Picture of the month: When fibres support the concrete wall Reinforcement for 3D printing from the "Additive Manufacturing in Construction" Collaborative Research Centre
Concrete can absorb compressive forces, but when bending moments and tensile forces occur, the material can crack. To prevent this, reinforcement is used, for example in a base plate when building a house, often made of steel in the form of meshes or cages. Reinforcement is also necessary in 3D printing with cementitious materials in order to create load-bearing structures. One of the greatest challenges in additive manufacturing, because the good old “rebar”, as the reinforcing steel is also called, is not used here. Instead, steel structures are imprinted or filigree metal strands are carried along in the concrete strand. Scientists at TU Braunschweig are also developing textile-based reinforcement strategies in the Collaborative Research Center Transregio 277 “Additive Manufacturing in Construction”.
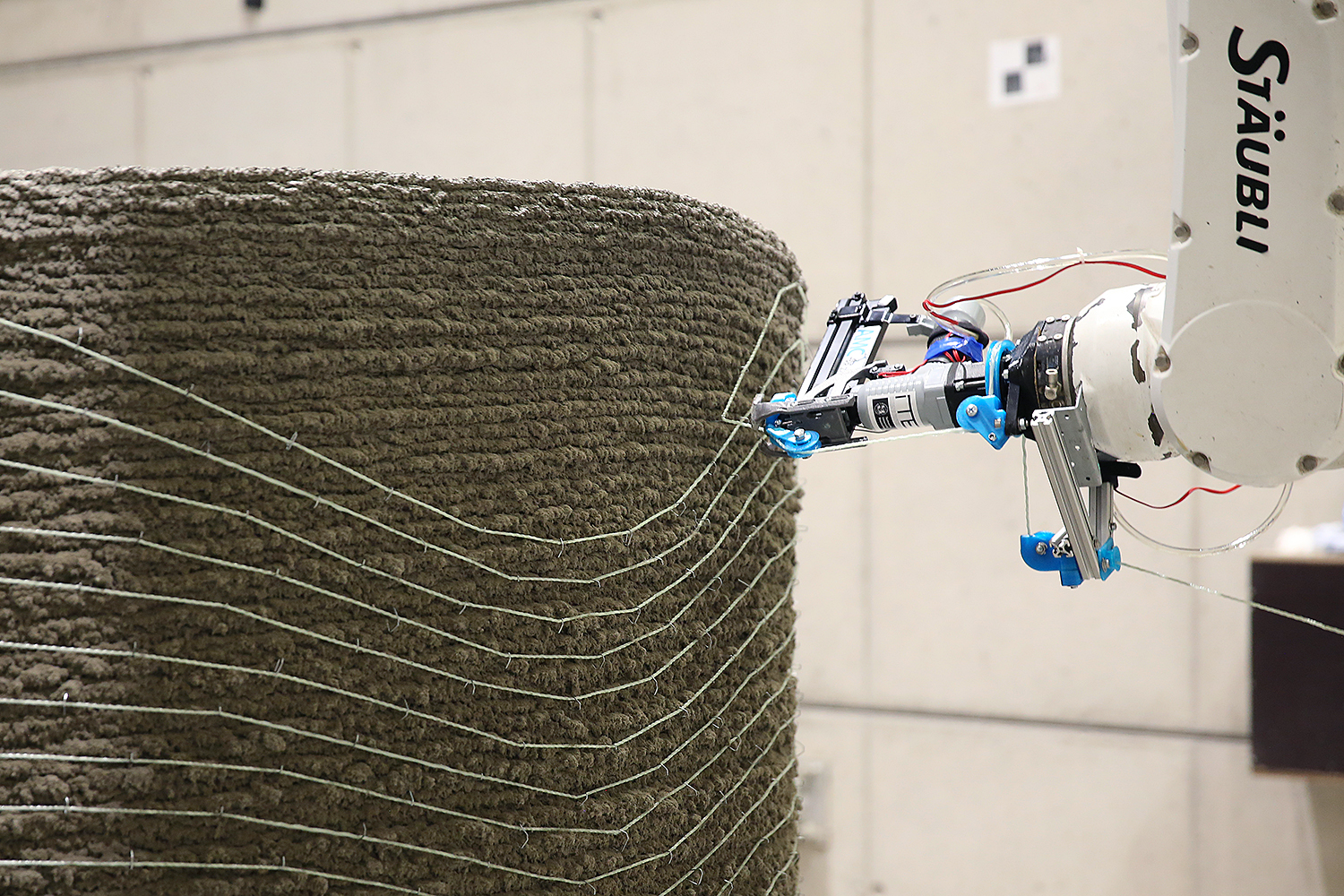
Individualised fibre composite reinforcement is integrated into 3D-printed concrete components. Photo credit: Stefan Gantner/TU Braunschweig
In AMC project A05, led by Professor Norman Hack from the Institute of Structural Design (ITE) and Professor Christian Hühne from the Institute of Mechanics and Adaptronics, scientists Stefan Gantner and Tom Rothe are investigating the integration of individualised fibre composite reinforcement in 3D-printed concrete components. The advantages of a textile-based reinforcement: Due to the corrosion resistance, the height of the concrete cover can be reduced and thus the CO2 footprint can be significantly improved. In addition, the material is flexible and therefore particularly suitable for producing individualised structures.
