Reinforced Concrete Components From the 3D Printer Dr. Inka Dreßler on her research in the SFB "Additive Manufacturing in Construction"
Houses from the 3D printer: What was still a vision of the future a few years ago is now possible. In Germany, as well, the first prototypes were recently created in this way for a residential building in Beckum near Münster and an apartment building in Wallenhausen near Ulm. Scientists at the Technische Universität Braunschweig and the Technische Universität München are conducting research in the Collaborative Research Center/Transregional Collaborative Research Center “Additive Manufacturing in the Construction Industry” (SFB/TRR277) to determine which materials and printing processes are suitable for this new type of manufacturing technology and what the digital interfaces must look like. Dr. Inka Dreßler from the Institute of Building Materials, Concrete Construction and Fire Safety (iBMB), Division of Building Materials, is one of them. She would like to know, for example: How can reinforced concrete components be produced as geometrically precise and high-strength as possible using 3D printing? To this end, she has now received support from experts from France during a TRR277-funded research stay in Brittany.
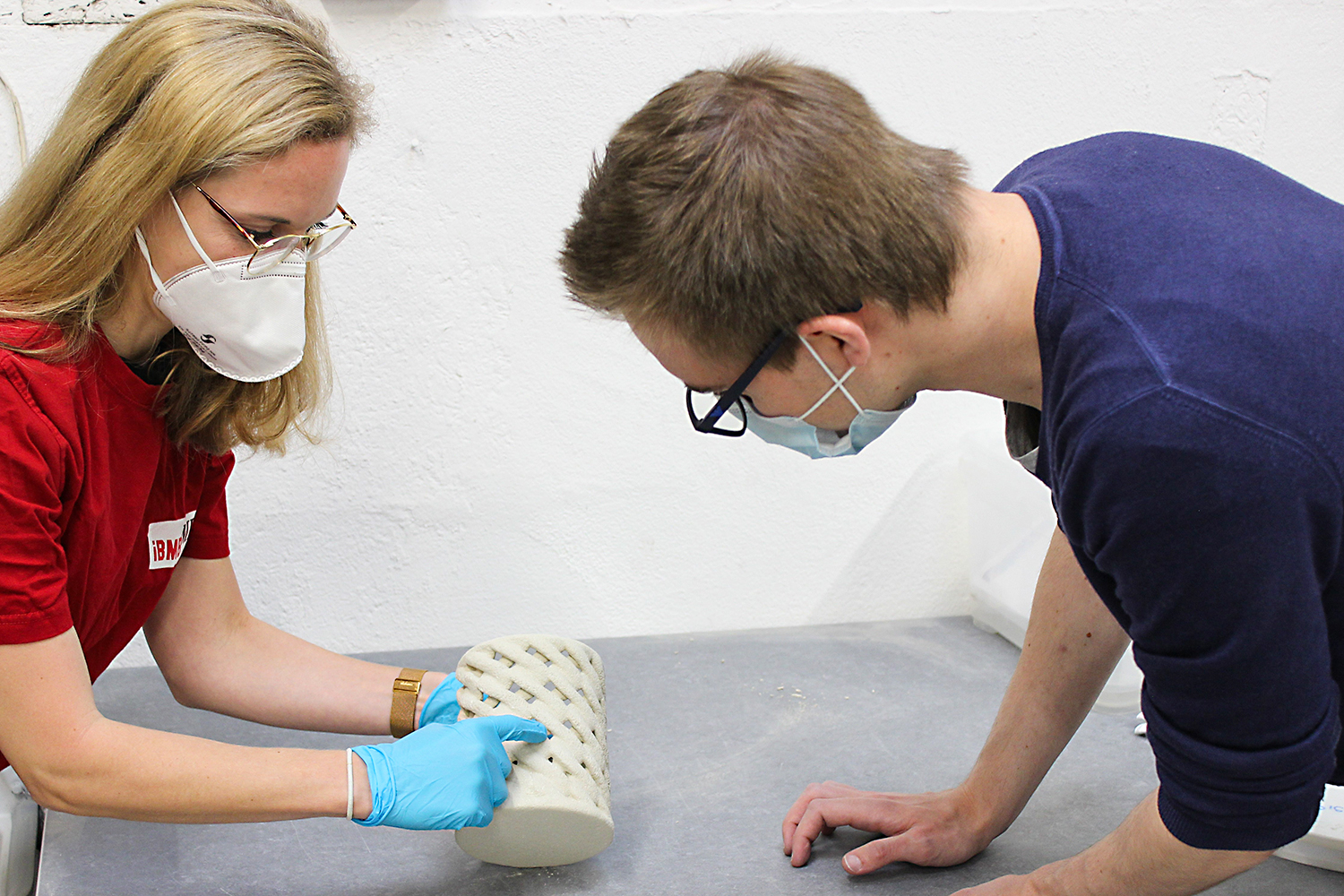
Dr. Inka Dreßler and her colleague Friedrich Herding discuss the printing result. Picture credits: iBMB/TU Braunschweig
Inka Dreßler is involved in two research projects out of a total of 22 in TRR277: A01 and A04. What is behind them? A01 is a project on particle bed 3D printing by selective cement activation, A04 deals with the production of additively manufactured reinforced shotcrete elements. But what is a particle bed 3D printing process? In the multi-material powder bed printing technique, a mixture of sand and cement is spread in a single layer. At the point where the solid structure is to be created, the