Lightweight concrete bridges from the 3D printer New process aims to save materials and enable complex geometries
It is the most commonly used material in the world: concrete. The material made of cement, water and aggregates is cheap, available in large quantities, easy to process and durable. However, the enormous demand for the building material results in a crucial problem: the production of cement is responsible for around eight percent of global carbon dioxide emissions. In order to reduce this, scientists at Technische Universität Braunschweig are researching how the immense material consumption in construction can be reduced. In a project funded by the Volkswagen Foundation, they are pushing the limits of 3D printing and using a new technique to create extremely lightweight structures from concrete.
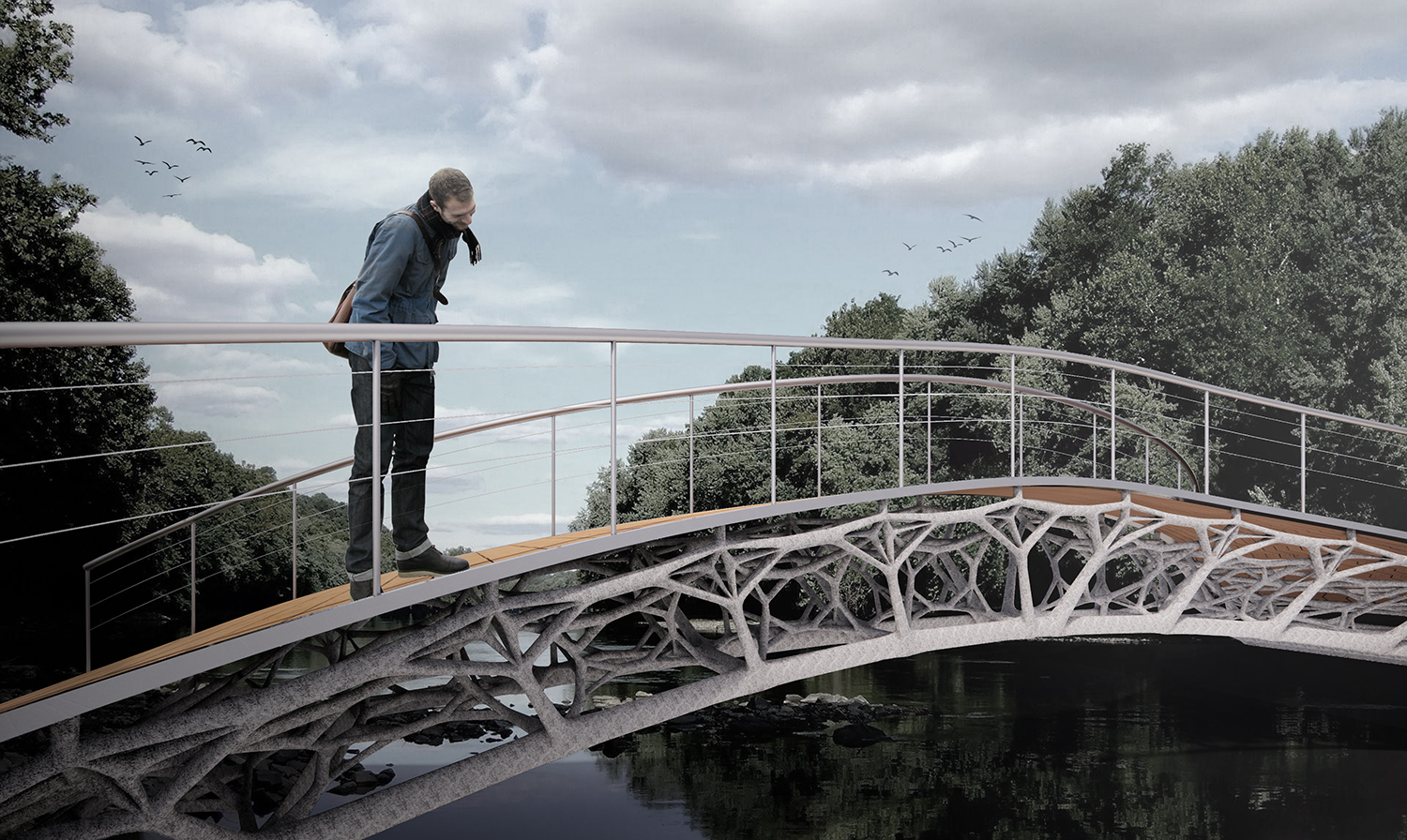
Is this what bridges will look like in the future? Picture credits: ITE/Braunschweig (Noor Khaled, Yinan Xiao), in cooperation with Pierluigi D’Acunto and Ole Ohlbrock.
