Der Schlüssel für eine digitale und nachhaltige Bauwirtschaft Forscherteam der TU Braunschweig über die „Digitale Baustelle“
Ressourceneffizienz, weniger Emissionen, kürzere Bauphasen, verbesserte Arbeitssicherheit – was wie ein Potpourri aus Wünschen für die Bauwirtschaft klingt, könnte die „Digitale Baustelle“ bald möglich machen. Mit dem Projekt wollen die Forschenden Möglichkeiten für eine zukünftige Baustelleninfrastruktur aufzeigen und auch die regionale und überregionale Wirtschaft einbinden. Einen ersten Einblick erhielten Unternehmen am 11. April beim Innovationsforum „Additive Fertigung/3D-Druck“, das vom TransferHub der TU Braunschweig und der Ostfalia Hochschule, der Braunschweig Zukunft GmbH und der IHK Braunschweig organisiert wurde. Mit dem Forschungsteam der „Digitalen Baustelle“ haben wir über ihre Zukunftsvision, ein neues Erscheinungsbild von Bauwerken, Veränderungen für Fachkräfte und Herausforderungen bei den Baustoffen gesprochen.
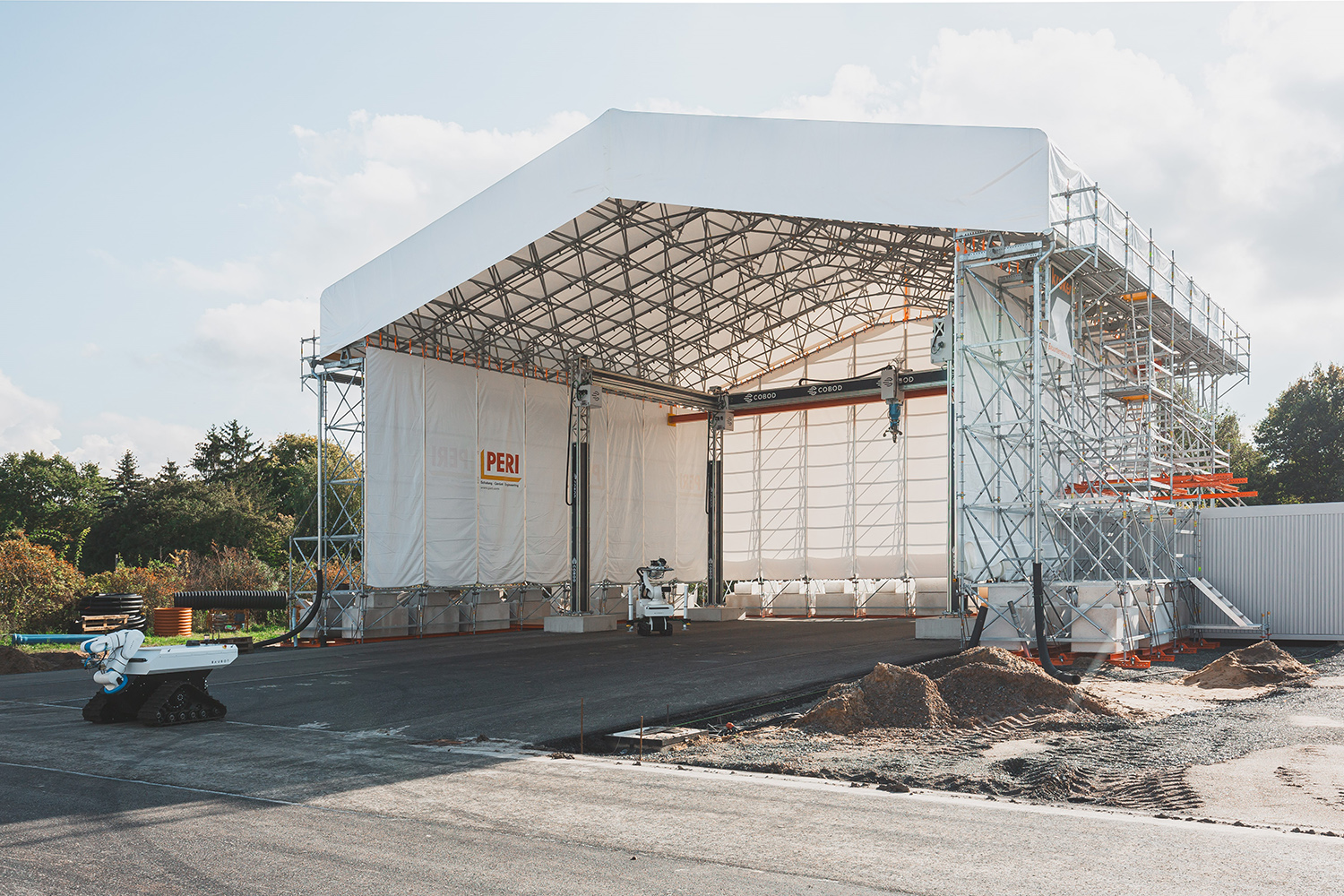
Eine ähnliche Digitale Baustelle wie an der TU Braunschweig könnte in Zukunft Wirklichkeit werden. Bildnachweis: Tjark Spille/Institut für Tragwerksentwurf
Bei der „Digitalen Baustelle“ denkt man zunächst nur an Häuser aus dem 3D-Drucker. Aber was steckt genau dahinter?
Prof. Harald Kloft: Die durchgängige Digitalisierung des Bauens ist der Schlüssel, um die Bauwirtschaft in eine produktive und nachhaltige Zukunft zu führen. Während für die Planung leistungsfähige Software zur Verfügung steht und auch im operativen Gebäudebetrieb der Einsatz digital gesteuerter Komponenten mit Hochdruck voranschreitet, ist die Baustelle größtenteils noch traditionell handwerklich organisiert. Der Austausch von Informationen mit den Baustellen erfolgt daher in der Regel dokumentenbasiert, häufig noch in Form von ausgedruckten Plänen. Die Digitalisierung der Baustellen ist also das Bindeglied, um die durchgängig digitalen Prozessketten – von der Planung über die Ausführung bis zum Betrieb von Bauwerken – zu erreichen. Und das 3D-Drucken ist in diesem Zusammenhang eine digitale Schlüsseltechnologie. Warum? Der 3D-Druck ermöglicht automatisierte, digital gesteuerte Prozesse, wie wir sie bisher nur aus der Serienfertigung kennen, bei gleichzeitig individualisierter, materialeffizienter und abfallarmer Fertigung. Damit ist das 3D-Drucken ideal für das Bauwesen, da Ökonomie, Ökologie und soziale Aspekte, wie zum Beispiel die Reduzierung der physischen Belastung, zusammengeführt werden.
Auf der „Digitalen Baustelle“ werden wir schwerpunktmäßig zunächst an den digitalen Schnittstellen zwischen Planung und Fertigung forschen sowie das 3D-Drucken mit Beton, aber auch mit Stahl und Lehm unter Realbedingungen im Maßstab 1:1 testen. Hierzu stehen uns ein stationärer Portaldrucker, mehrere mobile Roboter, Tracking Systeme und immersive Technologien zur Verfügung. Zwei Dinge sind uns bei der Digitalisierung der Baustelle besonders wichtig: erstens die Arbeitsabläufe, hiermit können innovative Ansätze bei der Bauproduktion verfolgt werden. Im Bauwesen sind wir sequentielle Prozesse gewohnt. Erst wird geplant, dann wird gebaut – und zwar idealerweise genauso, wie geplant wurde. Handwerkliche Imperfektionen werden aber mitunter erst im Nachhinein identifiziert und die Planung kann hierauf nicht reagieren. In digitalen Bauprozessen haben wir die Möglichkeit, die Fertigung sensorbasiert zu überwachen. Dadurch erhalten wir permanent Informationen über den Baufortschritt und können diese als Feedback in die Planung geben. Durch dieses Interagieren zwischen Planung und Fertigung können bei etwaigen Abweichungen umgehend planerische Maßnahmen getroffen werden. Der zweite Punkt betrifft die Arbeitsbedingungen. Der Mensch wird in unseren Vorstellungen weiterhin die zentrale Rolle auf den Baustellen spielen, aber dazu kann Ihnen Herr Schwerdtner sicher mehr erzählen.
