New construction: extremely light, extremely free, extremely printed Professor Dirk Lowke on a vision for the construction industry
How can we print an extremely lightweight spatial building structure with concrete? The Institute for Building Materials, Concrete Construction and Fire Safety (iBMB) and the Institute of Structural Design (ITE) at Technische Universität Braunschweig are researching this. We talked to Professor Dirk Lowke, head of the Division of Building Materials at iBMB, about the “Beyond 3D Printing” project.
Professor Lowke, the title of your research project is “Beyond 3D Printing”. What does “beyond” mean in this context?
If we take a closer look at 3D printing, we notice that we don’t actually print in 3D. We can only ever print on top of an existing layer. So in the simplest case, we print vertically upwards or – if we’re a bit more daring – we offset the layers a bit so that an oblique structure is created. Ultimately, this is then “2.5D printing”. However, with the process we are developing in the project, we are really free to position the material. We can print the structure into any orientation in space. That would be “real” 3D printing, a materialization in space. That is the decisive difference. This does not yet exist in the construction industry. In other areas, such approaches are already being pursued in research, for example in medicine, where tissue structures are to be printed.
Can you give us an example from the construction industry?
The first 3D-printed house is a nice example. It’s built vertically upward strand by strand. But with the window cutout, you face a problem: What do I do when I get to the top of the window? At this point, I can’t just print upward into the air. This is where the limitations of the layering process become apparent.
In your experiments, you first print structures on a small scale using “Injection 3D Concrete Printing”, a concrete strand into a support gel. How could the process be applied in the construction industry?
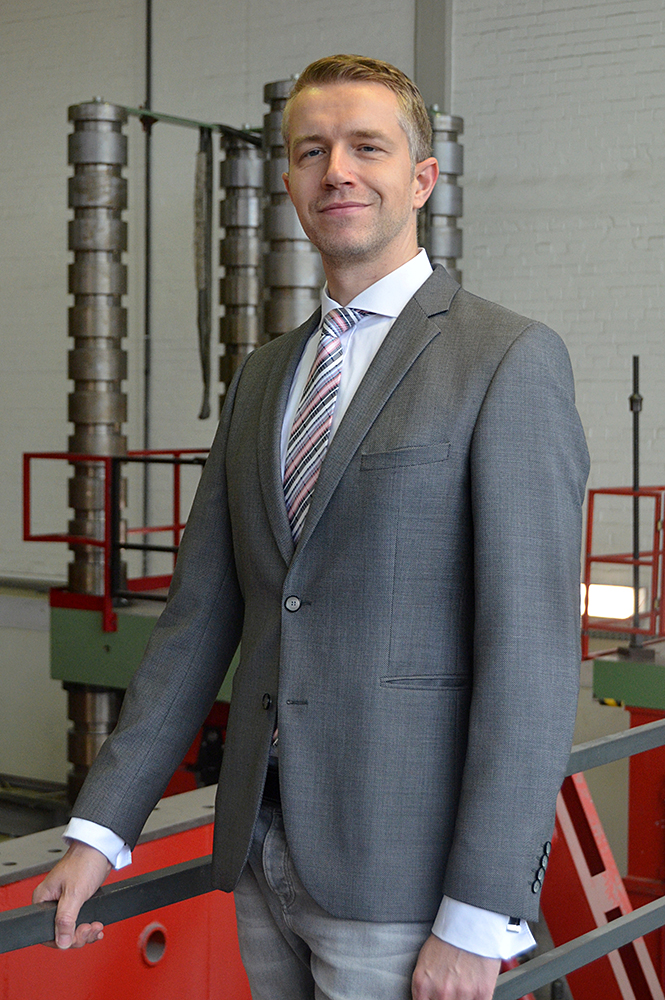
Prof. Dirk Lowke is Head of the Division of Concrete Construction at the Institute of Building Materials, Concrete Construction and Fire Safety (iBMB). Picture credits: Daniela Klar/TU Braunschweig
Of course, the gel is less suitable for large-scale application because, among other things, it is very expensive. We are replacing the gel with a mineral suspension, which is cheaper, ecologically harmless and recyclable on a large scale. The carrier liquid – a rock flour suspension similar to a mud pack – can be drained off and reused.
The focus is on precast construction, for example of bridge components. The individual segments are printed in the factory, transported to the construction site and assembled on site. In the factory, a correspondingly large container is then needed to produce these prefabricated parts.
But first, we want to print on a larger scale here at TU Braunschweig. The Digital Building Fabrication Laboratory (DBFL) at the Institute of Structural Design (ITE) has the appropriate dimensions to be able to print such structures and precast parts.
Two years ago, you patented Injection 3D Concrete Printing.
Right. Our patent (together with Professor Norman Hack and Professor Harald Kloft) goes even further than what I have already reported. The carrier material into which the free structure is printed could also be a very inexpensive and ecologically low-impact concrete. This could be used to fill the container, which already has the shape of a normal conventional structure, such as a beam that I place from one support to the next. Since the lower performance concrete can’t carry the load, we would then imprint a spatial structure in that support material with a high performance concrete. We thus hid a very high-performance concrete in the low-cost concrete, which is responsible for the load transfer.
How did the idea for the research project come about?
Actually, I had the basic idea for it for quite some time because, as a “material person,” I find the possibility of being able to print something in space very exciting. However, I didn’t have the vision of what I could do with it on a large scale. Then, when I started talking about it with Professor Norman Hack and Professor Harald Kloft from the ITE of the architecture department, the idea of the research project was quickly born. In the field of additive manufacturing, it is important to work in an interdisciplinary way. In this field, you don’t get very far with individual expertise. As a civil engineer, I can make the concrete float in liquid, but the architect can tell me what will come out of it and how I can use these spatial structures in architecture. And he can imagine how we can implement this on a large scale at DBFL. The exchange with different disciplines works very well here.
What are the further plans?
If the research project is successful, one option is to establish Injection 3D Concrete Printing in the next funding phase of the Collaborative Research Center TRR 277 “Additive Manufacturing in Construction (AMC) – The Challenge of Large Scale”. With this project, we hope to show that the process is a serious vision for the construction industry. Innovative research needs courage!