How to simulate cabin noise Noise research for new aircraft concepts with better acoustic properties
As nice as flying is, noise in the cabin can trigger stress and cause fatigue. In various research projects, researchers at Technische Universität Braunschweig are developing methods to predict and control cabin noise. To do this, they first create a so-called vibroacoustic model that represents the structural and acoustic properties of an aircraft. For this purpose, components along the sound transmission path that influence cabin noise are identified. These are mapped based on their material properties in order to obtain a cabin noise model that is as accurate as possible.
The main causes of cabin noise are the airflow around the aircraft and turbine or propeller noise. The vibrations thus generated are transmitted through the outer skin and insulation to the inner lining. The inner lining begins to vibrate and thus radiates sound into the cabin.
How the noise “spreads out” can be simulated and calculated with the models created. The researchers at the Institute for Acoustics and the Institute of Dynamics and Vibrations at TU Braunschweig can thus make predictions about the noise in the cabin. The following image shows such a prediction for an electrically powered propeller aircraft. It is easy to see that loud noises occur in the vicinity of the propeller.
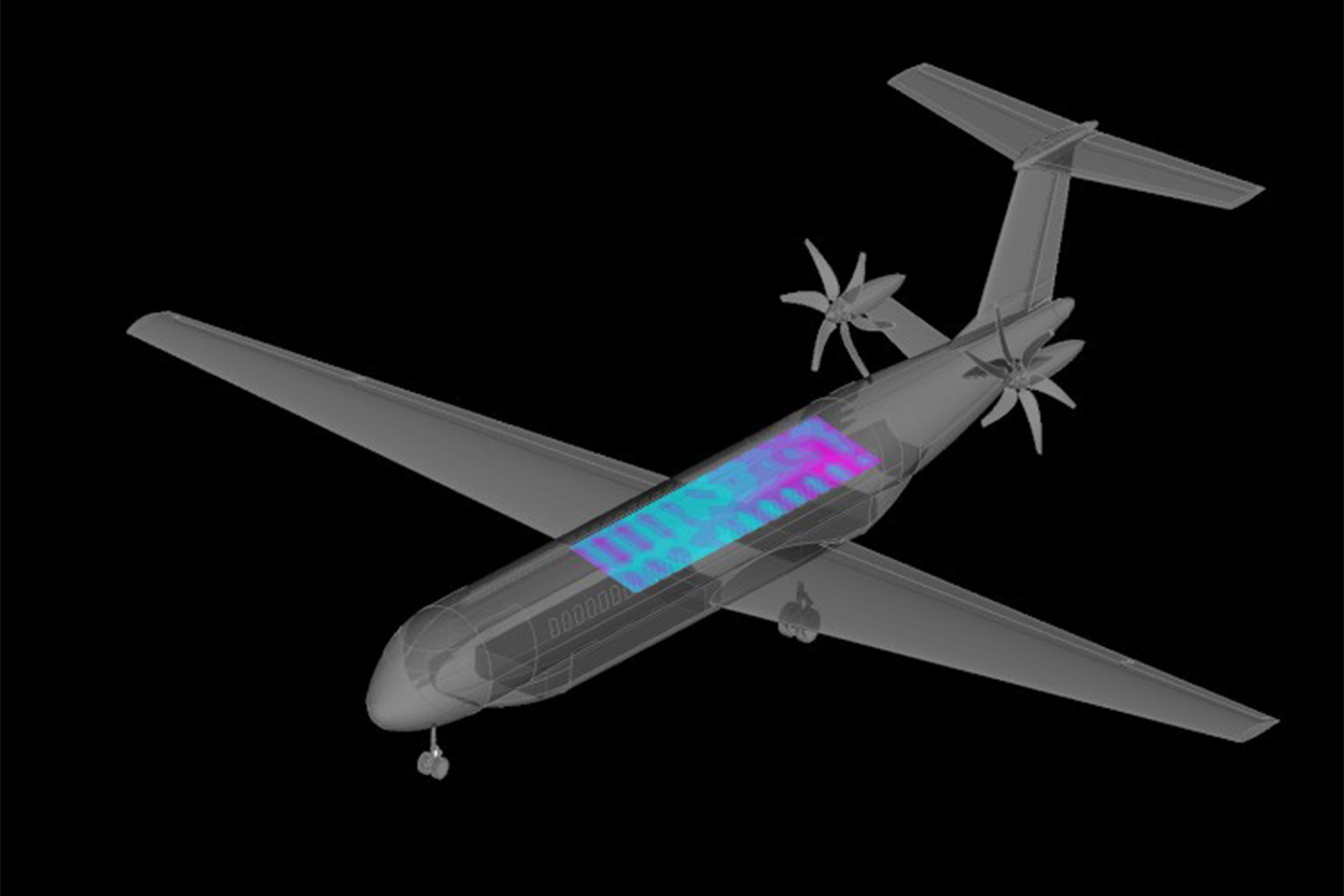
Representation of cabin noise at seat height for an aircraft configuration from the Sustainable and Energy Efficient Aviation (SE2A) cluster of excellence. Photo credit: SE2A
What it can be used for
The simulations can help test different aircraft concepts and new designs. This means that acoustic properties can be taken into account early in the development process. Modern simulation tools enable a better understanding of complex systems and an analysis of the underlying relationships. Models can be used to identify various influencing factors and improve their interactions.
Two fundamental problems complicate an accurate prediction of cabin noise. On the one hand, the structures of the cabin, especially the aircraft fuselage, must be defined very precisely, which makes the simulation very time-consuming. On the other hand, many influencing variables are not completely known in advance. Material parameters of the fuselage vary from aircraft to aircraft and the turbulent boundary layer, one of the dominant noise sources, depends on the current flight conditions, which vary stochastically.
“Quantifying uncertainty”
The researchers’ approaches to solving the problem include methods of high-performance computing in order to be able to break down the noise-causing vibrations of the fuselage with high precision. In addition, the “quantification of uncertainty” plays an important role. This involves describing incomplete or strongly fluctuating initial data and estimating their influence on the overall result. In this way, scattering of real geometries and flow conditions can be described mathematically. This ultimately enables robust designs that allow for low noise pollution under many real-world conditions.
Text: Yannik Hüpel, Sabine Langer and Ulrich Römer