Flying farther on less fuel Focus on Research: Energy Transition in Aviation
With cheaper tickets and 700 new routes, airlines around the world carried a record high of 3.7 billion passengers in 2016. This figure is up 6.3% compared to 2015, according to the International Air Transport Association (IATA). And air transport is poised to increase even further. To help mitigate the environmental impact, the European Commission’s Flightpath 2050 has set ambitious goals for the industry: by the year 2050, fuel consumption and carbon dioxide emissions are to be reduced by 75% per passenger kilometre, as compared to 2000. Nitrogen oxide emissions are to decrease by 90%, and noise emissions by 65%.
Less weight, less resistance
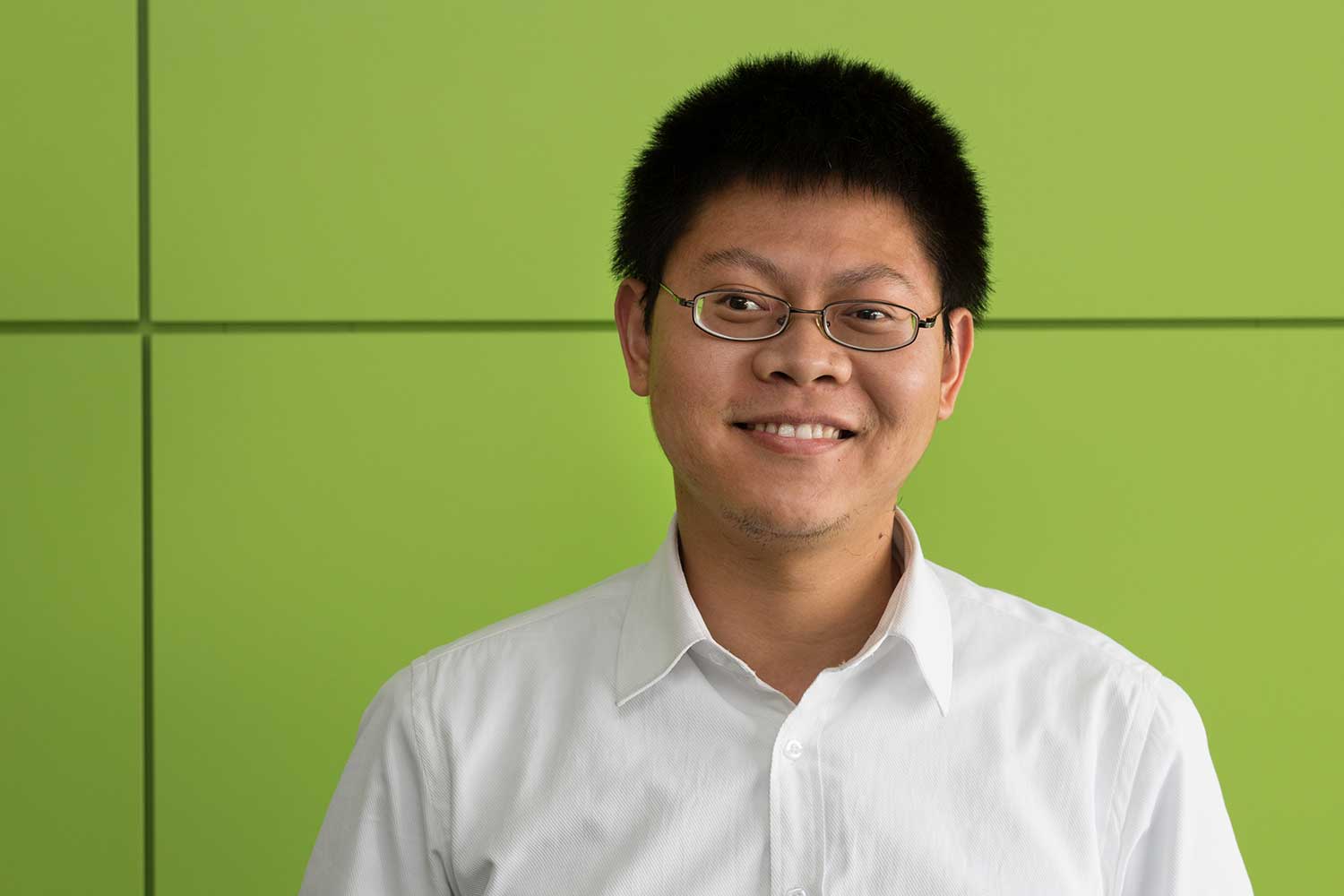
Dr. Yaolong Liu, Institute of Aircraft Design and Lightweight Structures. Credit: Jonas Vogel/TU Braunschweig
“Fuel consumption can be lowered by reducing – reducing weight with the help of lighter materials and construction methods, or reducing the drag on the fuselage and wings through improved aerodynamics”, says Dr. Yaolong Liu, who is conducting research on overall aircraft design at TU Braunschweig’s Institute of Aircraft Design and Lightweight Structures. He also participates in the Energy System Transformation in Aviation research project, namely as a member of the System Platforms working group, which concentrates on technical changes to aircraft.
