Laboratory at TU Braunschweig for Residual Stress Analysis Successfully Accredited NOSA supports engineers (and partner) from research and industry to optimize and analyze components
At the Institute of Joining and Welding Technology at Technische Universität Braunschweig, residual stresses can now be measured and analyzed at “Norddeutsches Zentrum für Spannungsanalytik” (NOSA) in the recently accredited test laboratory. This makes the TU Braunschweig the perfect contact for industry and companies when it comes to X-ray residual stress determination.
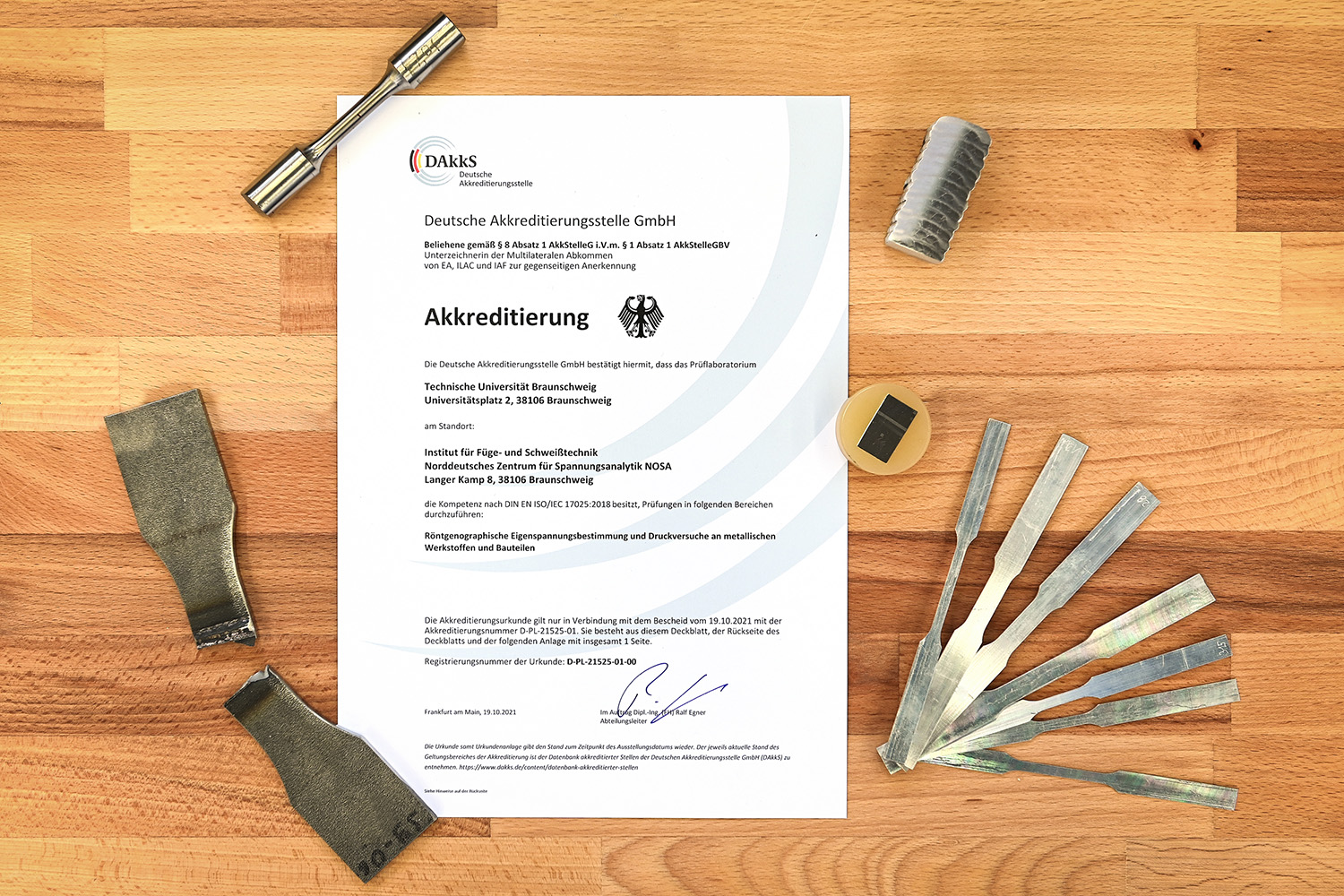
Accreditation certificate. Bildnachweis: Markus Köhler, TU Braunschweig
Residual stresses are internal stresses that occur in the component without the action of external forces. It arise during production or manufacturing under the effect of plastic deformation of microscopic and macroscopic material areas. They also play a role when heat is applied to any type of component processing, e.g. gear components, turbines or other components in the automotive and aerospace industries.
Residual stresses can have both a positive and a negative influence on component behavior. Due to the broad knowledge of the effect of residual stresses accumulated over decades, they now represent an industrially used engineering tool for the optimization of component properties, especially for high-strength and ultrahigh-strength materials
High requirements for competence confirmed
Since many years, the Institute of Joining and Welding Technology at the Technische Universität Braunschweig has been involved in the determination of residual stresses in metallic materials and components as part of the “Norddeutsches Zentrum für Spannungsanalytik” (NOSA). Destructive and non-destructive testing methods are used for materials analysis. Since this year, NOSA has been accredited by the German Accreditation Office (DAkkS) as a testing laboratory for residual stress analysis according to DIN 17025. This confirms the high requirements on competence, the uniform working method as well as the quality standards.