scientists* activate it with a liquid, triggering the hardening process. This is repeated for each layer to build a three-dimensional structure. The advantage: Compared to other additive manufacturing processes in the construction industry, this method has almost no restrictions on the choice of geometry and thus on the design. At present, the main areas of application are still in the furniture sector and in the design of facade elements. In the future, it will also be possible to produce structural components.
Cooperation with experts in Brittany
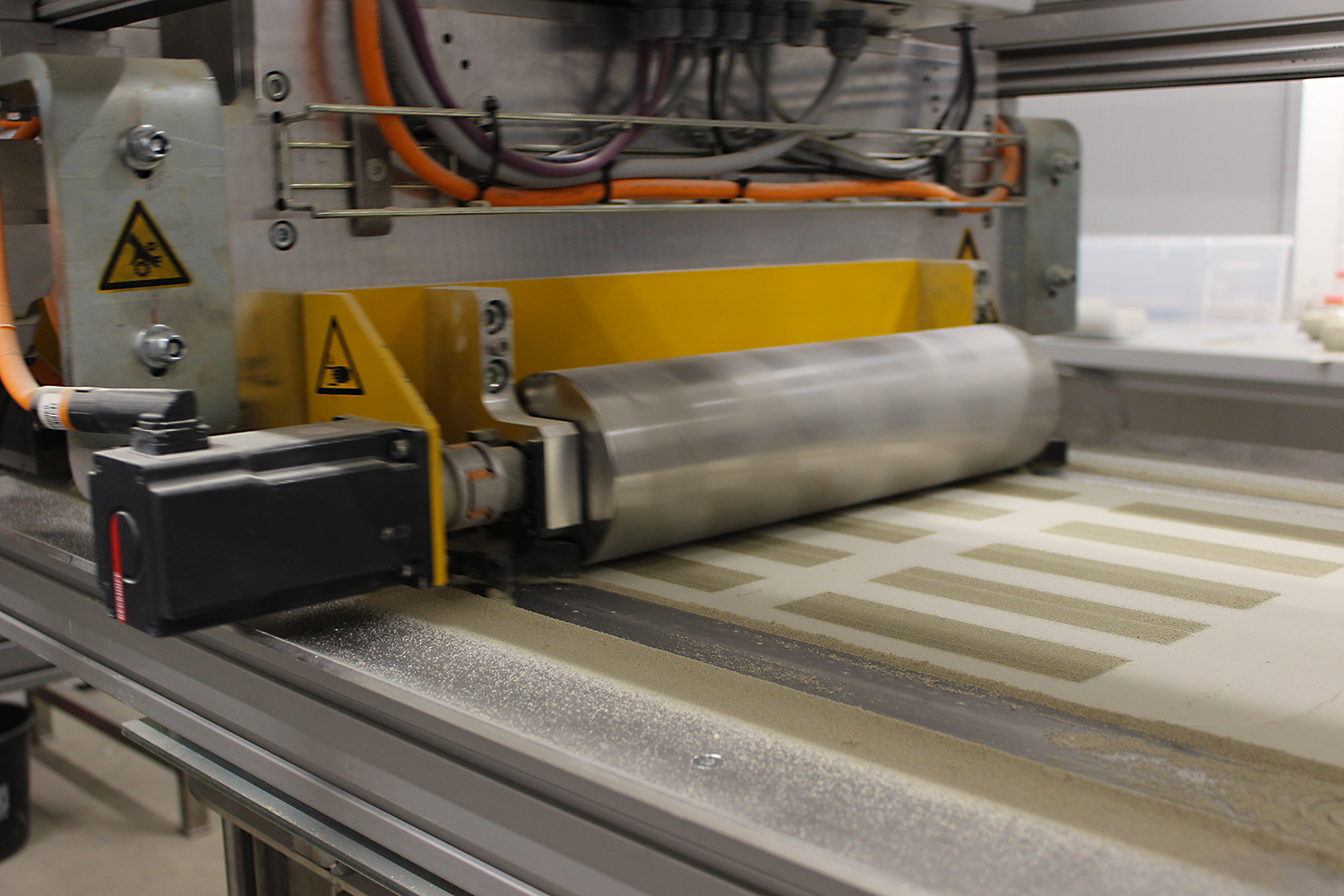
The new research printer at the Institute for Building Materials, Solid Construction and Fire Protection. Picture credits: Inka Dreßler/TU Braunschweig
In the project, Inka Dreßler and other researchers from the Institute of Building Materials, Concrete Construction and Fire Safety and the Institute for Particle Technology are investigating the material-process interaction of this process. A central aspect is the penetration of the liquid into the particle bed. What is the right amount of liquid to mechanically couple the two layers? “If I apply a lot of water to the sand-cement mixture, it can go completely through the whole layer. At the same time, it also spreads to the side and then I end up with a misshapen component,” explains Inka Dreßler. That’s why the scientist investigated the following questions during her research stay in France: What factors influence how the fluid is distributed in the layers? How can this be actively controlled and predicted? In the end, Inka Dreßler would like to develop a formula that describes how, for example, the particle size changes the penetration depth of the fluid. “This is important in order to be able to produce both geometrically precise and mechanically high-strength components in the future.”
