Flying through turbulence undisturbed Dr André Bauknecht heads the Junior Research Group "Flow Physics of Load Reduction" in the Cluster of Excellence SE²A
Less weight, fuel consumption and emissions, more comfort for passengers: Efficient active load reduction systems have the potential to make flying more sustainable and comfortable in the future. The Junior Research Group (JRG) “Flow Physics of Load Reduction” in the Cluster of Excellence SE²A – Sustainable and Energy-Efficient Aviation – at TU Braunschweig is investigating how this can be achieved. The junior research group deals with the reduction of dynamically occurring loads on the wings of commercial aircraft caused by gusts or flight manoeuvres. An interview with JRG leader Dr André Bauknecht.
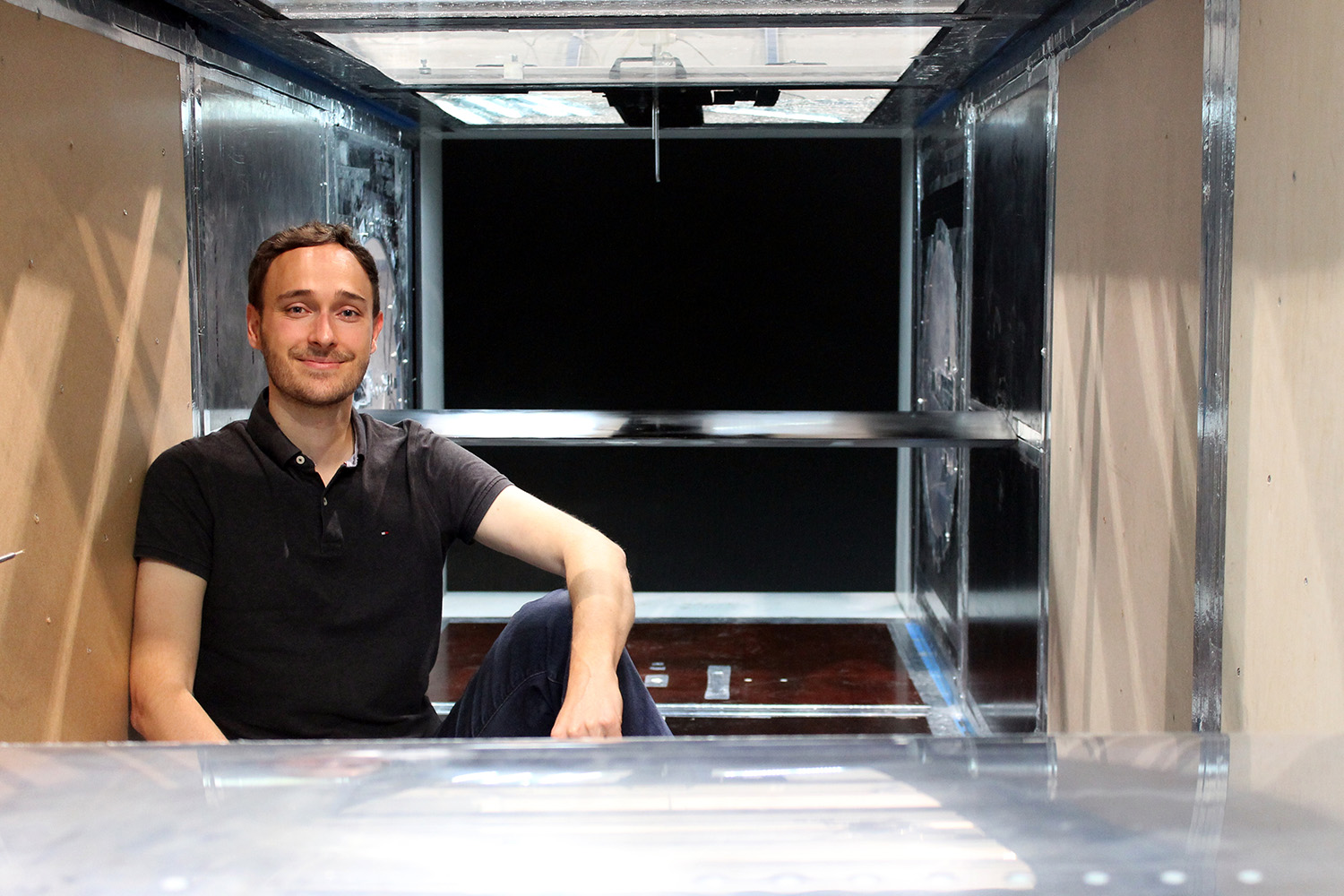
Junior research group leader Dr André Bauknecht in the wind tunnel. In the foreground is the wing with active blow-out, in the background a second profile with which dynamic gusts can be generated. Photo: Salvatore Asaro/ISM
Mr Bauknecht, your Junior Research Group is researching active load reduction. What is behind this?
