Picture of the month: 3D printed filigree bridge Material-efficient lightweight structures through "Injection 3D Concrete Printing"
Could this be the bridge of the future? Filigree, light, material-efficient? In the Collaborative Research Centre “Additive Manufacturing in Construction (AMC)” of TU Braunschweig and TU Munich, scientists have produced the first bridge prototype using a special 3D printing process. “Injection 3D Concrete Printing”, developed and patented at TU Braunschweig, enables lightweight structures that were previously impossible with concrete.
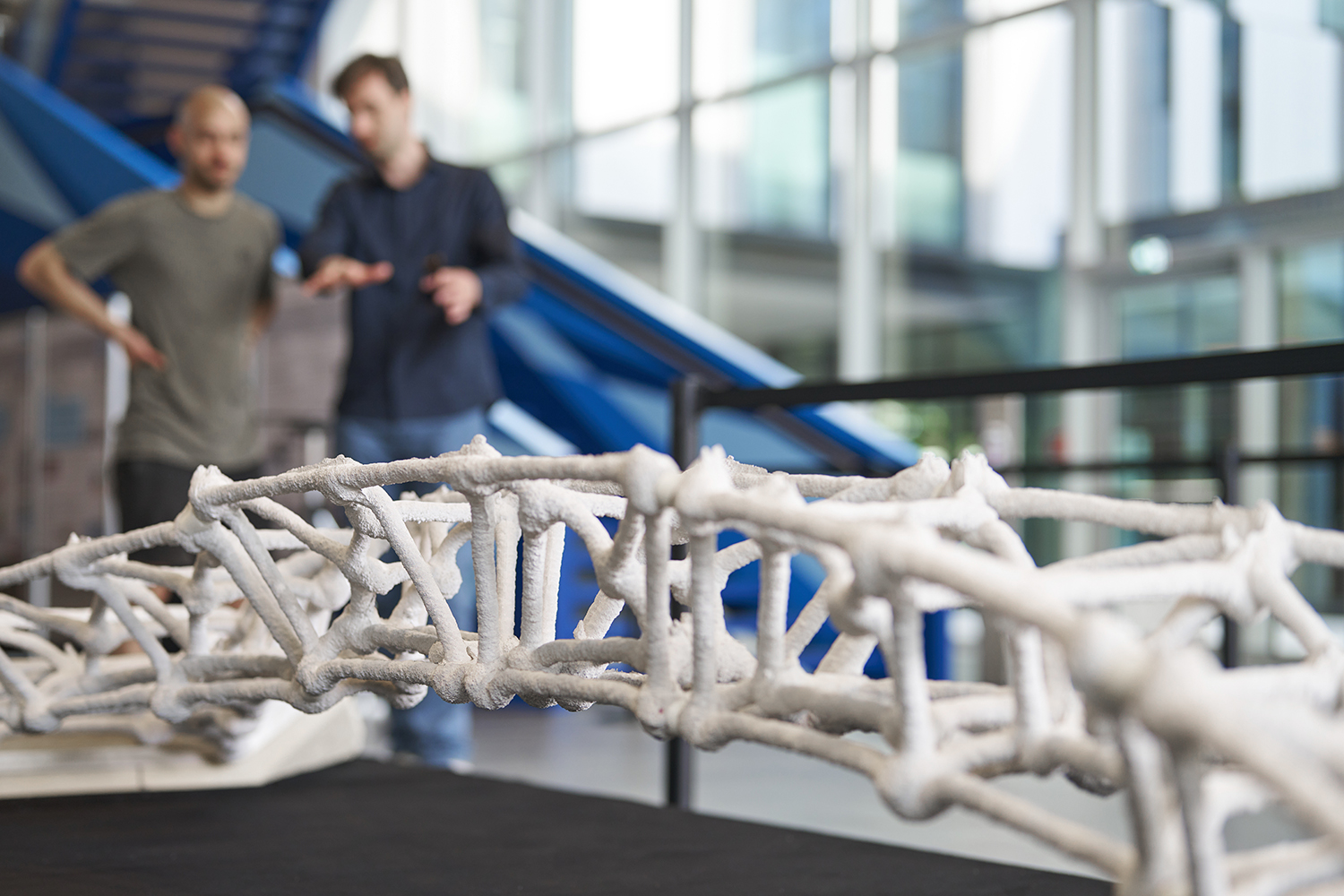
The filigree bridge was created by Injection 3D Concrete Printing. Picture credits: AMC/Julia Bergemeister
Additive manufacturing processes mainly focus on layer-by-layer 3D printing techniques, which are usually applied horizontally. However, these processes are limited for geometrically complex structures. “Injection 3D Concrete Printing”, on the other hand, offers completely new possibilities for form finding and 3D path planning. The component can also be built up three-dimensionally in space. This makes it possible to achieve a lightweight, resolved construction method more familiar from wood or steel.
