Pores against Turbulence Save fuel with newly designed wing surfaces
Researchers of the SE²A Cluster of Excellence develop new ideas for sustainable and energy-efficient aviation. In various projects, the aircraft of the future is analyzed and optimized in almost every detail. For example, the two young scientists Siby Jose and Hendrik Traub are working on improved wings. Using additive manufacturing, they want to produce wings with better flow characteristics to reduce turbulence and thus save fuel.
The wings of a conventional aircraft have some aerodynamic disadvantages. At the leading edge of the wing the airflow is characterized by a so-called laminar flow: While here the air flows around the shape of the wing smoothly and without eddies, shortly afterwards this flow state changes: the flow starts to perform more chaotic movements, due to wall friction a laminar flow becomes a turbulent flow. The change of the flow state increases the friction drag, which in turn leads to higher fuel consumption.
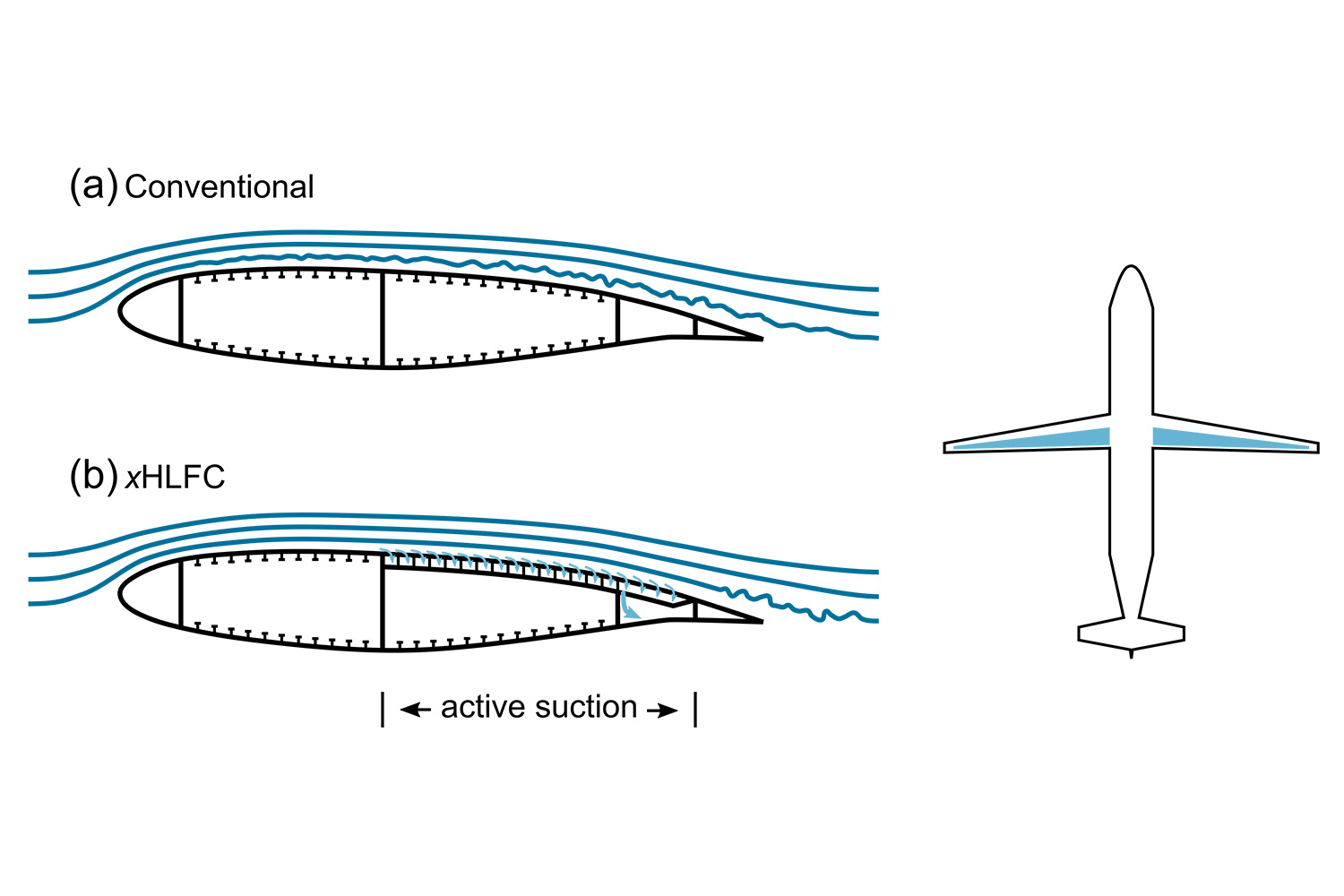
(a) Airflow of a conventional aircraft showing chaotic movements along the aerofoil. Approach of the cluster of excellence: aerofoil with laminar flow and an active suction system for a delayed transition (b). Credits: Hendrik Straub/TU Braunschweig
Therefore, one goal of the Cluster of Excellence SE²A is to maintain the laminar flow and delay the transition to chaotic movements. One idea is to realize a kind of air suction at the rear part of the wing where the flow would otherwise turn turbulent. For this purpose a pore surface is placed on the wing structure to stabilize the flow by suction and to maintain the laminar flow condition.