When an aircraft flies through a gust – colloquially known as “turbulence” – not only the passengers are jolted, but also the flexible wings. These are indeed designed to withstand these loads. But this also makes them heavier than they would have to be without these gust-induced loads. In aviation, weight always means additional fuel consumption and thus emissions. So we try to counteract the loads with suitable measures so that the wing no longer has to withstand them and can be built lighter. One of these measures is active load reduction: by means of an actuator, i.e. a control instrument such as a flap or a targeted discharge of compressed air, a load is caused that is directed in the opposite direction to the gust, so that the gusts balance each other out as much as possible and the aircraft can fly through the gusts undisturbed.
Is the topic of gust load reduction new or has it been occupying aviation research for some time?
Approaches to gust load reduction have been around since the 1950s, but they only arrived in commercial aircraft more recently. Up to now, the existing control flaps have been used almost exclusively as actuators. However, these flaps are not necessarily designed to generate a change in lift for gust load reduction within one to two tenths of a second. Their distribution and subdivision on the wing is also not optimal.
We are taking a slightly different approach in the junior research group and are investigating fluidic actuators. With these, compressed air is blown out at suitable points on the wing to specifically influence the lift. In this way, we hope to be able to react quickly and efficiently to dynamic load changes and thus achieve significant weight and emission savings on the aircraft. In addition, such a system can increase passenger comfort.
What is the Junior Research Group investigating specifically?
At the beginning, we compared different actuator concepts and examined them under the flight conditions relevant to us on simplified wing segments. We then specifically improved the most suitable candidates so that they have the greatest possible influence on lift, but at the same time do not significantly reduce the aerodynamic quality of the wing. We have developed a good understanding of how these actuators behave under constant and time-varying blow-out and can study their interaction with gusts both experimentally and on the computer. This data also feeds into other disciplines within the Cluster of Excellence SE²A, for example in aircraft pre-design to study the effects on the whole aircraft.
Wind tunnel examination of a wing with active air blow-out at the trailing edge. Here, the wing is mounted vertically on a force balance and the airflow is coming from the left. (Text on the photo, from top left: wind tunnel, PIV cameras, wing model, airflow). Photo: Salvatore Asaro/ISM
What investigations and trials are coming up next?
We are in the process of integrating the most promising actuator systems into a future-proof aircraft configuration. This will allow us to quantify the load reduction potential of our new actuators and thus make statements about their feasibility. For this purpose, we will also investigate the mutual interaction with other active systems on the wing, for example an exhaust system for laminar retention further forward on the wing. In a final wind tunnel test, we also want to implement a complete gust load reduction system, including gust generation, gust detection, control and actuation. This demonstration of the performance of the entire system is an essential step towards installing such a system in a real aircraft.
Simulations or experiments – which typical “tools” are used?
On the one hand, we use flow simulation on the computer, on the other hand experimental tests with demonstrators in the wind tunnel. From both sources we receive large data sets that we have to simplify for further use in other SE²A research groups. We develop simplified data models – so-called reduced-order models – that approximate these large data sets, but with significantly reduced computational and memory requirements. Our simulations are mainly based on transient, i.e. time-resolved RANS simulations, in which the Navier-Stokes equations, i.e. the fundamental equations of fluid mechanics, are used to predict the flow field. In addition, typical engineering problems such as the design and optimisation of the actuator geometry and its integration into a realistic wing are also addressed here.