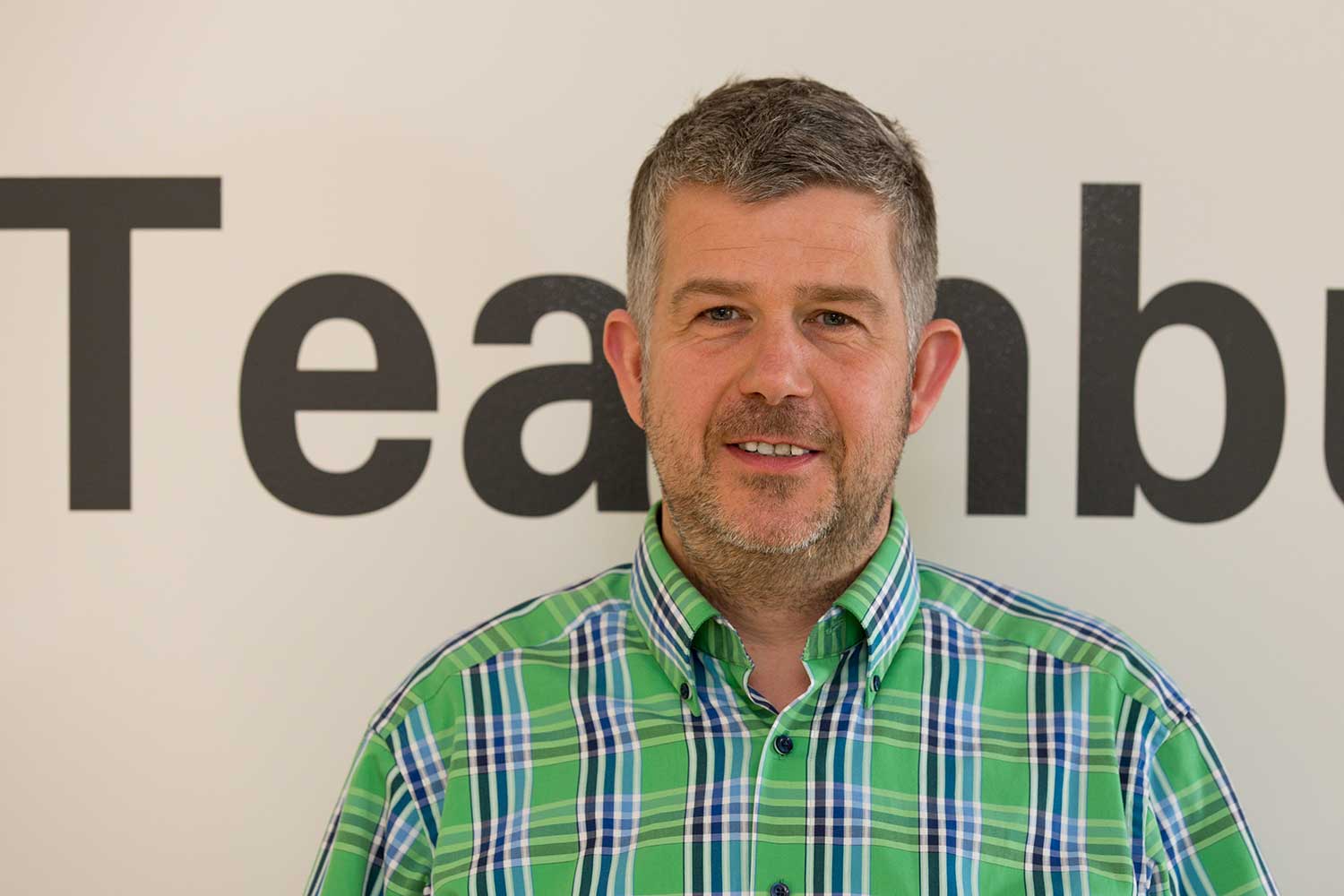
Nils Beck, Research Assistant at the Institute of Fluid Mechanics. Credit: Jonas Vogel/TU Braunschweig
Less resistance is one of the avenues the scientists are pursuing, and this puts the focus on laminar flow technologies. “Less than five percent of the surface of a passenger aircraft currently has properties that encourage laminar air flow. There is still a lot of potential here, despite the fact that research into boundary layers has been underway for more than 50 years, and experiments with wind tunnels and research aircraft have produced promising results”, says team member Nils Beck, Research Associate at TU Braunschweig‘s Institute for Fluid Mechanics.