Herr Professor Schwerdtner, wie verändert die „Digitale Baustelle“ die Arbeit vor Ort?
Prof. Patrick Schwerdtner: Um den Menschen in digital organisierte Baustellen zu integrieren, werden sich die Anforderungsprofile entscheidend verändern müssen. Man benötigt nicht mehr (nur) Fachkräfte zur Ausführung handwerklicher Tätigkeiten. Es entstehen neue Arbeitsfelder, die andere Kenntnisse und Kompetenzen erfordern. Mit Augmented Reality (AR) ist der Mensch jederzeit in der Lage, Teil der digitalen Fertigungsprozesse zu sein. Wir werden also qualitativ hochwertige Arbeitsplätze haben, die auch hinsichtlich Arbeitssicherheit und Gesundheitsschutz auf einem höheren Niveau sein werden und eine neue Attraktivität für die Bauberufe hervorbringen.
Dennoch ist jede Baustelle anders und die Projekte erfordern eine individuelle Anpassung der digitalen Prozesse an die Randbedingungen. Ein vollständiger Ersatz handwerklicher Tätigkeiten durch robotische Systeme ist derzeit schwer vorstellbar.
Früher hätte man vor diesen Entwicklungen gewarnt und mit der Gefährdung von Arbeitsplätzen argumentiert. Mittlerweile wissen die Unternehmen, dass ihnen mittel- und langfristig nicht mehr genügend Arbeitskräfte zur Verfügung stehen, um den großen Herausforderungen im Bauwesen mit tradierten Fertigungsmethoden gerecht zu werden. Deshalb müssen die Entwicklung robotischer Systeme einerseits und die Optimierung konventioneller Prozesse durch digitale Methoden andererseits zum Ziel haben, die Arbeitsproduktivität zu erhöhen.
Die „Digitale Baustelle“ verändert nicht nur die Arbeitsprozesse. Welche Auswirkungen könnte die „Digitale Baustelle“ auf das optische Erscheinungsbild von Bauwerken haben?
Prof. Norman Hack: Die Formensprache von 3D-gedruckter Architektur wird sich erst im Laufe der Zeit entwickeln; so wie dies auch in der Vergangenheit bei vielen anderen Baumaterialien und -techniken der Fall war. Der Übergang von Holz zu Stein in der antiken griechischen Architektur ist ein faszinierendes Beispiel dafür, dass technologische und materielle Fortschritte im Bauwesen nicht unbedingt zu einer unmittelbaren Abkehr von etablierten ästhetischen und strukturellen Normen führen. Stattdessen kommt es häufig zu einer Vermischung des Neuen mit dem Traditionellen, was ein komplexes Wechselspiel zwischen Innovation, Tradition und Zweckmäßigkeit in der architektonischen Entwicklung widerspiegelt.
Klar ist jedoch, dass wir nicht mehr wie bisher an den rechten Winkel gebunden sind, und dass Wandkonstruktionen nicht mehr zwingend massiv sein müssen. Mit dem 3D-Druck können wir Material an den Stellen verdrucken, wo es tatsächlich strukturell gebraucht wird.
Stichwort Klimaschutz und nachhaltige Entwicklung: Welchen Beitrag kann die Digitalisierung auf der Baustelle hier leisten?