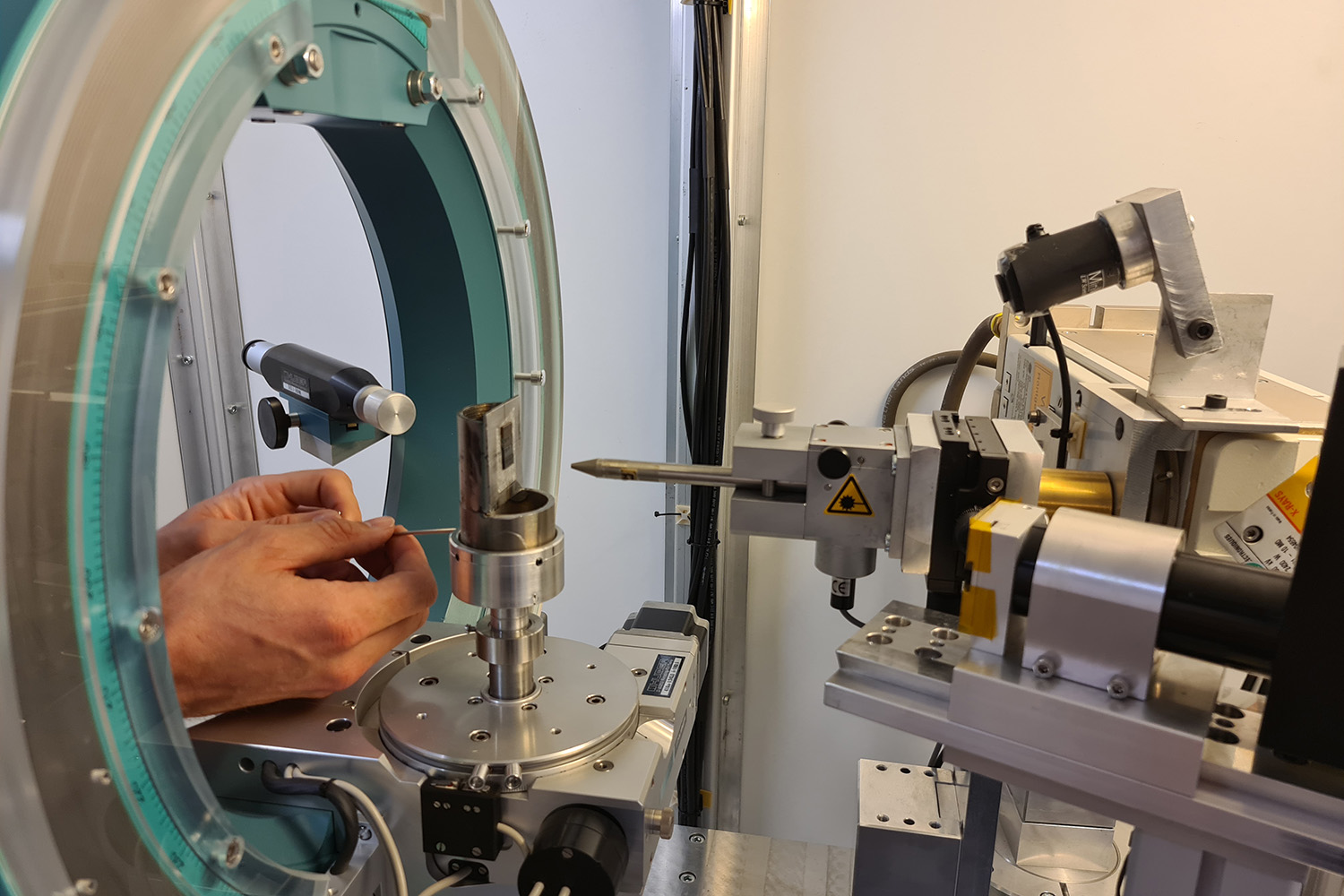
Test lab: Positioning of a sample in the X-ray diffractometer. Bildnachweis: Paul Diekhoff, TU Braunschweig
Accreditation basic prerequisite for many industry cooperations
A large number of residual stress-, phase- and texture analyses are carried out daily in various specially developed stationary and mobile X-ray diffractometers as part of basic and application-oriented research projects. With a diffractometer, non-destructive investigations of the structure of crystalline phases in materials can be carried out.
Since the determination of residual stress states has long been an industrially established method for quality control during series production and prototype development, the institute is also a service partner in this field of bilateral industrial projects. Such tests are offered to companies that are interested in such analyses but do not have the necessary know-how or equipment themselves. “The accreditation of the testing laboratory is a basic requirement for many industrial partners for cooperative projects and represents a great development opportunity for NOSA,” says NOSA director Dr. Thomas Nitschke-Pagel.
In the laboratories of the Institute for Joining and Welding Technology, stress states of materials and components are analyzed and evaluated. “New testing methods – such as the aforementioned use of mobile X-ray diffractometers – are constantly being developed and improved in order to guarantee customers from research and industry fast and precise analyses with the highest quality standards in the future,” says Thomas Nitschke-Pagel, head of the testing laboratory.