“I see so many answers in the building material clay” An interview with Joschua Gosslar on building with clay
Does the future of building lie right beneath our feet in the earth? “I see many answers for construction in earth“ says Joschua Gosslar. The research associate at the Institute for Structural Design (Institut für Tragwerksentwurf) at TU Braunschweig conducts research on the robotically assisted manufacturing of building components made of rammed clay and leads seminars on clay construction for architecture students. Bianca Loschinsky talked to him about his research on this sustainable building material.
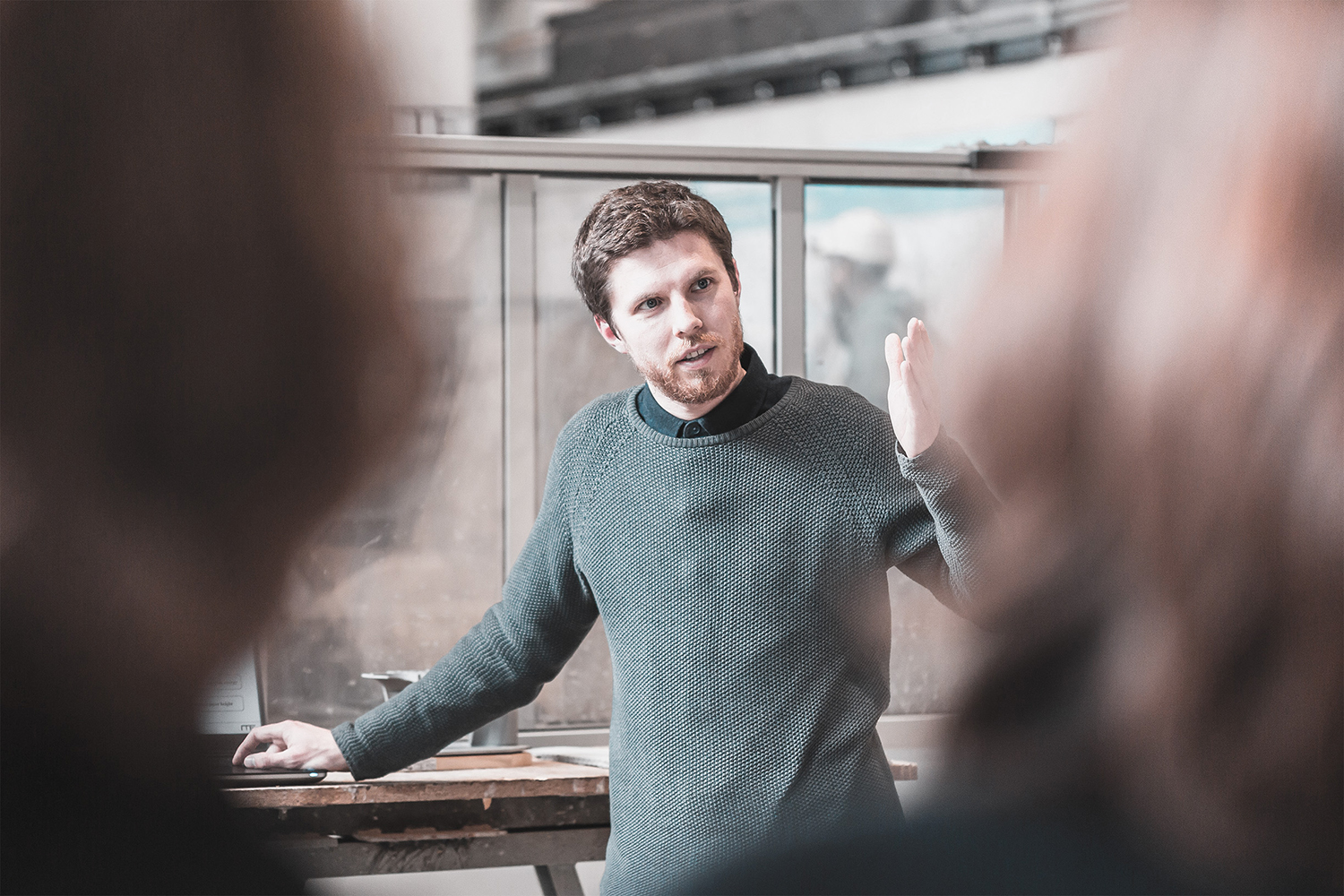
“Earth is a versatile material that is available everywhere,” says Joschua Gosslar. Picture credits: Tjark Spille
You recently completed your craft training “Clay construction specialist” at the Dachverband Lehm – as an architect?