As shown in the “Picture of the Month”, the fibre composite reinforcement is created from fibre strands in the Digital Building Fabrication Laboratory (DBFL) of the ITE, which is integrated into the additive concrete manufacturing processes in a load-path-compatible manner by means of the robot-based end effector, the robot’s hand, so to speak. For this purpose, the processes of core winding, in which reinforcement fibres are wound and fixed on the concrete core, and shotcrete 3D printing are combined. The aim of the project is to create individual concrete structures with fibre composite reinforcement by 3D printing directly on site at the construction site.
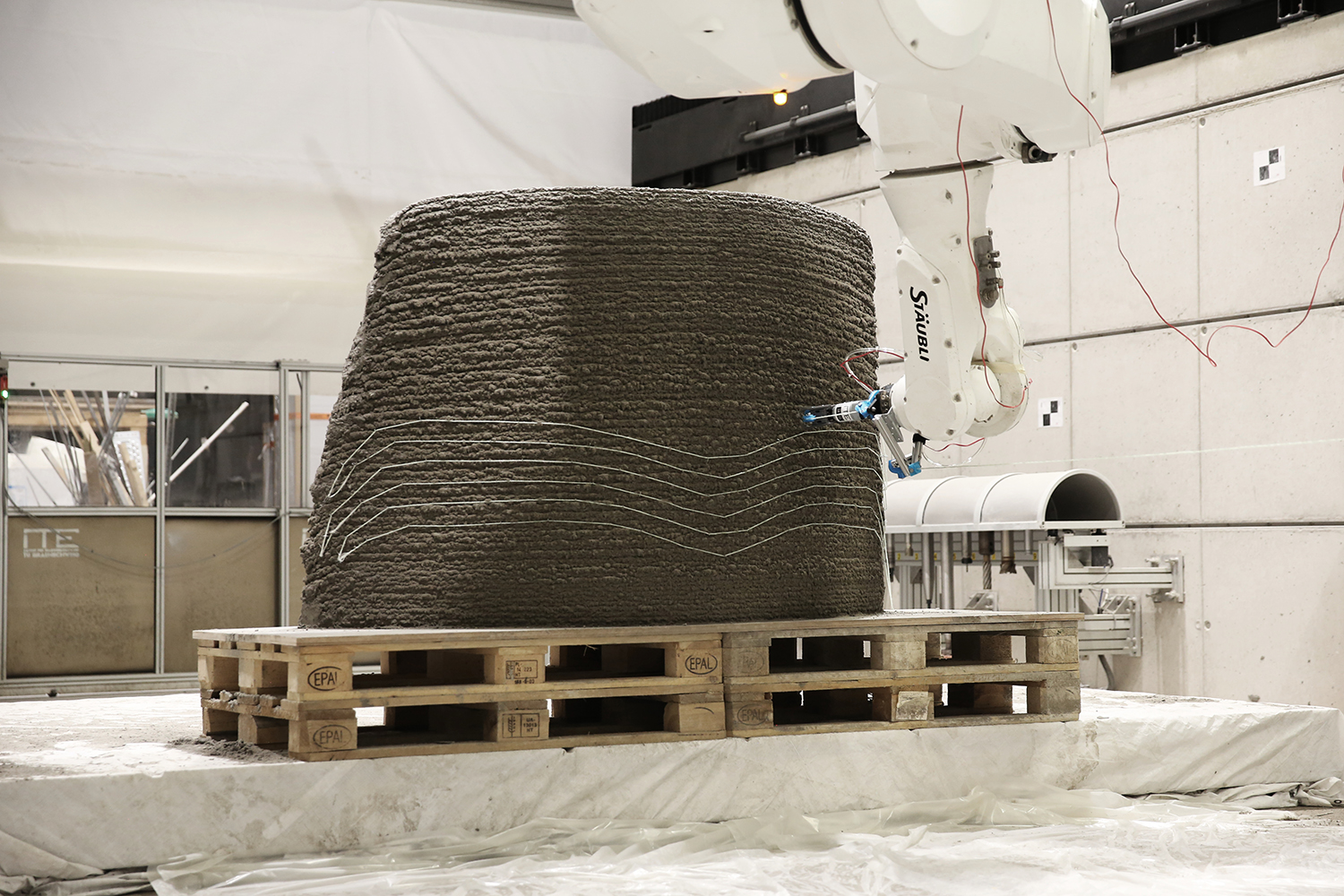
In ITE’s Digital Building Fabrication Laboratory (DBFL), fibre strands are used to create the fibre composite reinforcement, which is integrated into the additive concrete manufacturing processes. Photo credit: Stefan Gantner/TU Braunschweig
Additive manufacturing in construction
The Collaborative Research Centre Transregio 277 Additive Manufacturing in Construction (AMC) aims to play a significant role in shaping the digitalisation of construction. Within the levels of materials and processes, computer-aided modelling and control, and planning and construction, the AMC researches resource- and energy-efficient as well as sustainable, recyclable and digital construction. Innovative 3D printing methods are used to completely rethink materials, processes and optimised design.
Further information: https://amc-trr277.de/