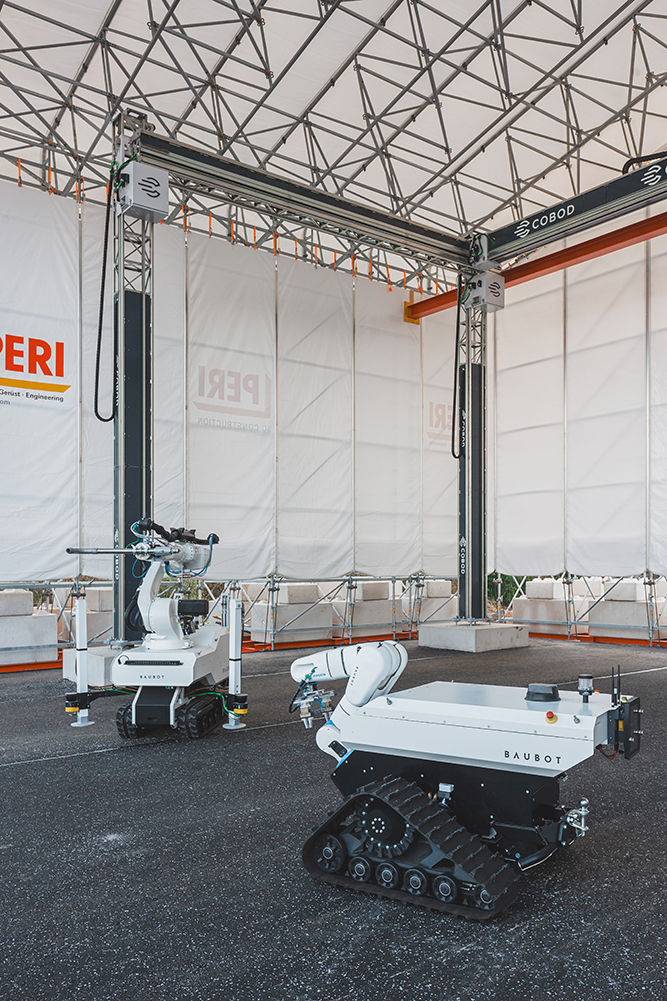
Neben dem stationären Portaldrucker stehen auch mehrere mobile 3D-Drucker zur Verfügung. Bildnachweis: Tjark Spille/Institut für Tragwerksentwurf
Prof. Dirk Lowke: Unsere Gebäudeinfrastruktur hat durch Herstellung und Betrieb einen unrühmlichen Spitzenwert bei den CO2-Emissionen. Wichtig ist, dass wir Gebäude so entwerfen, dass sie bei der Erstellung weniger Ressourcen benötigen, eine möglichst lange Lebensdauer besitzen und im Betrieb weniger Energie benötigen. Beim Thema Materialeffizienz kann die additive Fertigung einen signifikanten Beitrag leisten, indem man beispielsweise nicht mehr die gesamte Schalung für ein Bauteil mit Beton füllen muss, sondern – wie bereits von Herrn Hack erwähnt – den Beton nur noch dorthin druckt, wo er statisch erforderlich ist. Dadurch können wir bis zu 70 Prozent der erforderlichen Ressourcen einsparen. Aber natürlich geht es uns auch darum, die additive Fertigung mit neuen Baustoffen mit deutlich geringeren CO2-Emissionen, wie klinkerreduzierte Öko-Betone oder Geopolymere, zu erforschen.
Das Thema Nachhaltigkeit beinhaltet aber auch die ökonomischen und sozialen Komponenten. Ökonomische Nachhaltigkeit bedeutet, dass wir die Produktivität erhöhen und mit weniger Ressourceneinsatz das Ziel erreichen, sodass es monetär günstiger wird. Damit werden auch nur solche Produktionsprozesse überleben, die mittel- bis langfristig ökonomisch vernünftig sind. Hier ist die „Digitale Baustelle“ der richtige Ansatz, da wir in Zukunft einfach zu wenig Ressourcen haben werden – sowohl bei den Arbeitskräften als auch beim Material.