The program mainly aims at further training craftspeople, such as masons and carpenters. However, architects and building engineers can participate as well. Lately, the training has been more and more booked out. The subject is becoming increasingly important in the building industry, however, there have not been many specialists thus far who are well informed about it. The training has a duration of one and a half months and is unique in Europe.
I have learned a lot about the old techniques there: How do I characterize the earth and how can I examine whether it is generally suitable for my technique? There are very simple, sensory ways of testing this. It is about smelling, feeling, seeing. For the falling ball test, for example, you shape a ball of a certain size, compress it with your hands and let it fall down to see how it comes apart when hitting the surface. The tests also give information about the measure of shrinkage or the binding force, meaning how cohesive the earth is. Is there a part of humus? Does it contain chalk? And what is the grain of the material like?
How did you become interested in this building material?
I was already very interested in this topic during my studies because it is a versatile material that is available everywhere. It fits perfectly into our discussion about sustainability and Cradle to Cradle (circular economy). Earth is a hundred percent reversible. You can shape it, dissolve the shape, and make something completely different. The construction materials of a building that are made out of earth can be reused at the end of the utilization phase in a new form, in a new building or given back to the soil.
Through the clay community you learn a lot. Many support each other on construction sites. I, myself, worked on construction sites for some time and constructed buildings ranging from a small visitors’ center to a large-scale high rack warehouse.
What are the advantages of earth?
Earth can absorb moisture and release it again when it gets too dry. With earth you will not have mold issues since the material is able to absorb, store and release moisture. This has a positive impact on the indoor climate. For a long time, clay had an image problem, but a lot is currently changing in that regard as it hardly causes any CO2 emissions. I see many answers in clay that fit perfectly into our recent debates.
Robotic fabrication of components from rammed earth. Video: Jonathan Schwarz/TU Braunschweig
Where does earth come from?
Earth as a building material is available in many parts of the world. We do not have to build an additional infrastructure. However, from a building practice and financial point of view it is currently easier to acquire earth from the industry instead of using local pit clay since it requires an increased effort due to admission procedures. There are only a few larger companies that offer classified clay material. In the future, however, we should take advantage of the benefits of local availability and work with pit clay as we have done in the past. In this way, we can further reduce CO2 emissions caused by transportation and take advantage of the benefits of using local resources. In our research project with GOLEHM, we are examining how to process local pit clay and use it for the robotic manufacturing of rammed earth.
The Institute of Structural Design has been doing research on additive manufacturing with earth for a while. Is the material suitable for 3D printing?
Generally, earth can be printed with a 3D printer. You can process the material in a dry, earth-moist, plastic or almost liquid state. For the extrusion process, for example, the moisture content in the material has to be quite high in order to be able to pump it. Afterwards, however, the clay has to dry again. So in this case, we have to consider shrinkage caused by the drying of water in the pasty material. Generally, you can say: The higher the moisture content of the material the higher the degree of shrinkage.
Rammed earth, on the other hand, is processed in a very dry state. Its moisture amounts to less than ten percent, similarly to soil in a garden when broken up. The clay does not contain a lot of water so that the material has a lower degree of shrinkage in the end. The permissible maximum degree of shrinkage for rammed earth is at 0.5 percent. Therefore, rammed earth is well-suited for additive robotic manufacturing, where material and production process constitute one entity. Through the automated production process, the currently quite expensive way of construction will be more cost-efficient in the future as formworks are omitted and consistent, reliable material constants are achieved. Moreover, it is possible to react to local conditions, such as the local material, via digital control of all process components.
3D printing with soil materials has its challenges, but also many benefits, such as a tremendously increased freedom of form and the omission of formwork. This makes it possible, for example, to optimize building elements statically or building-physically through the form since the 3D printer does not care whether it prints right angles or curves. We ultimately have a large savings potential regarding material usage as well as increased efficiency.
How is rammed earth held together?
