Picture of the Month: Graphite Anode in the drying channel From the Battery LabFactory Braunschweig (BLB)
It has become an integral part of many areas of our lives and is used primarily as a mobile energy storage device in smartphones, notebooks and electric cars: the lithium-ion battery is currently in the focus of science in order to economically and eco-efficiently implement topics such as the energy revolution and the change in propulsion technologies. Our picture of the month was taken in the drying channel of the continuous coating line at Battery LabFactory Braunschweig (BLB). These are the process steps “coating and drying”, two of 18 process steps in total that a lithium-ion battery passes through during production.
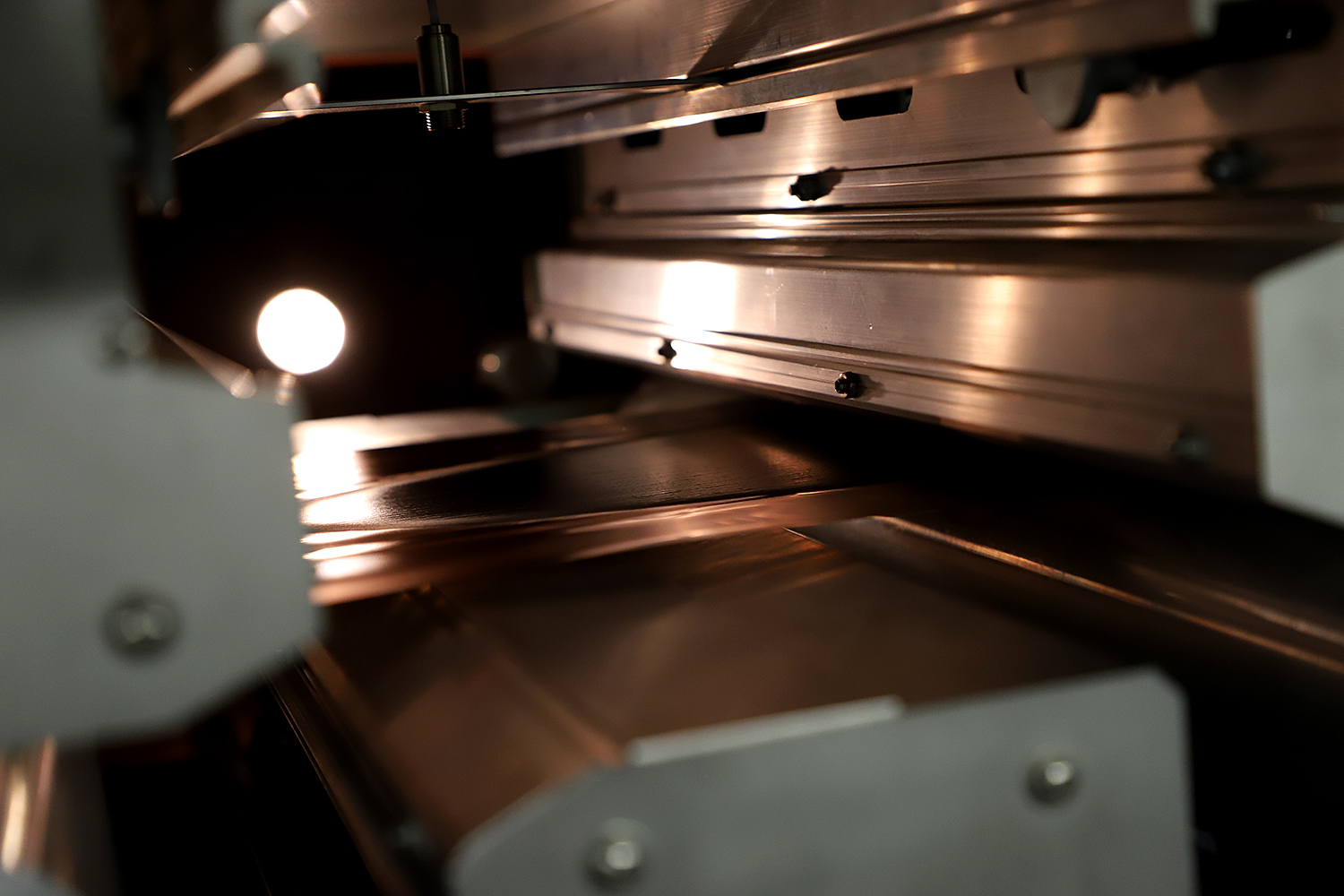
Graphite anode in the drying channel of the continuous coating line. Picture credits: Marisol Glasserman/TU Braunschweig
In the simplest case, a lithium-ion battery cell consists of two electrodes (anode and cathode), an electrolyte and the separator, which electrically separates the two electrodes from each other. The picture of the month shows a copper foil on which the active electrochemical and passive materials were applied in advance using a comma bar process, i.e. a coating process. This is a graphite anode that represents the negative electrode.
Of the various institutes that are active at BLB, the Institute for Particle Technology deals, among other things, with the process steps of coating and drying. An alternative process that is being investigated at BLB is slot die coating. Besides the advantage of the intermittent coating, a coating with interruptions, the independence of the coating thickness from the properties of the electrode paste is given here.
Drying is a cost-intensive step in all industrial processes. The main focus is on technologies such as infrared drying to increase drying speeds and reduce energy costs. Furthermore, coating errors and binder migration can be avoided through optimized drying, thus reducing material waste.