The senior engineer did the modeling and basic experiments at the Université Bretagne Sud in Lorient. There she was a visiting scientist with Professor Arnaud Perrot, an expert in the field of analytical modeling. Professor Dirk Lowke, head of the Division of Building Materials at the iBMB, project leader and board member of TRR 277, had already worked successfully with Professor Perrot in the past, so that cooperation came about quickly and without complications.
Cross-national research proposal
For Inka Dreßler, the stay was an excellent opportunity to gain new impetus for her project and to expand her language skills. The scientists exchanged technical information in English. For everyday communication, they had agreed on French. “I already had a solid foundation and could build on it well,” says the civil engineer.
After the two months in Lorient, Inka Dreßler is now working on verifying her model with the particle bed printer at the iBMB. The scientists in Braunschweig and Lorient want to further establish the cooperation and are already writing a new research proposal together.
On the way to the highest possible strength concrete
The goal for the particle bed pressure process is also to increase the strength to the point where it is comparable to normal concrete. “We’re already well on the way there – currently in the range of 20 megapascals, which corresponds to a medium normal concrete.” Inka Dreßler is also working very closely here with the Institute for Particle Technology. The scientists are coating particles to investigate how they can precisely control the penetration of water into the layer. In this way, the researchers can create very specific effects by using different surface properties of the particles. “Be it that the water does not penetrate locally, be it that the particles can be compacted better in order to increase the strength or also by coating sand particles directly with cement so that we do not have any segregation phenomenon,” explains Inka Dreßler.