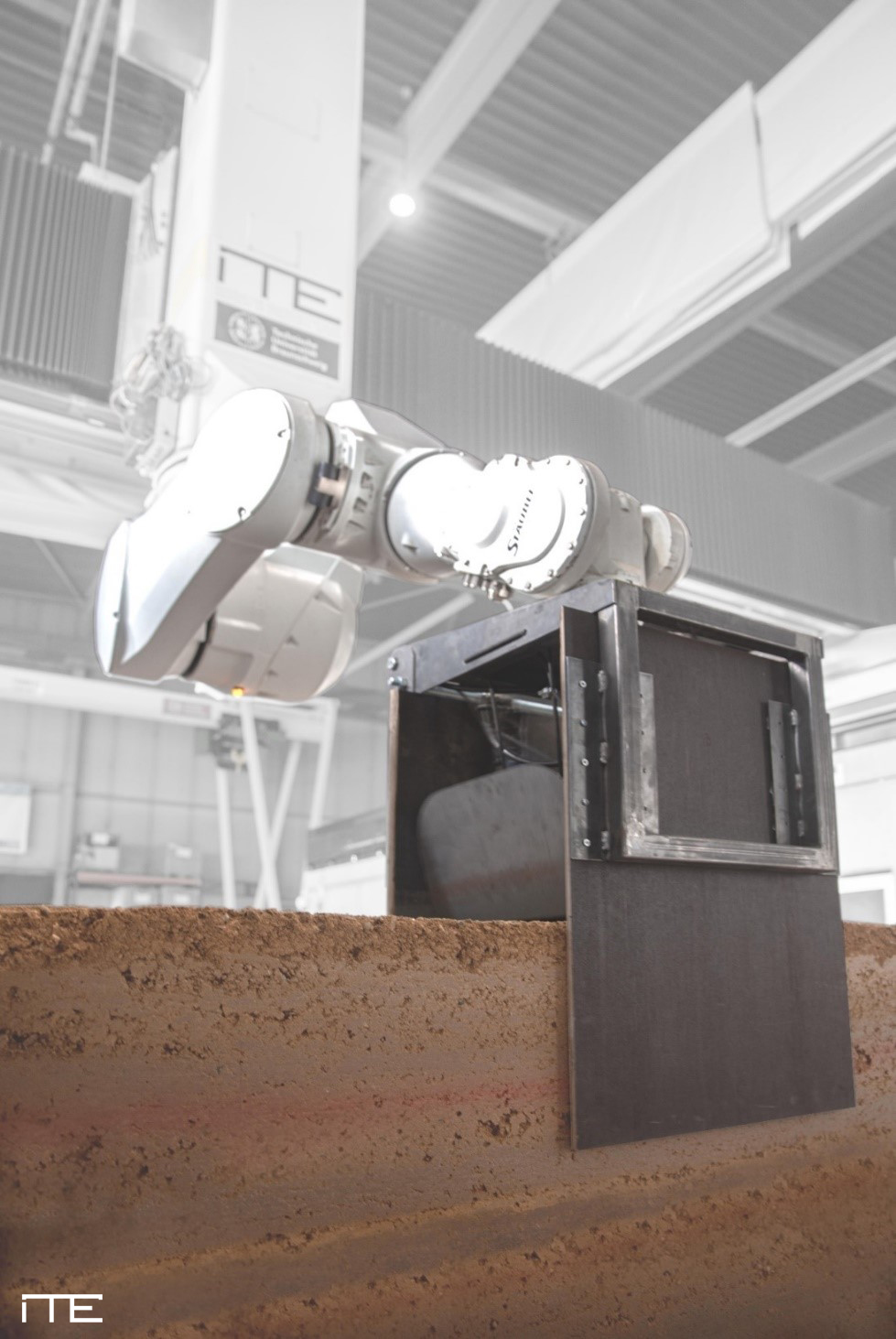
Active formwork mounted to robot during construction process. Picture credits: Joschua Gosslar/TU Braunschweig
When building with rammed earth nowadays, we either work with prefabricated elements that are assembled on the construction site or the whole wall is being fully encased bit by bit. The earth-moist clay is added in layers into the formwork and compressed with hand-guided, mostly pneumatic tampers. Formwork is, therefore, still necessary, in the same way as when building with concrete. It is, however, slightly costlier since it has to resist higher ramming pressure during compression. It is our goal to reduce the formwork effort to an absolute minimum through an actively guided sliding formwork.
Normally, the formwork is this massive because layers of approx. ten centimeters are compressed to seven centimeters. This requires a certain impact energy that sufficiently compresses the entire layer. When we reduce the height of a layer, for example to three centimeters, we also need less energy for compression. Thereby, we can reduce the stiffness of the formwork as well as its size and, eventually, the weight of the entire system.
Are you going to impart your knowledge on earth to the students?
In the summer semester we organized a clay construction workshop. The students learned to lay unfired clay bricks, apply a multi-layer clay plaster, and build a rammed earth wall. Additionally, planning pioneers who currently deal with the material provided theorical input. You also need to have held the material in your own hands in order to not have a false impression of it. We wanted to include first foundations in teaching to sensitize architects to working with natural, local materials already during their studies. Building on this, we also offer teaching content on digital manufacturing with clay in seminars and Kompaktentwürfen.
Thank you very much.