3D printing of complex structures
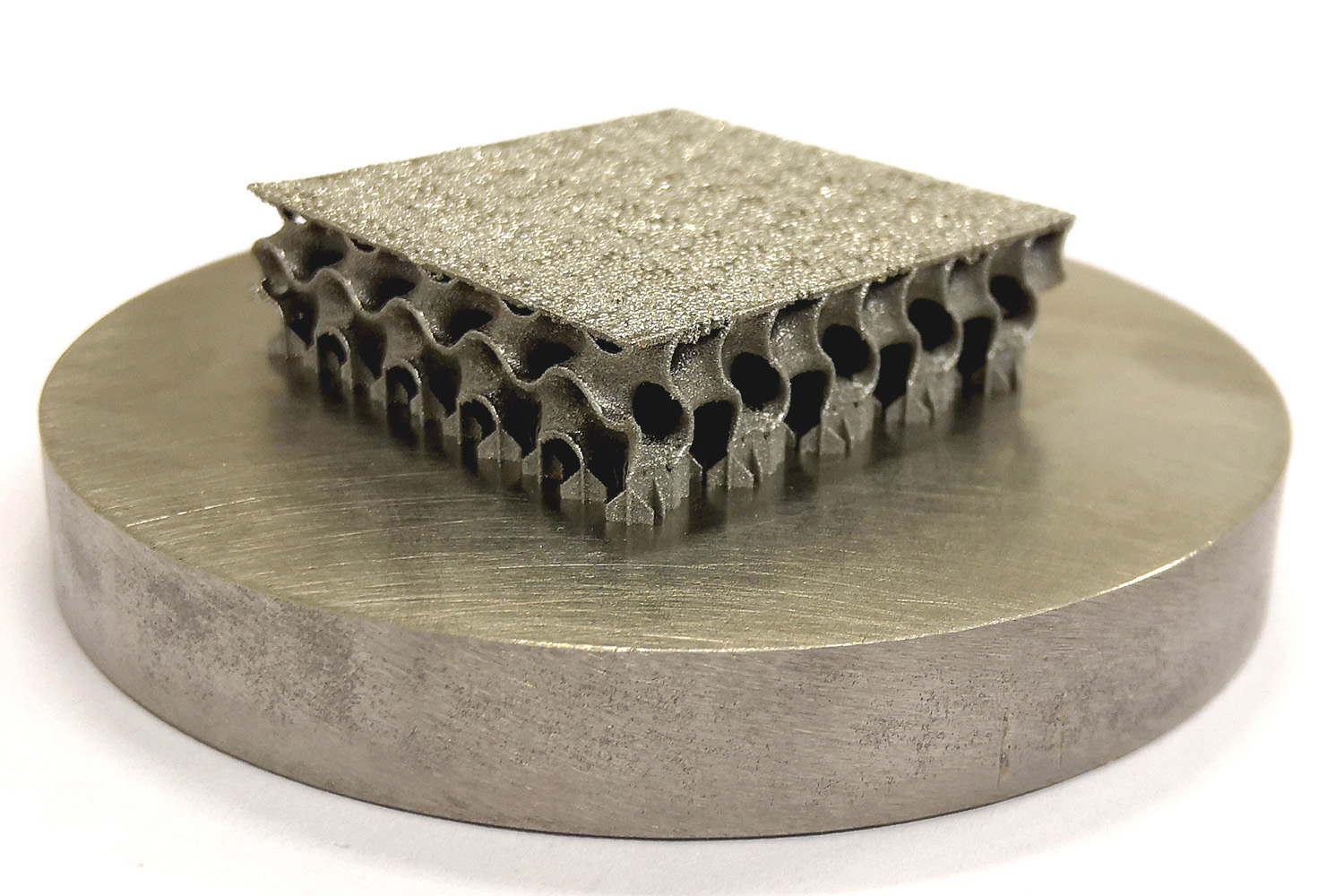
Titanium part, printed with SLM technology. Visible is the skin structure, providing submillimetre sized holes for pressure distribution as well as the TPMS substructure, supporting the skin of the wing. Credits: Siby Jose/TU Braunschweig
However, the production of such a wing structure is not very easy. The two young researchers Siby Jose and Hendrik Traub are tackling the challenges in the production of the optimized wing.
To model the specific pressure distribution for the suction system, they propose complex internal structures of the wing. Since traditional manufacturing techniques are limited in the execution of these structures, they choose 3D printing as manufacturing method.
Different additive manufacturing methods
They work mainly in metal printing with Selective Laser Melting (SLM) technology and in plastics printing with Stereolithography (SLA) and Fused Deposition Modeling (FDM) technology. In selective laser melting, the material is applied in thin powder layers onto a base plate and melted with laser radiation. Stereolithography is also a laser-based technology. The material used is a UV-sensitive liquid resin. During the printing process, a UV laser beam selectively hardens the resin layer by layer, depending on the cross-section of the object. In the fusion layering (FDM) process, an object is produced layer by layer from a meltable thermoplastic.