In this 3D printing process, scientists robotically inject a strand of concrete into a non-hardening carrier fluid. The strand of concrete must remain in a stable position. The carrier fluid must therefore be perfectly matched to the concrete and the robot-controlled process in order to hold the material in the desired position. This support fluid can be removed later, leaving the filigree structure in place.
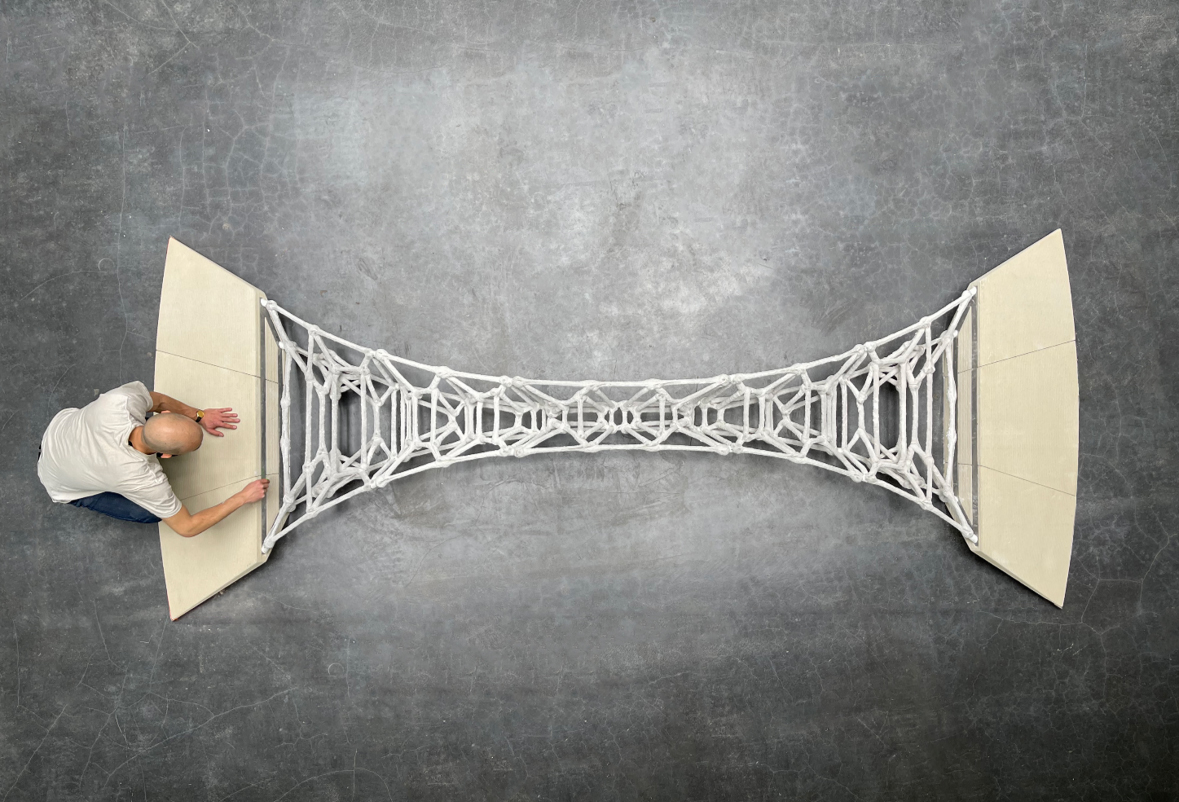
For the prototype of the bridge, five segments were printed, which were then assembled by the scientists. Picture credits: AMC/TU Braunschweig
Bridge exhibited at Architecture Biennale
To accommodate the limited working space of the robot arm, the original bridge had to be divided into five segments. These individual segments were then produced using the I3DCP process. Once the five bridge segments, the joints and the two support feet had been successfully 3D printed, they were assembled. The scientists took great care to ensure that each segment fitted seamlessly into the neighbouring segments to create a unified and robust structure.
The bridge caused a stir at last year’s Architecture Biennale in Venice. The structure was part of the “Time Space Existence” exhibition at the European Cultural Centre (ECC).
