The Optimal Air Supply Tim Wittmann researches air supply systems for hydrogen fuel cells in aircraft propulsion systems
Hydrogen fuel cells are among the technologies with particular potential when it comes to sustainable aircraft propulsion systems. Tim Wittmann, a doctoral student at the Institute of Jet Propulsion and Turbomachinery (IFAS) at Technische Universität Braunschweig, is researching a system design for the air supply of fuel cells at high altitudes. Additional impetus for his work was provided by a research grant from the Cluster of Excellence SE²A – Sustainable and Energy-Efficient Aviation at TU Braunschweig.
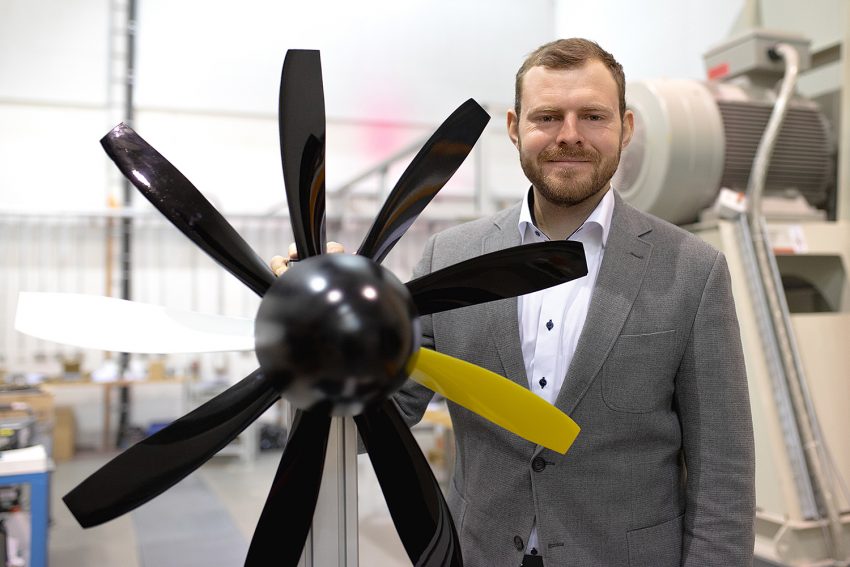
Timm Wittmann is doing research on an air supply system for fuel cells at high altitudes. Photo credit: Max Fuhrmann/TU Braunschweig
Mr Wittmann, what are the advantages of an aircraft powered by hydrogen fuel cells?
This propulsion concept is almost emission-free. The fuel cell converts hydrogen directly into electrical energy for the electric motor with the help of oxygen. The only waste product is water vapour.
In your research, you concentrate on the air supply system. Why?
The air supply system is an important part of the fuel cell system. It supplies the fuel cell with compressed, humidified and heated ambient air. It also ensures that the liquid water produced during the fuel cell reaction is removed. While the tank system can supply the hydrogen at almost constant pressure, the ambient conditions vary greatly with the altitude. Especially at high altitudes, the ambient pressure and temperature are too low – the air up there is thin and cold – to operate a fuel cell efficiently. Therefore, before the ambient air is used in the fuel cell, it must be compressed and heated. We have investigated which operating parameters and system architectures are optimal here. Especially at high altitudes, this is a complex optimisation task.
How did you approach this?
We built an analytical model with a broad parameter space. Two central aspects of our modelling are calculating the fuel cell voltage as accurately as possible as a function of pressure, temperature, oxygen stoichiometry and humidity, and taking condensation in the turbine into account. Based on our model, we have determined optimal operating parameters and system architectures for two use cases: for a passenger aircraft at a flight altitude of 7 kilometres and for an unmanned aircraft for telecommunication services at a flight altitude of 18 kilometres.
What are the optimal operating parameters?
The optimal air supply for a fuel cell depends on the current density of the fuel cell and the flight altitude. The current density is the measure of the load on the fuel cell. The higher the current density, the more compact and lighter the cell. However, the efficiency is also lower. For short flight distances, a higher current density is better. This requires higher pressures and oxygen concentrations. For long flight distances, the fuel cell must be particularly efficient. The current density is therefore lower, as are the optimal pressures and oxygen concentrations. Condensation in the turbine protects the air supply system from temperatures below freezing. The released condensation heat increases the turbine output and thus improves the efficiency. In addition, our modelling has shown that the air system does not necessarily need a heat exchanger for air cooling. Evaporative humidification can also be used for this purpose. This simplifies the system and saves weight – in aviation, as we know, every kilogram counts.
You are doing a kind of pioneering work with your research, right?
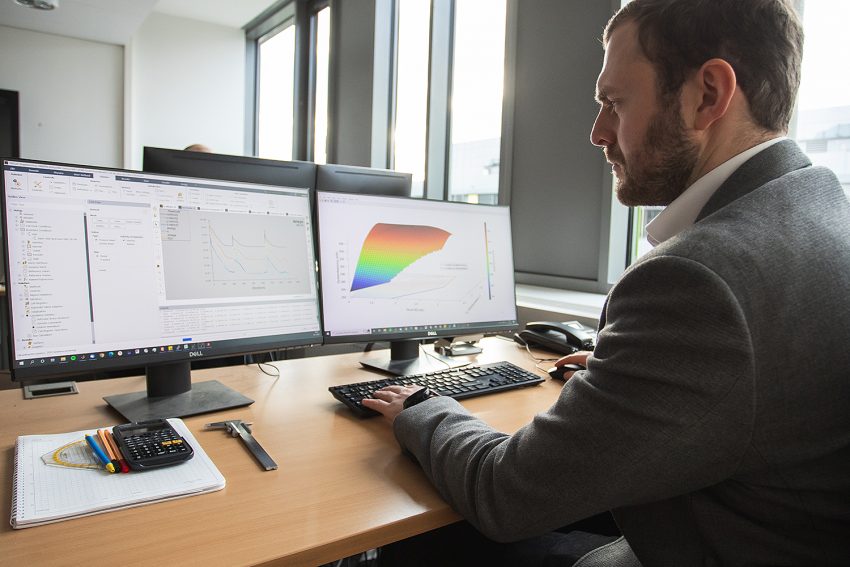
With his research, Timm Wittmann wants to contribute to making climate-neutral flying possible. Photo credit: Max Fuhrmann/TU Braunschweig
We can certainly draw on fundamental research for the automotive sector. But the use of hydrogen fuel cell technology for aviation applications is more complex. In addition, many publications do not explicitly consider the air supply system in the system design. We are at the forefront of this with our research.
Your research results are also important for the Cluster of Excellence SE²A – Sustainable and Energy-Efficient Aviation.
Yes, the topic of energy storage and conversion in aircraft is one of the research priorities of the SE²A cluster at TU Braunschweig. The cluster therefore made it possible for me to receive a research scholarship. As a visiting doctoral student, I did research for six months at the National Fuel Cell Research Center at the University of California in Irvine. There I was also able to further deepen my knowledge of electrochemistry. This field is playing an increasingly important role for aerospace engineers when it comes to sustainable propulsion technologies with batteries or fuel cells.
What excites you about your research?
I consider it a stroke of luck to be able to do research in this day and age. It’s no longer just about achieving a few more percentage points of improvement with new technologies. We have the chance and also the task to develop revolutionary technologies that will make climate-neutral flying possible at all. So with my research I am making a small contribution to the decarbonisation of aviation. The hydrogen fuel cell as a propulsion technology could be in use in about 15 to 20 years. Until then, there is still a lot to do. Because this solution must not only be technically feasible, but also meet the high safety standards that apply in aviation.