3D printing in steel construction: serial becomes individual German Steel Construction Award goes to Linus Schmitz
How can steel beams that are exposed to particular stresses be individually reinforced? Linus Schmitz investigated this in a student research project at the Institute of Structural Design (ITE) at TU Braunschweig: using a 3D printing process, he applied metal specifically to the areas of steel profiles where the stresses are greatest. This allows for slimmer profiles, saving resources and reducing CO2 emissions in steel construction. The Civil Engineering graduate has now been honoured for his research with the German Steel Construction Award. The award is presented every two years by bauforumstahl.
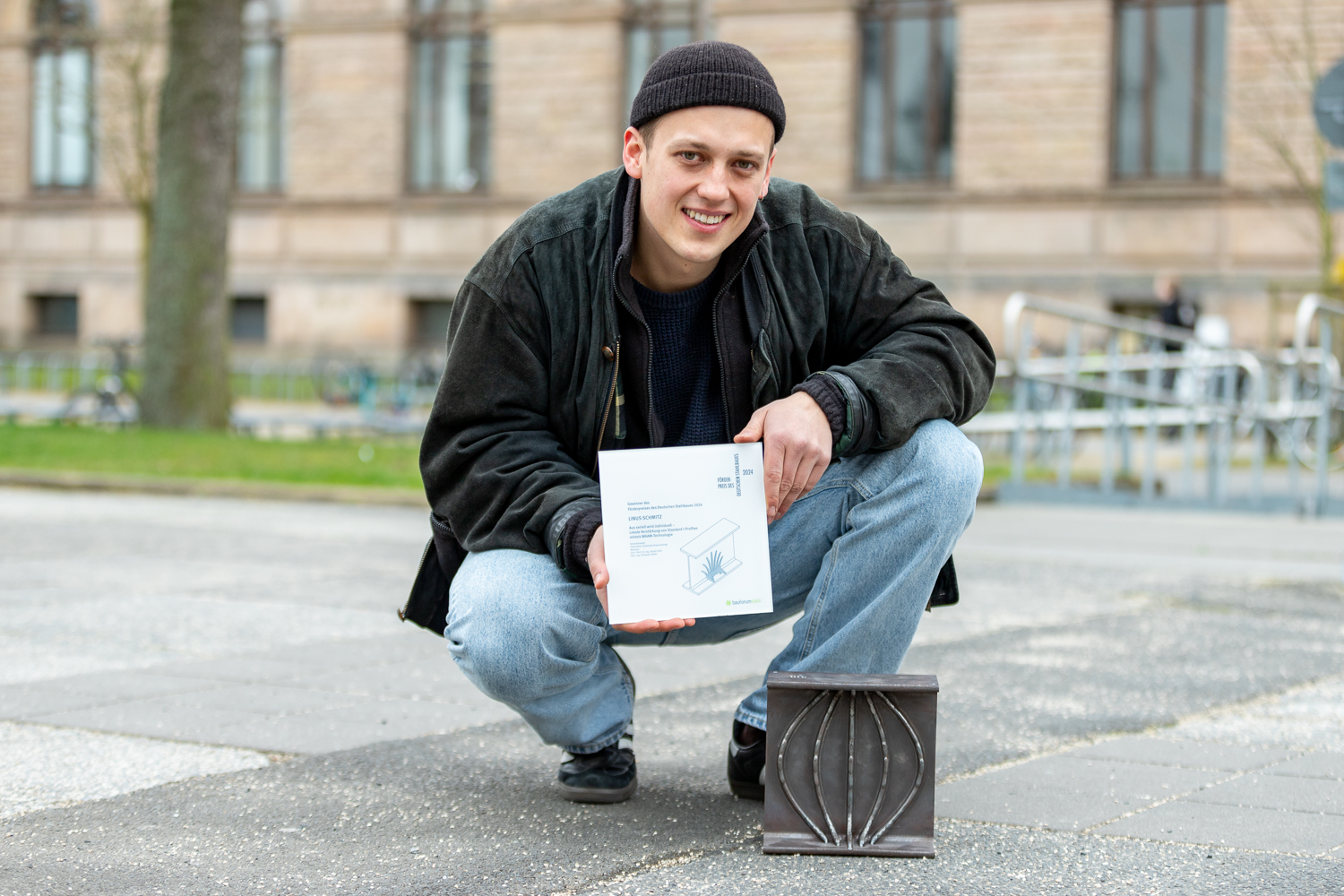
Linus Schmitz with the German Steel Construction Award and one of the five demonstrators. Photo credit: Kristina Rottig/TU Braunschweig
“Wire-and-Arc Additive Manufacturing” (WAAM) is the name of the 3D printing process that Linus Schmitz used in his specialisation project. The welding process uses an electric arc as a heat source to melt a metal wire. In the construction industry, this technology can be used to produce steel nodes, for example, but also geometrically complex components and even pedestrian bridges.