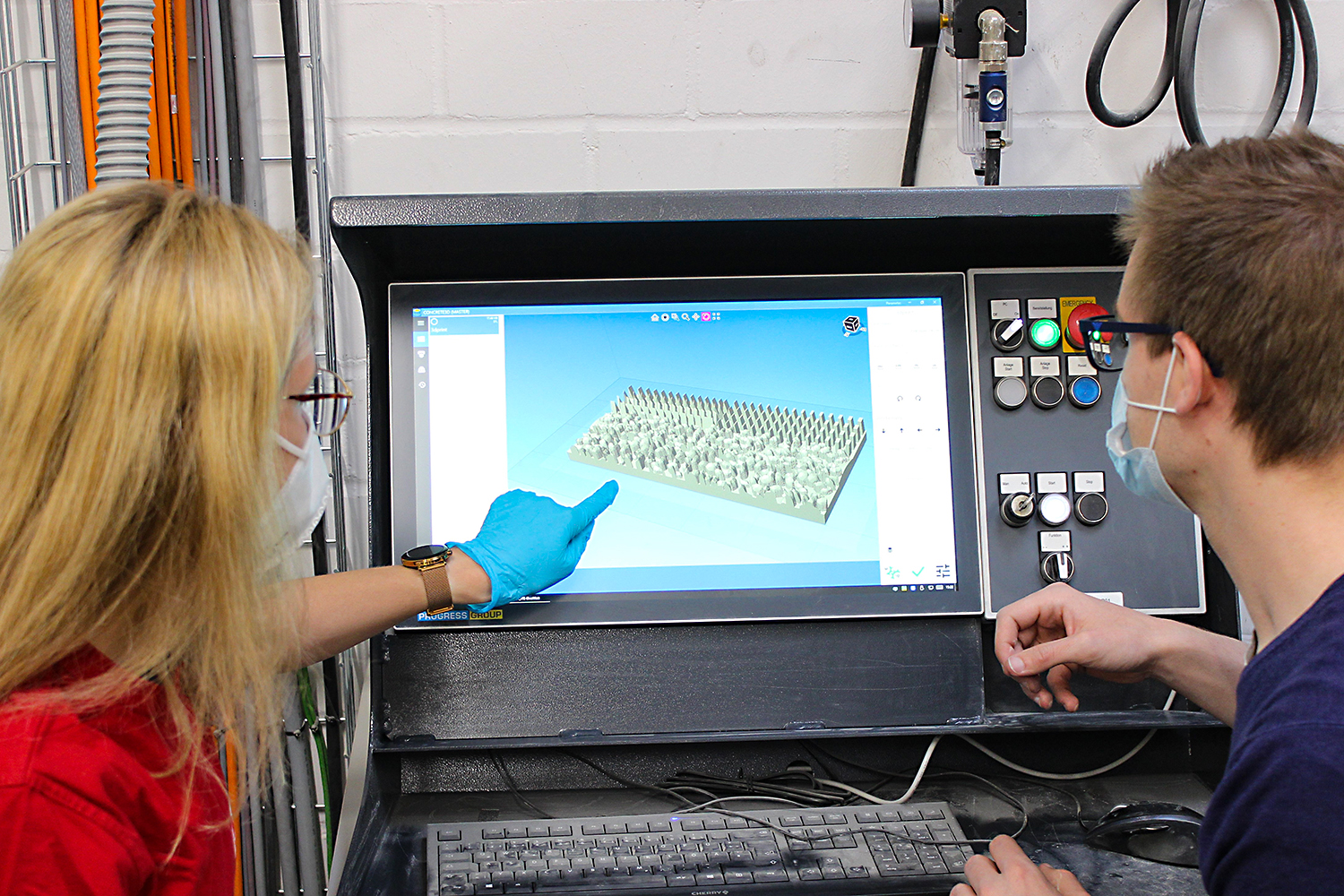
Dr. Inka Dreßler and her colleague Friedrich Herding plan the next print. Picture credits: iBMB/TU Braunschweig
What the scientist appreciates most about additive manufacturing is the diversity of research questions. How do you find the optimum to completely master the process? In addition, she says, it offers enormous potential for saving materials in the construction industry and thus for working more ecologically in the city of the future. Researchers from Zurich, for example, have produced a ceiling element that requires 70 percent less material than a conventional component and yet has the same load-bearing capacity, reports Inka Dreßler.
Using recycled material
In addition to the two projects in TRR277, the institute is working on three other additive manufacturing processes, for example “Injection 3D Printing,” which allows the scientists* to produce completely free form elements, “Selective paste intrusion” or “Large Particle 3D-Concrete Printing.” Here, the research team consisting of scientists from the Institute of Structural Design and the Institute of Building Materials, Concrete Construction and Fire Safety is using the Digital Building Fabrication Laboratory (DBFL) to investigate how recycled aggregate can be used in additive manufacturing. “Typically in additive manufacturing, cement volumes are quite high, which is a disadvantage ecologically,” says Inka Dreßler. “In the worst case, this means that you have saved a lot of material, but the CO2 emissions are still just as high as for a normal component. That’s why the idea is to use recycled aggregates while reducing the amount of cement in the component.”
Automation through 3D printing processes will change some work patterns in construction, he said. “But a lot of things will be safer and more precise in the long run because you can control them specifically. A defect that’s just been detected can be fixed right in the manufacturing process. This might otherwise go undetected. It’s a dynamic field of research where you can make a lot of difference!”