Picture of the month: The Research Engine Research on component fatigue and the construction of a digital twin
In 2022, the Institute of Jet Propulsion and Turbomachinery (IFAS), in cooperation with MTU Maintenance Hannover GmbH and the TFD of Leibniz University Hannover, successfully conducted two measurement campaigns with the research engine of TU Braunschweig. The measurement campaign consisted of two engine setups with different compressor blades. The data obtained is now being used in several research projects in the field of component fatigue as well as the construction of a digital twin of the engine.
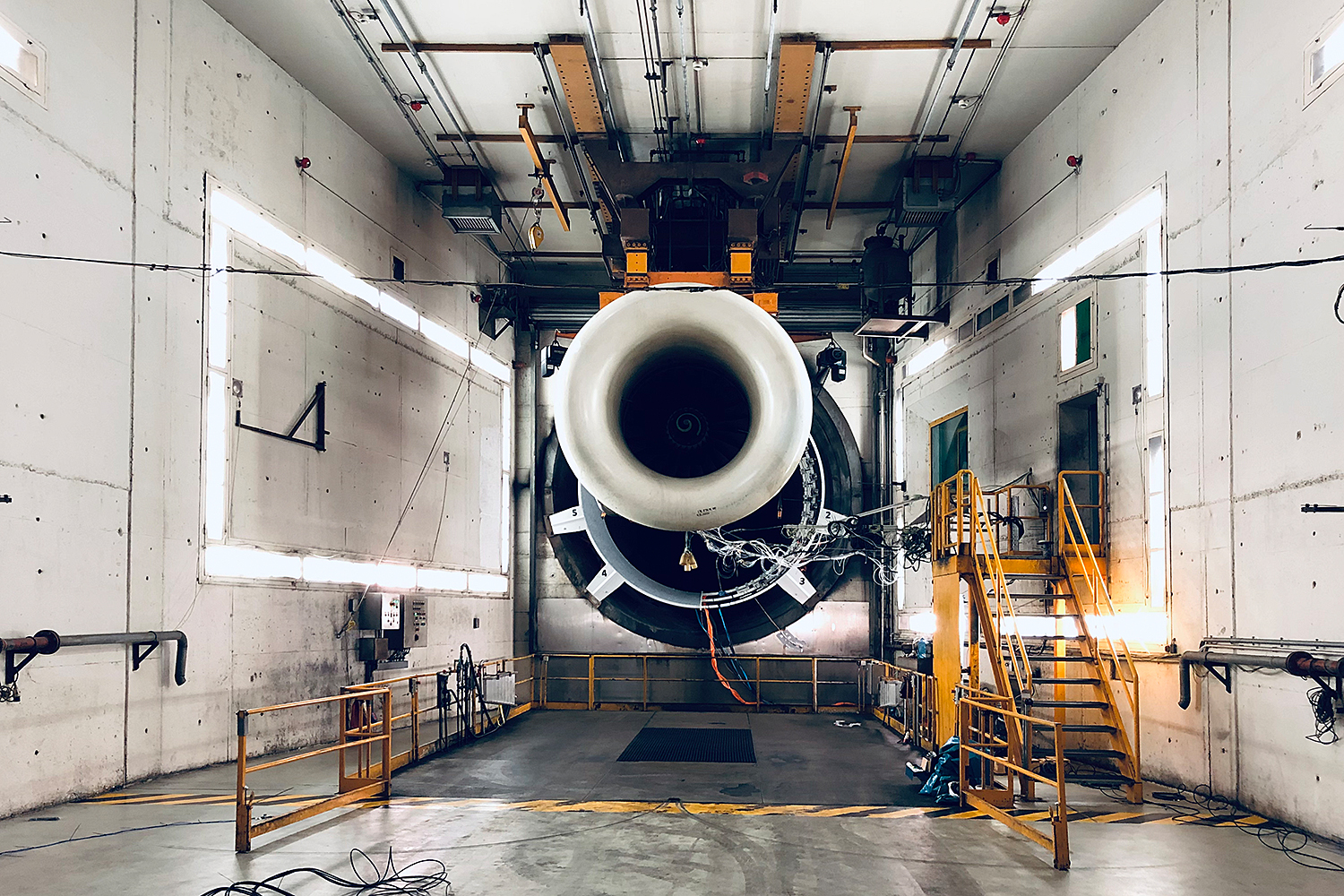
Research engine from the Institute of Jet Propulsion and Turbomachinery (IFAS): Photo credit: Jan Göing/TU Braunschweig
This picture shows the research engine from the Institute of Jet Propulsion and Turbomachinery. It is a turbofan engine of the type IAE V2500-A1, which was designed for the Airbus A320 aircraft. For research purposes, it was equipped with over 100 special probes. The research engine was operated by MTU Maintenance Hannover GmbH. The picture was taken shortly before the first commissioning of a total of six test runs and eight measurement days.
Influence of wear and tear on fuel consumption
Over the last twelve years, researchers have developed mathematical models that assess the condition of complex capital assets – including engines – in the context of digitalisation and the “digital twin”. These models make it possible to determine the influence of wear and tear such as erosion, corrosion and contamination on fuel consumption. As a decision-making aid when planning maintenance and servicing of the engine, these models provide valuable information.
To check the accuracy of the mathematical models, the research engine was equipped with additional measurement technology and put into operation. Different high-pressure compressor blading was used and the combustion chamber was modified to provoke disturbances and perform adapted manoeuvres.
Real test conditions
The specific feature of this project was the work on a real engine at pressures of over 30 bar and temperatures of over 1000 Kelvin. Strong interdisciplinary cooperation between researchers, mechanics and engineers was required to successfully complete the project.