Serial uniqueness
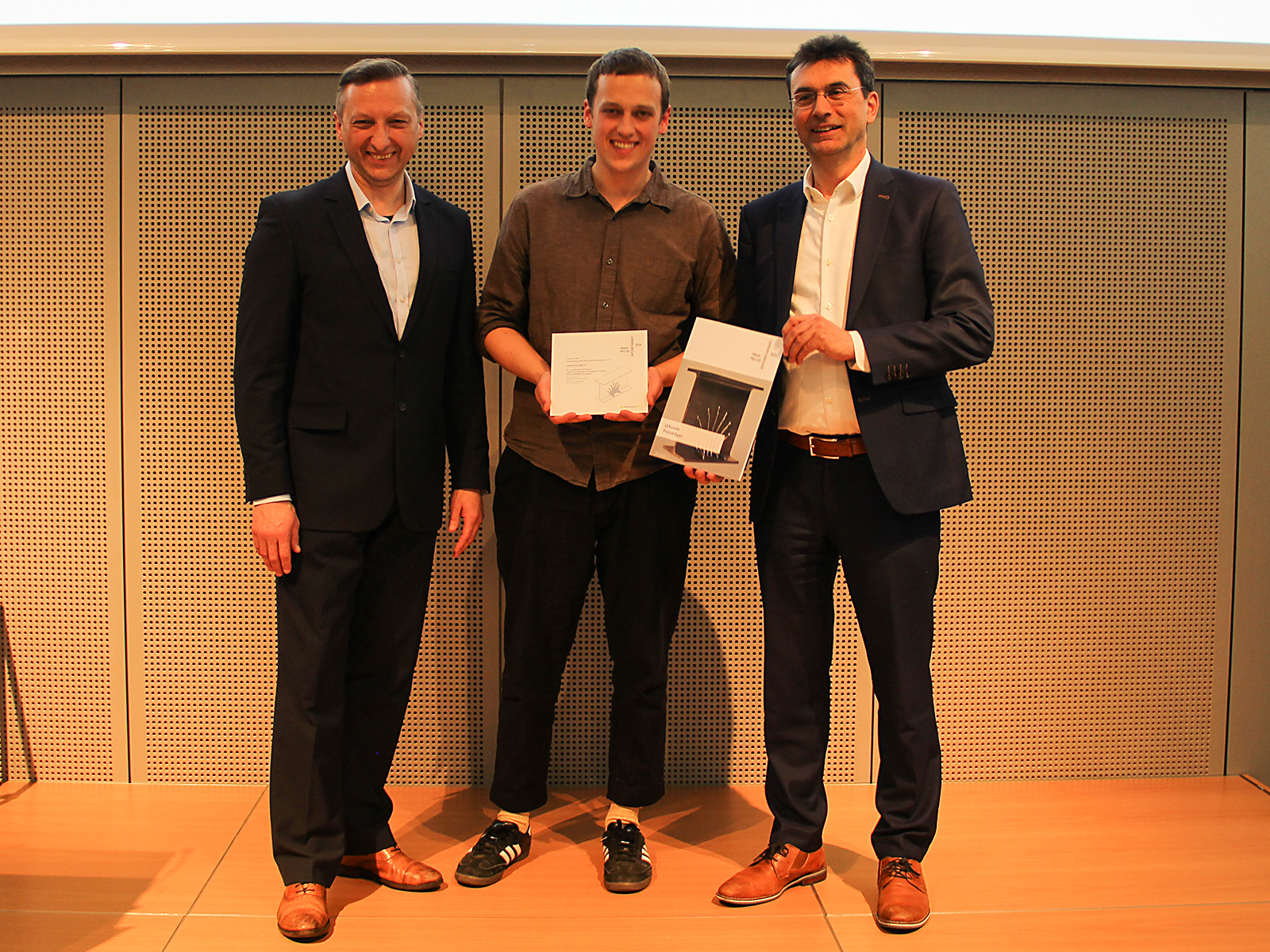
Presentation of the German Steel Construction Award at the DASt Colloquium in Munich. Photo credit: bauforumstahl e.V.
