit einem Hochleistungs-Beton eindrucken. Wir haben damit in dem günstigen Beton einen sehr hochleistungsfähigen Beton versteckt, der für den Lastabtrag verantwortlich ist.
Wie ist die Idee zum Forschungsprojekt entstanden?
Tatsächlich hatte ich die grundlegende Idee dazu schon länger, weil ich als „Materialmensch“ die Möglichkeit sehr spannend finde, etwas in den Raum drucken zu können. Allerdings hatte ich nicht die Vision, was ich damit großtechnisch anfangen könnte. Als ich dann mit Professor Norman Hack und Professor Harald Kloft vom ITE des Architekturdepartments darüber ins Gespräch kam, war die Idee des Forschungsprojekts schnell geboren. Im Bereich der additiven Fertigung ist es wichtig, interdisziplinär zu arbeiten. In diesem Gebiet kommt man mit einer Einzelexpertise nicht sehr weit. Ich kann als Bauingenieur den Beton zwar in Flüssigkeit schweben lassen, aber der Architekt kann mir sagen, was daraus entstehen und wie ich diese räumlichen Strukturen in der Architektur nutzen kann. Und er kann sich vorstellen, wie wir das in großem Maßstab am DBFL umsetzen. Der Austausch mit verschiedenen Disziplinen funktioniert hier sehr gut.
Wie sehen die weiteren Pläne aus?
Wenn das Forschungsvorhaben erfolgreich ist, ist es eine Option, das Injection 3D Concrete Printing in der nächsten Förderphase des Sonderforschungsbereichs TRR 277 „Additive Manufacturing in Construction (AMC) – The Challenge of Large Scale“ zu etablieren. Wir hoffen, mit dem Projekt zeigen zu können, dass das Verfahren eine ernsthafte Vision für die Bauwirtschaft ist. Innovative Forschung braucht Mut!