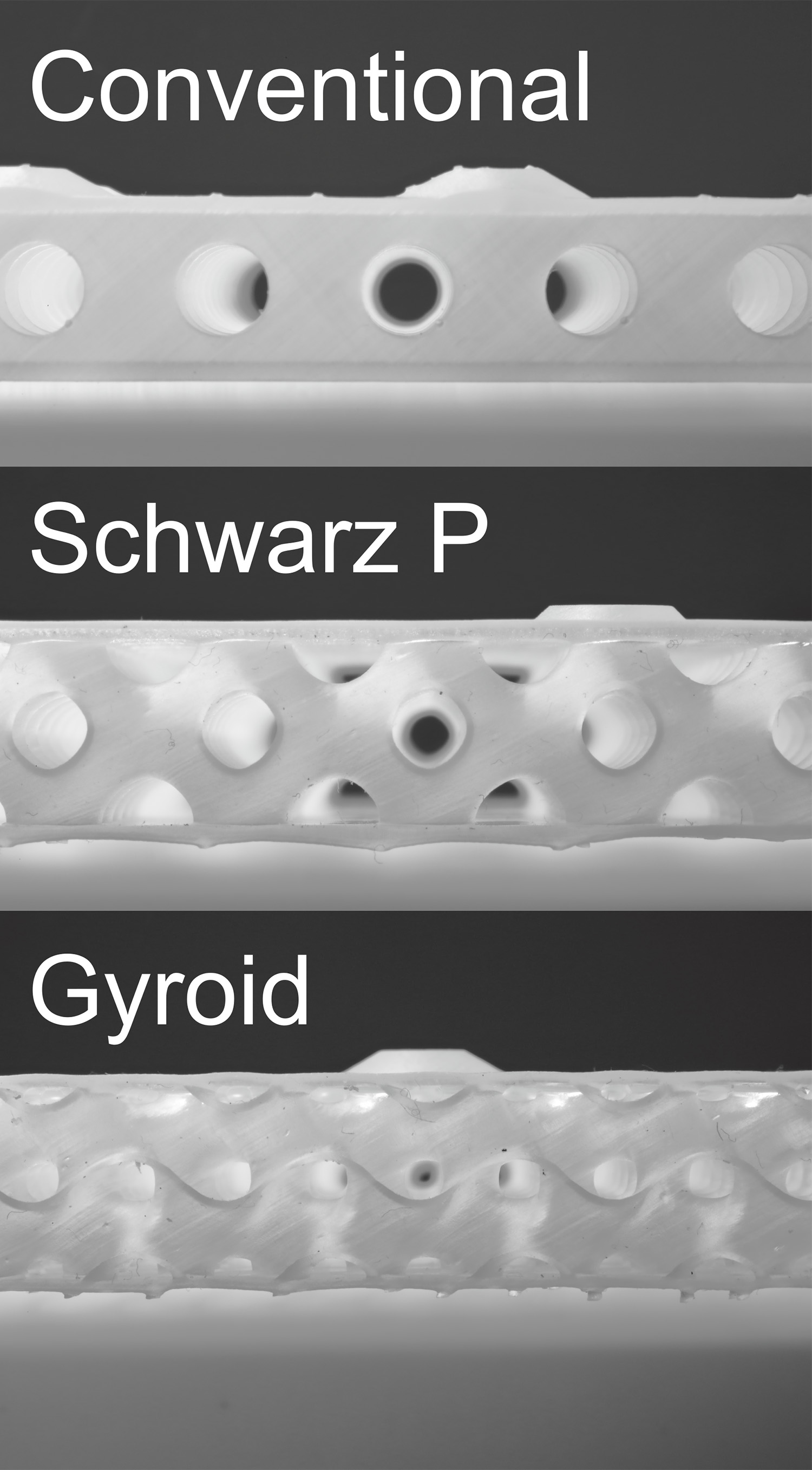
Conventional and TPMS designs (Schwarz P and Gyroid), printed with SLA for structures inside the wing, providing structural and aerodynamic properties. Credits: Hendrik Traub/TU Braunschweig
Jose and Traub have compared the three processes with regard to the aerodynamic properties of their printed structures. They are also currently working on optimizing the sub-millimeter-sized holes in the skin that provide the specific pressure distribution for air intake. For this purpose, process parameters such as laser spot size and laser speed must be varied to enable the complex manufacturing process. For the internal structure, comparisons of different designs are carried out to obtain the most suitable structure with good structural and aerodynamic properties.
“We are also currently investigating properties of Triply Periodic Minimal Surfaces (TPMS) as sandwich core structures in lightweight construction and the possibility of using them as air ducts in wing construction,” says Traub. TPMS structures could be used as a three-dimensional support structure and also enable the transport of media such as air inside the component – in comparison to conventional honeycomb structures, for example.
“After optimizing the suction system in terms of aerodynamic and structural properties, we test the entire design in the wind tunnel to get more ideas for optimization,” says Jose.
Text: Siby Jose, Hendrik Traub