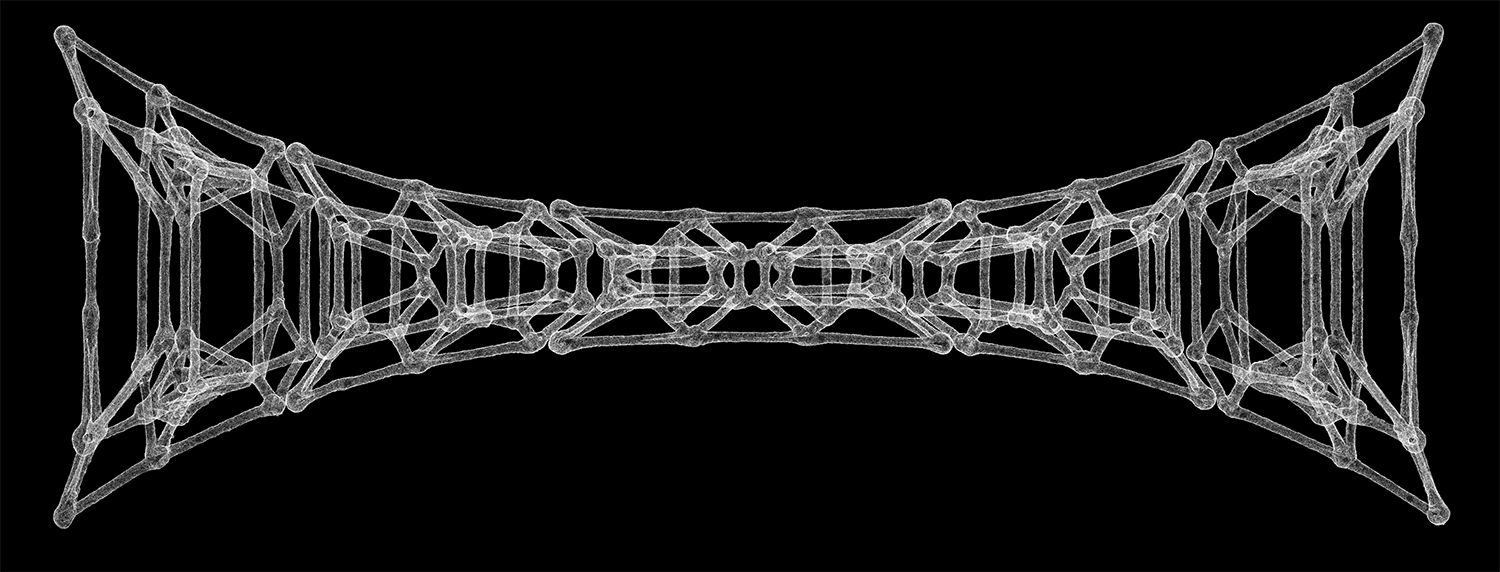
3D scan of the bridge. The bridge’s maximum load-bearing capacity exceeds its own weight by a factor of 20. Picture credits: AMC/TU Braunschweig
The prototype bridge is 4.20 metres long, 50 centimetres high and 1.80 metres wide at its widest point. Its total weight is approximately 312 kilograms. The bridge’s maximum load-bearing capacity exceeds its own weight by a factor of 20, demonstrating the potential of “Injection 3D Concrete Printing” for the construction of lightweight concrete infrastructure. In order to produce larger load-bearing objects, the scientists need to integrate reinforcement and nodes for a stronger structure.
The following researchers are involved in the project: Yinan Xiao, Aileen Vandenber, Osman Zhini, Dr. Patrick Ole Ohlbrock, Prof. Dr. Pierluigi D´Acunto, Prof. Dr. Norman Hack, Prof. Dr. Harald Kloft, Prof. Dr. Dirk Lowke und Prof Dr. Inka Mai.
About the Collaborative Research Centre AMC:
The DFG-funded Collaborative Research Centre TRR 277 “Additive Manufacturing in Construction” (AMC) of TU Braunschweig and TU Munich aims to play a key role in shaping the transformation of the construction industry towards a digital and sustainable future. The focus is on the use of 3D printing technology (additive manufacturing) to develop resource-saving, low-emission and economical construction methods. Complex research questions relating to materials, process engineering, digital process control, modelling, design and construction will be examined holistically by scientists from the fields of Civil Engineering and Mechanical Engineering.
Further information: www.amc-trr277.de