Die soziale Nachhaltigkeit sehen wir vor allem in den Bereichen Arbeitssicherheit und Gesundheitsschutz. Durch den Einsatz additiver Fertigung und anderer digitaler Technologien ist die körperliche Belastung für dieFacharbeiter*innen auf der Baustelle geringer und die Menschen sind länger arbeitsfähig. Das ist auch insbesondere wichtig, da unsere Sommer immer heißer werden und auf den Baustellen nur mit sehr begrenzter Produktivität gearbeitet werden kann, weil man mehr Pausen benötigt oder in die Randzeiten ausweichen muss. Maschinen ist nicht ganz so wichtig, wie heiß es ist.
Mit welchen anderen Baustoffen als Beton soll im Projekt gearbeitet werden? Welche besonderen Herausforderungen gibt es hier?
Prof. Dirk Lowke: Neben dem Drucken von Beton ist beispielsweise auch der 3D-Druck mit weniger CO2 intensiven Baumaterialen wie Lehm möglich. Dieses natürliche Material ist allerdings schwerer zu kontrollieren als das stark standardisierte und normierte Baumaterial Beton. Besondere Herausforderungen hierbei sind beispielsweise der Strukturaufbau während des Druckens, das Schwinden beim Trocknen des Materials, und die geringere Druckfestigkeit und Dauerhaftigkeit von erdbasierten Materialien.
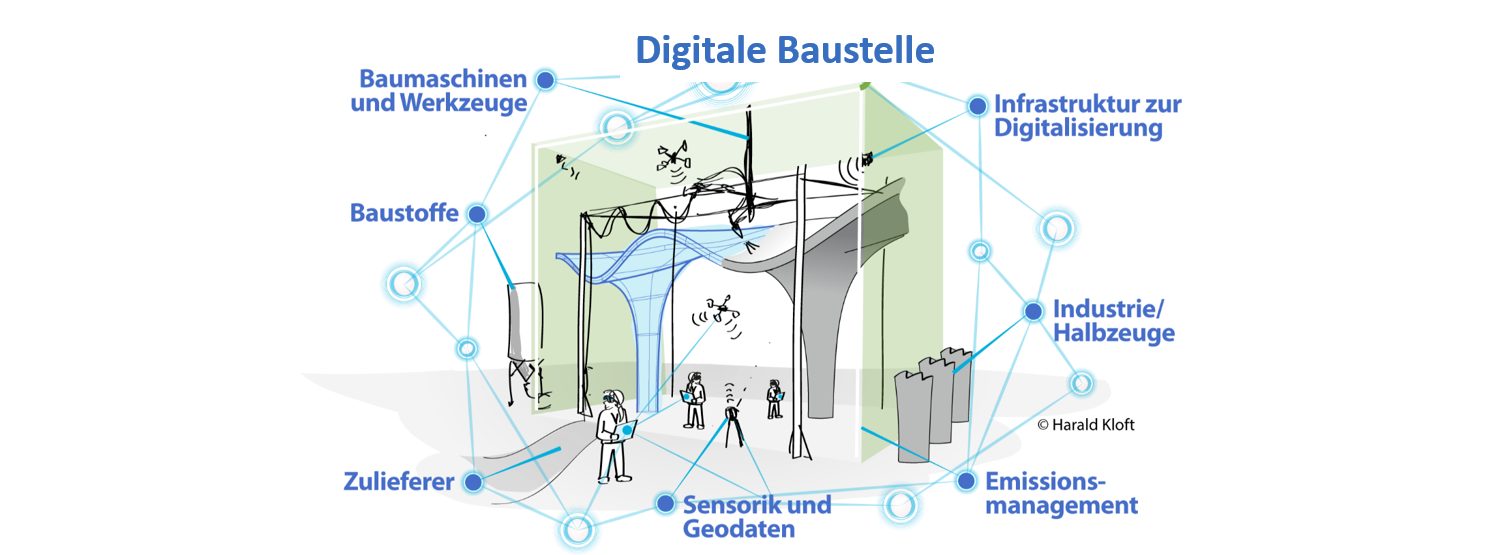
Unterschiedliche digitale Technologien werden vor Ort zusammenführt und im Sinne der Industrie 4.0 vernetzt. Bildnachweis: Harald Kloft/TU Braunschweig
On-Site und In-situ Drucken – wo bestehen die Unterschiede und wie soll es auf der „Digitalen Baustelle“ umgesetzt werden?