According to the International Energy Agency (IEA), the construction and building sector is responsible for around 40 percent of global greenhouse gas emissions. Concrete production alone causes more carbon dioxide emissions than all transport – i.e. aviation, shipping and cars – combined. Given this significant environmental impact from construction, solutions to reduce material requirements, energy consumption and waste volumes are urgently sought.
Scientists at TU Braunschweig see enormous potential in additive manufacturing, also known as 3D printing. With the help of digital processes, material can be used more efficiently and significantly less of it can be consumed. Concrete is only deposited in the component where it is actually needed. 50 to 70 percent of material can be saved in this way. The Institute for Building Materials, Concrete Construction and Fire Safety (iBMB) and the Institute of Structural Design (ITE) are going one step further. Until now, it has been customary to print horizontally, layer by layer, in order to build a house wall, for example. The two institutes, on the other hand, are researching a completely new process.
Filigree structures made of concrete
In the project “Beyond 3D Printing – A novel spatial printing technology for lightweight spaceframe concrete structures”, the researchers led by Professor Dirk Lowke, Professor Harald Kloft and Professor Norman Hack are now developing a 3D injection printing process (Injection 3D Concrete Printing) to produce lightweight spatial structures. “In concrete construction in particular, it is common to have solid concrete walls. However, we want to achieve a lightweight, resolved construction method that is more familiar from wood or steel,” explains Professor Lowke.
In this process, the scientists inject a concrete strand into a carrier medium, where it forms a filigree spatial structure. “In the experiment, the carrier fluid is a transparent gel. For the large-scale application process, we want to replace this with a mineral suspension that is cheaper, ecologically harmless and recyclable on a large scale,” explains Professor Lowke. The difficulty with this process: The carrier fluid must be perfectly matched to the concrete and the robotically controlled process to keep the material in the desired position.
Bridges and roof structures from the 3D printer
When the rock flour suspension, which looks like a mud pack, is drained off, the grid-like structure is left behind. But where should this be used? “The concrete components are suitable for bridges or roof support structures, for example,” he says. These are to be manufactured in the factory and assembled on site. “In addition to the CO2 savings potential, we can also create new possibilities in architecture with our process, namely complex geometries without spatial restrictions.” Here, the research team points to bridges designed by Swiss civil engineer Robert Maillart and filigree forms such as those once created by Italian civil engineer Pier Luigi Nervi with his “ferro-cemento” elements. “Such structures are no longer manufactured today because it is too costly. However, if we have a technology that allows us to produce something like this in a cost-effective way, it may help these resource-efficient structures have a new renaissance.”
The project team is also researching reinforcement integration to ensure the structure is as load-bearing as possible. “In injection 3D concrete printing, we want to imprint steel structures or carry a long metal or fiber strand in the concrete strand. That’s the somewhat challenging option. With this, not only concrete comes out of the nozzle, but also a continuous wire rope, an endless fiber that serves as reinforcement,” says Professor Lowke.
With their project, the Braunschweig experts from civil engineering and architecture are looking clearly into the future: Professor Lowke expects at least ten years before the already patented 3D printing technology can be used on a large scale. First, however, the researchers want to prove the feasibility and show that it is possible to produce reinforced concrete elements using the process.
Project data
The research project “Beyond 3D printing – A novel spatial printing technology for lightweight spaceframe concrete structures” is being funded with 119,000 euros by the Volkswagen Foundation as part of the “Experiment!” funding initiative, which has now ended. In it, the foundation supported radically new and daring research ideas. The Institute for Building Materials, Concrete Construction and Fire Safety (iBMB), Division of Building Materials, and the Institute of Structural Design (ITE) are involved in the project.
Researchers: Aileen Vandenberg, Noor Khadher, Yinan Xiao, Norman Hack, Harald Kloft, Dirk Lowke
Publication
Dirk Lowke, Aileen Vandenberg, Alexandre Pierre, Amaury Thomas, Harald Kloft, Norman Hack: Injection 3D concrete printing in a carrier liquid — Underlying physics and applications to lightweight space frame structures. Cement and Concrete Composites 2021, 104169, ISSN 0958-9465.
https://doi.org/10.1016/j.cemconcomp.2021.104169
N. Hack, I. Dressler, L. Brohmann, S. Gantner, D. Lowke, H. Kloft: Injection 3D Concrete Printing (I3DCP): Basic Principles And Case Studies, Materials. (2020).
https://doi.org/https://doi.org/10.3390/ma13051093.