Optimising surfaces
A flow is laminar when it is homogeneous, or layered, as opposed to a turbulent flow, whose swirls and eddies cause surface friction and energy loss. The more evenly air flows around an aircraft‘s wings and fuselage, the less resistance there is. Lower air resistance in turn means lower fuel consumption and exhaust emissions. As Beck puts it, “You get a laminar flow by optimising shapes and surfaces. Or – and this is our approach – by developing and mounting an active system that sucks away part of the flow, limiting aerodynamic instabilities and preventing laminar flows from becoming turbulent ones.” This Laminar Flow Control technology could save more than 30% in fuel.
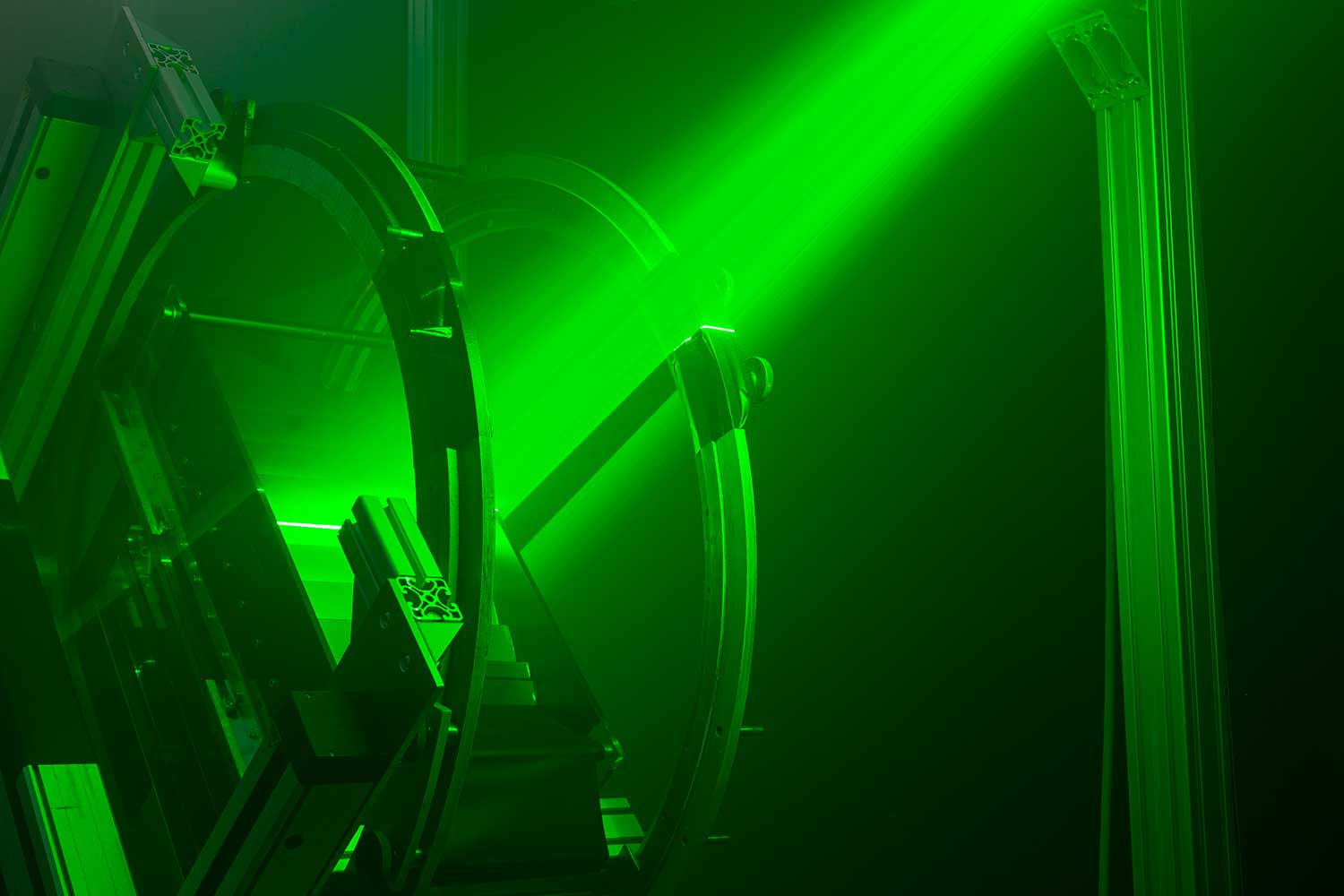
“Particle Image Velocimetry” can be used for non-contact laser measurement of different types of airflow around aircraft. Credit: Sebastian Olschewski/TU Braunschweig
“Until now, periods of high fuel prices have usually been followed by severe slumps in oil prices. Because of this, manufacturers lack the long-term motivation to bring laminar flow technologies to product maturity”, explains Beck. “But we are not going to wait for the price of oil to rise again; we are pursuing this topic now.” Because today’s developments will be the components of tomorrow’s aircraft. “In aviation, innovation cycles are much longer than in other sectors. Technologies are highly complex due to high safety requirements.”
Text: Nicole Geffert