Sustainable flying: Is the fuel cell the solution? An interview with Patrick Meyer on the future of flying with the PEM fuel cell
Whether battery-powered aircraft, biokerosene or hydrogen: science is working on a variety of technologies to make the dream of sustainable flying a reality. For medium-haul flights, PEM fuel cell aircraft could be the answer. One challenge, however, is air traffic management. The SE²A Cluster of Excellence project “C6.3 – DEFCA: Design-space evaluation of the air, heat and power management of fuel cells for aviation” is looking into this. In this interview, PhD student Patrick Meyer talks about optimising air management and the aircraft design of the future, and answers the question of when the dream of environmentally friendly flying with fuel cells could become a reality.
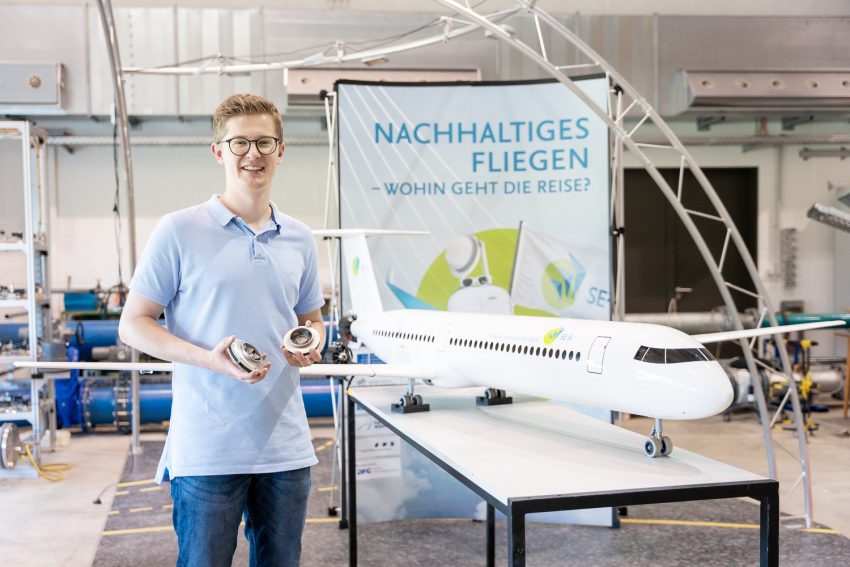
PhD student Patrick Meyer conducts research for SE²A at the Institute of Aircraft Propulsion and Turbomachinery. Photo credits: Marius Lauer/TU Braunschweig.
Why does a fuel cell aircraft need an air management system?
A PEM (polymer electrolyte membrane) fuel cell converts the chemical energy contained in hydrogen and oxygen into electrical energy. During flight, the hydrogen required is stored in a tank carried on board the aircraft. Oxygen from the ambient air is used to save weight. However, the fuel cell makes certain demands on the air in order to function reliably. It needs a certain pressure and humidity, and the air must not be too hot or too cold. The better the supplied air meets these requirements, the higher the efficiency of the fuel cell. It is therefore necessary to prepare the air in the best possible way using an air management system. Pressure is provided by an electric motor-driven compressor, temperature by a heat exchanger and humidity by a humidifier.
Such an air management system is generally required for PEM fuel cells. In aeronautics, however, the air management system is even more important because both the performance requirements and the environmental conditions change during flight. For example, temperatures and air pressure are much higher during take-off than at high altitude. The heat exchanger is therefore particularly important during take-off, when heat dissipation is more difficult due to the high ambient temperature. The compressor, on the other hand, has to work harder at high altitude to compensate for the lower air density. Power requirements also vary according to the phase of flight. During take-off, the aircraft requires considerably more power or thrust than when cruising.
Why is it necessary to optimise the air management system?
The air management system has a direct influence on the weight of the aircraft and therefore plays a role in determining whether flying with a fuel cell on medium-haul routes is feasible in principle. The air management system also has a direct impact on hydrogen consumption. Simply reducing the parasitic power, i.e. the additional power required by the air management system, reduces consumption and waste heat. In general, the better the operating parameters of the fuel cell are set, the higher the efficiency of the fuel cell. Other important issues are water management and the influence of air management on the formation of condensation trails.
What are you focusing on?
Some of our project partners are focusing on individual components and trying to optimise them. We start at a higher level and look at the whole system. To do this, we analyse different architectures or models, either from the literature or from project partners, for example different humidification strategies, combine the whole thing as an overall system view and compare which works best for the whole system. With our calculations, we can then provide our partners with important boundary conditions that help them to further improve the individual components.
Why is the fuel cell particularly interesting as a propulsion system for medium-haul flights, i.e. flights within a continent or between neighbouring countries?
Different types of propulsion are best suited to different distances. For example, fuel cell aircraft could also be used for short-haul flights. Theoretically, it would also be possible for smaller aircraft to fly on battery power alone. This would be completely emission-free, apart from noise pollution. For long-haul flights, however, propulsion systems such as hydrogen combustion or the combustion of Sustainable Aviation Fuels (SAFs) are more realistic, as fuel cell aircraft would be too heavy for these distances and there would also be problems with waste heat. For medium-haul flights, however, the fuel cell could be the solution. Due to the higher energy density of the propulsion system, it offers weight advantages over the battery, as well as greater emission reduction potential and higher efficiency than burning fuels.
Can you predict when climate-neutral flying with fuel cells could be possible for the masses?
That’s a good question. In principle, it is already possible to fly with a fuel cell aircraft. One company recently demonstrated this by flying a prototype short-haul aircraft with a fuel cell. We don’t yet know for sure whether it will work on medium-haul routes. And there are many other aspects that will play a role in making flying possible for the masses. For example, a nationwide hydrogen infrastructure has yet to be established. After all, what’s the point of flying a hydrogen-powered aircraft if there’s nowhere to refuel it?
That’s why my colleagues in project A3.3 of the SE²A Cluster of Excellence are working on retrofitting existing airports. Aircraft also have to meet many stringent certification requirements to be approved for public transport. This is a lengthy process, especially for such a new technology. And then there are some question marks over the production of hydrogen. If I want to fly climate-neutrally, the energy used to produce the hydrogen must come from renewable sources. There is still a long way to go before all these structures are in place.
Will flying with fuel cells also change aircraft design?
Yes, definitely. The first fuel cell aircraft will probably be “retrofits”. This means taking an existing aircraft design and installing a new engine, so to speak. While this works quite well with sustainable aviation fuels, it is not so easy with fuel cells. This is because paraffin is typically stored in the wings, while hydrogen would probably have to be stored in liquid form in large cylindrical cryogenic tanks. This means that these would probably have to be located in the fuselage rather than in the wings, which would have a major impact on the design. In addition, due to its density, hydrogen requires a much larger storage volume than paraffin. The air management and thermal management systems we have analysed also take up space. The layout of the engines could also change. Then there is the waste heat from the fuel cell. To dissipate this, the aircraft will probably need very large air intakes. In order to build a fuel cell aircraft that is as efficient as possible, it makes sense to completely redesign the aircraft in the future.
Other SE²A Cluster of Excellence projects are therefore focusing on optimising the design. We support these projects by providing key data to help the project team design the aircraft of the future. However, it will be a long time before we fly in such a completely redesigned aircraft, and it will be exciting to see how people react to this completely new way of flying.