By applying layers of molten metal in points or lines, the WAAM process allows a component to be built up freely in stages. “This makes it possible to produce complex, free-form elements,” explains Linus Schmitz. Unlike mass-produced components such as rolled profiles, which can be efficiently manufactured industrially but have a standardised geometry and are therefore only used in high-stress areas, 3D-printed components can be much better adapted to local loads.
The combination of serial production of rolled profiles and local reinforcement using WAAM thus combines the advantages of both manufacturing techniques. The content of the thesis originates from the research programme of project A07 of the Collaborative Research Centre TRR 277 Additive Manufacturing in Construction (AMC) of TU Braunschweig and TU Munich and was conceived by Professor Harald Kloft and Christoph Müller. For Linus Schmitz, the project offered a special opportunity to research cutting-edge technologies during his studies and to gain insights into the interdisciplinary cooperation of a Collaborative Research Centre.
Combining the strengths of two processes
He produced five demonstrators at the ITE using the robotic WAAM system. He first carried out a series of tests to achieve a stable manufacturing process with the robot system and welding parameters, and to produce the thinnest possible reinforcement structures. “I took it step by step,” says the civil engineer. “It was a very experimental and free process.“
- Bildnachweis: Linus Schmitz/TU Braunschweig
- Bildnachweis: Linus Schmitz/TU Braunschweig
- Bildnachweis: Linus Schmitz/TU Braunschweig
In his work, Linus Schmitz systematically investigates the individual reinforcement of rolled profiles for different types of stress: instead of dimensioning a profile for the maximum stress in future steel construction planning, a profile with smaller dimensions can be selected. The areas of maximum stress can then be locally reinforced with additional material using the WAAM process. Professor Kloft also sees great potential in the strengthening and retrofitting of existing steel structures. This could make an important contribution to circular construction in building practice. In the second funding period of TRR 277 AMC, which is currently underway, this will be investigated using mobile robots.
“Congenial collaboration between engineer and architect”
“This possibility of ‘personifying’ standardised profile rows with material reinforcements in layers according to the main stress lines of the moment curves offers new possibilities for detail design, especially for the designer or constructor interested in design quality, but also in material efficiency,” said the jury of the German Steel Construction Award. “In principle, a reduced use of materials goes hand in hand with the gracefulness of the filigree structure and the legibility of the flow of forces in the joints. One is reminded of the congenial collaboration between engineer and architect, for example in the formation of the struts of the steel girders for the canopies of the Palazzo del Lavoro, Turin, 1961, by Pier Luigi Nervi and Gio Ponte. […] In the age of resource-conscious construction, the imperative of material economy is also a highly welcome strategy of sustainability, in which ecology, economy, engineering and design complement each other in a happy way.”
Innovations for sustainable construction
Linus Schmitz is committed to using innovation to make construction more environmentally friendly. “The fact that I was able to make a serious contribution to research with my work here naturally makes me very happy,” says the civil engineer. The results of the work have been published in a journal paper. Together with Neira Babovic from ITE, Linus Schmitz presented them at Eurosteel 2023 in Amsterdam.
After working intensively on the project, it was clear to him that he wanted to pursue a career in research. “I want to investigate the interface between Civil Engineering and Architecture and close the gap between design, materials and manufacturing processes,” says the TU graduate. In the near future, however, his research will focus not on metals but on earth-based building materials, which he is investigating in a project at ETH Zurich.