Prof. Norman Hack: Das in situ Drucken ist ein Konzept, bei dem das Bauteil an Ort und Stelle hergestellt wird, und dort auch nach dem Drucken verbleibt. Das Bauteil wird also nach dem Druck nicht mehr bewegt. Diese Strategie eignet sich insbesondere für vertikale Bauteile wie Wände und Stützen.
On-Site Drucken hingegen bedeutet, dass ein Bauteil zwar auf der Baustelle gedruckt wird, aber dann noch in seine finale Position gebracht werden muss. Hier kann man als Referenz die Feldfabrik nennen. Im Kontext der „Digitalen Baustelle“ könnte man sich beispielsweise vorstellen, dass horizontale Deckenelemente mit mobilen Robotern in einem Abschnitt neben dem eigentlichen Gebäude gedruckt werden, und erst nach dem Aushärten auf die Wände gehoben werden. So könnte die Produktion parallelisiert und der Baufortschritt beschleunigt werden.
Herr Professor Gerke, Sie beschäftigen sich im Projekt mit der Vermessungssensorik. Wird diese bereits jetzt auf Baustellen eingesetzt? Und welche Änderungen sehen Sie im Kontext der „Digitalen Baustelle“?
Prof. Markus Gerke: Auf „traditionellen“ Baustellen kommt die Vermessung zu bestimmten Fertigungszeitpunkten ins Spiel, zum Beispiel bei der Absteckung von Gebäudeachsen oder bei der Feinvermessung für die Integration bestimmter Bauteile. Durch die manuelle Bauweise können geometrische Baufehler innerhalb bestimmter Toleranzen ausgeglichen werden.
Auf der „Digitalen Baustelle“ ist jedoch eine tiefgehende Integration moderner, hochgenauer Vermessungssensorik und -methodik in allen Arbeitsschritten notwendig. Zum Beispiel müssen die automatisierten Bauprozesse vor Ort auch im Hinblick auf die korrekte Position gesteuert werden. Weiterhin ist es angezeigt, die Qualität der gefertigten Teile zeitnah zum Druckprozess sicherzustellen, damit Folgeprozesse optimal gesteuert werden können, denn die manuelle Korrektur von Bauteilen im Nachhinein ist nicht möglich. Weitere interessante Forschungsfragen drehen sich um die vollständige Integration dieser Technologien, auch bei unterschiedlichen Wetterbedingungen auf der Baustelle oder die Sicherstellung von Arbeitssicherheit durch die Nachverfolgung aller Akteure, damit „Mensch und Maschine“ optimal zusammenarbeiten können.