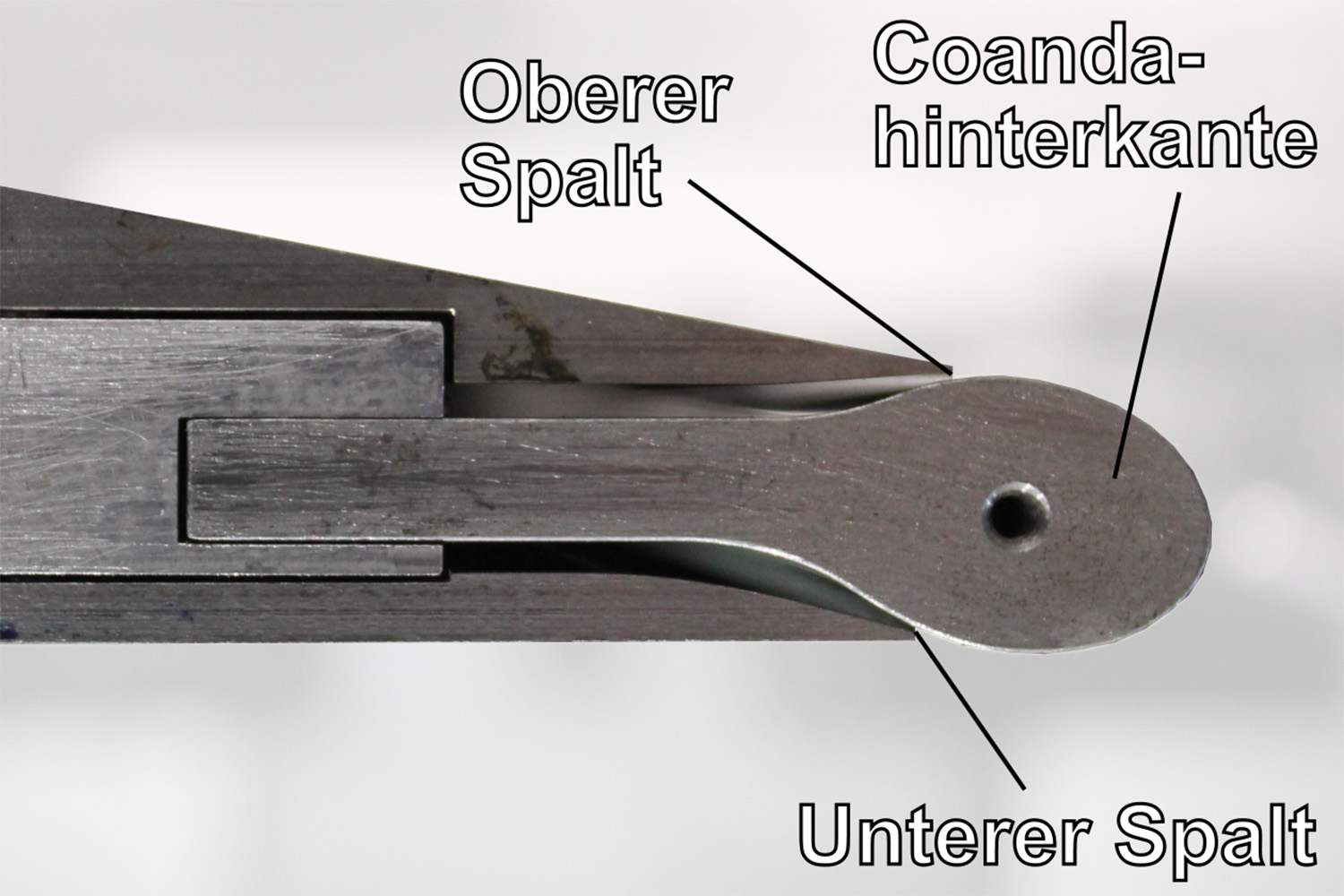
Construction of a trailing edge of a wing with air blow-out on both sides for gust load reduction. (Text on the photo from top left: upper gap, Coanda trailing edge, lower gap). Photo: Salvatore Asaro/ISM
Wind tunnel tests are essential for your research?
That’s right, with our wind tunnel tests we want to validate the simulation results on the one hand. On the other hand, the real implementation of the actuation concepts enables us to demonstrate the applicability on representative wing geometries and to implement control strategies. For this purpose, we even generate our own gusts in the wind tunnel, measure them with a probe and then specifically control our blow-out in such a way that the loads on the wing remain as low as possible.
What relevance does this topic have for the aviation of the future – especially with regard to reducing the climate impact of aircraft?
In future aircraft, emissions can be reduced through sustainably produced synthetic fuels or electric drive systems. However, they must also become significantly lighter so that energy requirements can be further reduced. Since the wing is one of the parts that is under the most strain, it also weighs a lot accordingly. Our approach to reduce this structural weight by reducing the applied loads is therefore very relevant for future aviation. The practical implementation of our results in the aircraft will probably take a few more years, but the foundations we are laying here are nevertheless important for investigating the potential of this technology.
What excites you about this research work?
For me, it is a great motivation to research topics where a clear application perspective is recognisable and which have relevance for society. The task of developing technical solutions to mitigate climate change is therefore particularly motivating. I was also very attracted by the research approach, because relatively many flow effects interact here, such as transient aerodynamics through gusts, active flow control through blow-out, detached flow fields as well as subsonic and supersonic flows. What is extraordinary is that our research takes place in the multidisciplinary environment of SE²A, where one always learns from other research directions.
From which disciplines do the researchers in your Junior Research Group come?
We are mostly aerodynamicists, but with different focuses and backgrounds, for example in the disciplines of experiments and simulations. Since we are closely linked to SE²A, we have many connections to other disciplines such as aircraft preliminary design, flight mechanics and control, and structural aircraft design. The JRG is also international – with researchers from Italy, Morocco and Germany as well as students from different countries. Since most of the group’s research took place during the pandemic, much of the collaboration has been virtual. Now, however, we can fortunately exchange ideas in person again to further advance our research.