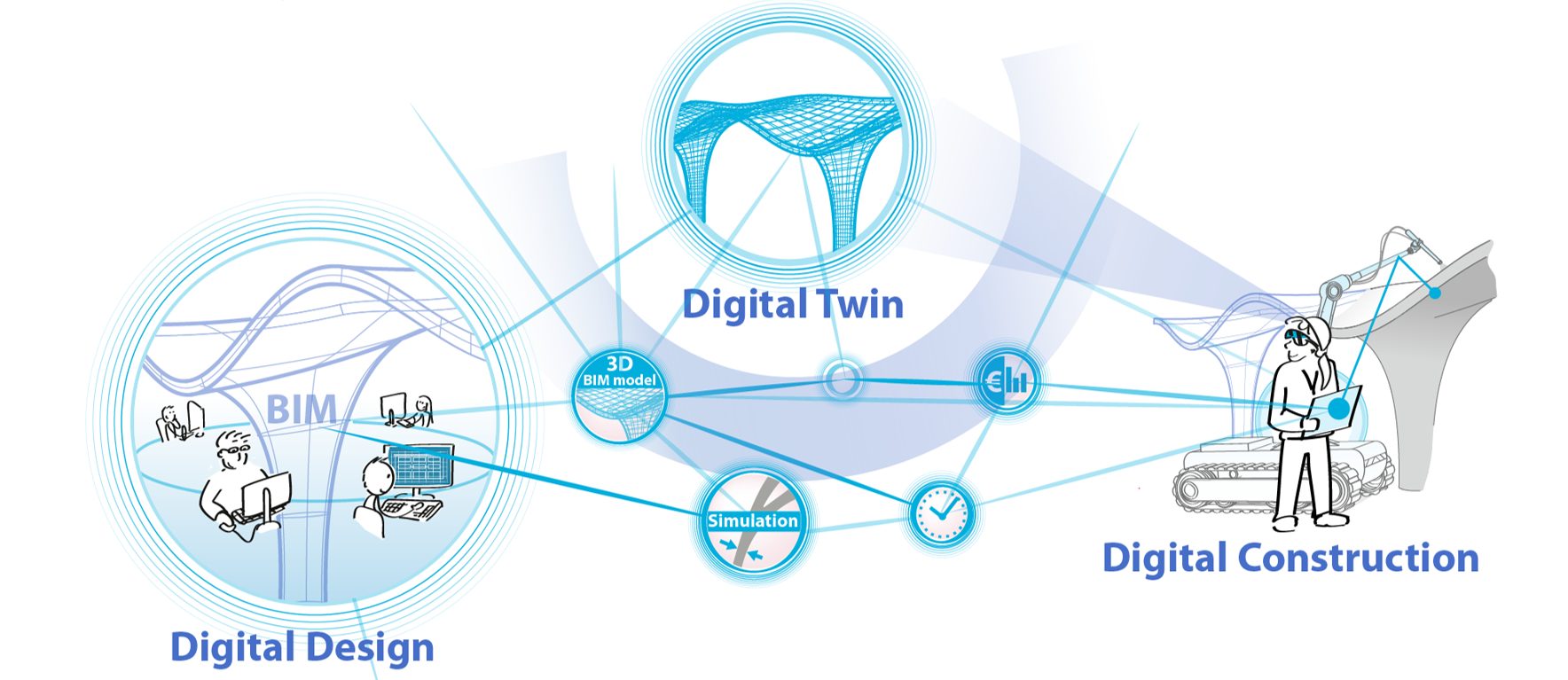
Idealerweise entsteht eine digitale Prozesskette, die so den Automatisierungsgrad erhöht. Bildnachweis: Harald Kloft/TU Braunschweig
Sehen Sie zukünftig auch Drohnen auf den Baustellen?
Prof. Markus Gerke: Wir forschen seit langer Zeit an Methoden zur effizienten und genauen Erfassung der Geometrie von Bauwerken und -teilen mit Hilfe von Flugrobotern, die entweder Kameras oder Laserscanner tragen. Da alle Planungsdaten und Baudetails digital vorliegen, ist der Einsatz von autonomen Flugsystemen auch für die „Digitale Baustelle“ angedacht. Aus dem Grund haben wir eine leistungsfähige Drohne angeschafft und werden deren Einsatz untersuchen. Hier ist die Kombination mit terrestrischer Sensorik interessant, denn wir erhalten einen Überblick über die gesamte Baustelle aus allen Perspektiven.
Was könnte eines der ersten Forschungsprojekte auf der „Digitalen Baustelle“ sein?
Prof. Norman Hack: Im Rahmen unseres Sonderforschungsbereichs TRR 277 „Additive Manufacturing in Construction“ (AMC) erforschen wir gemeinsam mit der TU München bereits seit vier Jahren wichtige Grundlagen für den großformatigen 3D-Druck. Bisher wurden die Versuche zumeist unter Laborbedingungen durchgeführt. Nun ist es an der Zeit, den Schritt aus den Laboren in die Realität der Baustelle zu wagen. Dieser Schritt wird völlig neue Forschungsfragen aufwerfen, die wir – neben wichtigen Fragestellungen zur Nachhaltigkeit – in einigen Teilprojekten der zweiten Phase des Sonderforschungsbereichs vertieft untersuchen werden.
Darüber hinaus arbeiten wir im Horizon Europe Projekt „Next Level AM“ mit unseren europäischen Forschungspartnern, der Mesh AG aus der Schweiz, Rupp Gebäudedruck aus Deutschland und COBOD aus Dänemark, zusammen. Hier wollen wir den Spritzbeton-3D-Druck mit automatisierter Bewehrungsproduktion auf die Baustelle bringen, um mehrstöckige Gebäude herzustellen.
Das Projekt soll auch anwendungsorientiert sein. Wird die Bauwirtschaft mit einbezogen?
Prof. Patrick Schwerdtner: Unbedingt. Wir laden die regionale, aber auch die überregionale Bauwirtschaft ein, bei unseren Forschungsprojekten mitzuwirken – sei es als Partner zur Diskussion von Fachfragen und Anwendungsgebieten zur Weiterentwicklung oder für Dialogformate zur Vorstellung von Visionen einer zukunftsorientierten Bauproduktion. Denn für die Unternehmensstrategie wird es wichtig, rechtzeitig einen Transformationsprozess in Richtung Digitalisierung in Gang zu setzen. Von unserer Seite gibt es ein klares Angebot an die Industrie, sich in das Projekt einzubringen. Wir stellen uns hier in situ auch den Problemen, die es im Labor vielleicht nicht gegeben hätte.
Die Frage zum Abschluss: Wann könnte die „Digitale Baustelle“ Realität werden?
Prof. Harald Kloft: Wir können sofort loslegen. Man darf sich die „Digitale Baustelle“ nicht als ein Endprodukt vorstellen, das erst in fünf bis zehn Jahren zur Verfügung steht. Wir forschen auf der „Digitalen Baustelle“ zwar von Beginn an mit Hightech-Ausstattung, aber unser Ansatz für den Transfer in die Baupraxis ist, dass wir uns sukzessive in die bestehenden Baustelleninfrastrukturen integrieren. Zum Beispiel könnten handwerkliche Prozesse schon jetzt mit Augmented Reality unterstützt werden. Oder 3D-Drucken könnte viel flexibler mit dem schalungsbasierten Betonbau kombiniert werden.
Wir haben zum Beispiel eine Bautechnik entwickelt, bei dem wir die Decken viel dünner als heute betonieren und zur Verstärkung Rippen aufdrucken. Das reduziert die Betonmasse um fast 60 Prozent. Aber, wie Herr Professor Schwerdtner zuvor schon sagte, brauchen wir hier auch den Innovationswillen der Bauindustrie. Nur gemeinsam können wir eine angemessene Wahrnehmung der Bauwirtschaft in Politik und Gesellschaft erreichen, als einer der Zukunftsbereiche, wo Investitionen wichtig sind. Bauen deckt die Grundbedürfnisse des menschlichen Zusammenlebens ab, zum Beispiel den Bedarf an Wohnraum. Eine ökonomisch und ökologisch verträgliche Sicherstellung der Grundbedürfnisse im Hoch- und Infrastrukturbau wird nur mit neuen Technologien möglich sein.