Energy source of the future: living lab for sustainable hydrogen An interview with Professor Bernd Engel and David Sauss about research at the H2 Terminal
Moving away from fossil fuels to renewable energy: Germany wants to be carbon neutral by 2045. One of the building blocks for a successful energy transition is a functioning hydrogen infrastructure. The newly opened Hydrogen Terminal (H2 Terminal) aims to pave the way. In this interview, David Sauss, Deputy Head of the Steinbeis Innovation Centre energieplus, and Professor Bernd Engel, Head of the elenia Institute at TU Braunschweig, explain the opportunities the living lab offers for researching the H2 value chain, why ageing tests with fuel cells are important and to what extent hydrogen and batteries can stabilise the power grid.
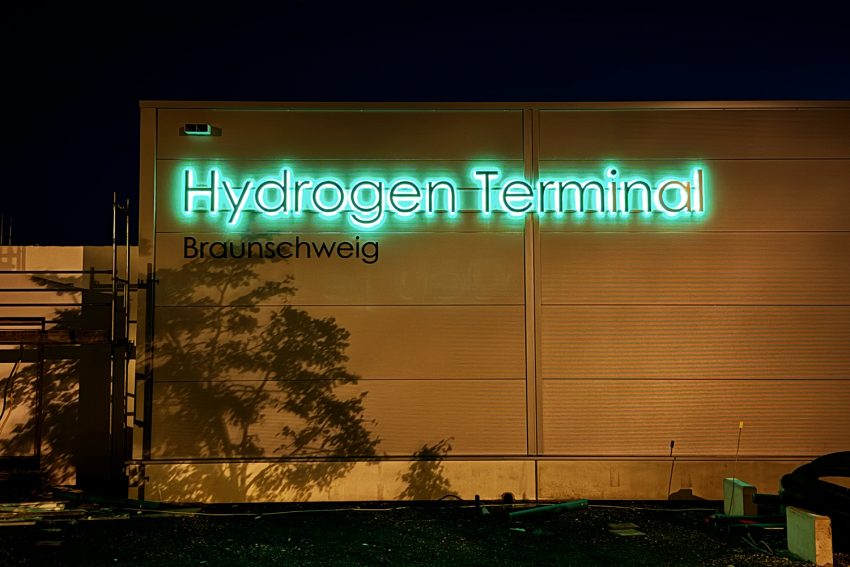
The newly opened Hydrogen Terminal at the Research Airport at night. Photo credit: David Sauss/siz energieplus
What is the H2 Terminal project?
Sauss: First of all, it’s about creating an infrastructure in order to be able to carry out hydrogen research in a concentrated way. At TU Braunschweig, hydrogen research is being conducted in so many different places, but until now there hasn’t been a place where everything can be tested together, and that’s what we wanted to create here. At the H2 Terminal, the institutes have the opportunity to experiment, and not just on a laboratory scale. Where else do researchers have the opportunity to operate an electrolyser of this size themselves, to run load curves, to study what happens when we take electricity away? We are bringing together all the different disciplines working on hydrogen at TU in this large living lab. The H2 Terminal is also useful for teaching purposes. It is important to train not only specialists, but also generalists, who bring knowledge from different areas and thus have a view of the whole. The H2 Terminal is a very good place to learn, because you can see the connections between the different sub-areas.
Engel: Another important aspect of the H2 Terminal is that we will be able to conduct megawatt-scale research into how electrolysers and the associated batteries could stabilise the power grid in the future.
Why is this necessary?
Engel: In Germany, all conventional power plants will soon be shut down and completely replaced by renewable energies. There are already times when we generate more than 100 per cent of the electricity we need from renewable sources such as wind power and photovoltaics. To avoid wasting this energy surplus, it can be useful to convert it into hydrogen using an electrolyser. This can be used where previously only fossil solutions were available, such as in steel production in Salzgitter. The energy surplus can also be stored using hydrogen. There are times when wind power and photovoltaic systems do not supply enough electricity. This is particularly the case in winter, when the so-called “cold dark period” occurs in Germany. With the help of H2-ready gas turbine power plants, the hydrogen can then be converted back into electricity and used.
Incidentally, batteries are not suitable for this, as they can only be used for short-term storage for a day or two. But batteries do have their advantages. They can react much more quickly than electrolysers, which is important for stabilising the grid in a highly dynamic way. That’s why we want to use the H2 Terminal to study how the interaction between batteries and electrolysers works best to stabilise the grid.
Sauss: Exactly, in order to be able to test all this, we have purchased an AEM electrolyser in the megawatt range, the heart of our H2 Terminal, so to speak.
What makes this electrolyser special?
Sauss: Our electrolyser allows us to use a relatively new electrolysis process. Until now, alkaline electrolysers have been used. However, these take a long time to start up and are therefore unsuitable for buffering renewable energy. The second most common process, PEM electrolysis, starts up quickly and can therefore respond quickly to fluctuations in renewable electricity production. However, it is very expensive, mainly because of the precious metals used. AEM (anion exchange membrane) electrolysis is a combination of the two processes mentioned above. In contrast to alkaline electrolysis, only a slightly alkaline lye is used here, i.e. 1 per cent instead of 20 per cent. This is much better for the environment. It also uses virtually no precious metals compared to PEM electrolysis. Our electrolyser is also made up of many small units, called stacks, that work individually. This gives us the flexibility of not having to run the electrolyser at 100 per cent power all the time, but only activating some of the stacks. And if a stack breaks down, you can just replace it and don’t have to take the whole electrolyser apart.
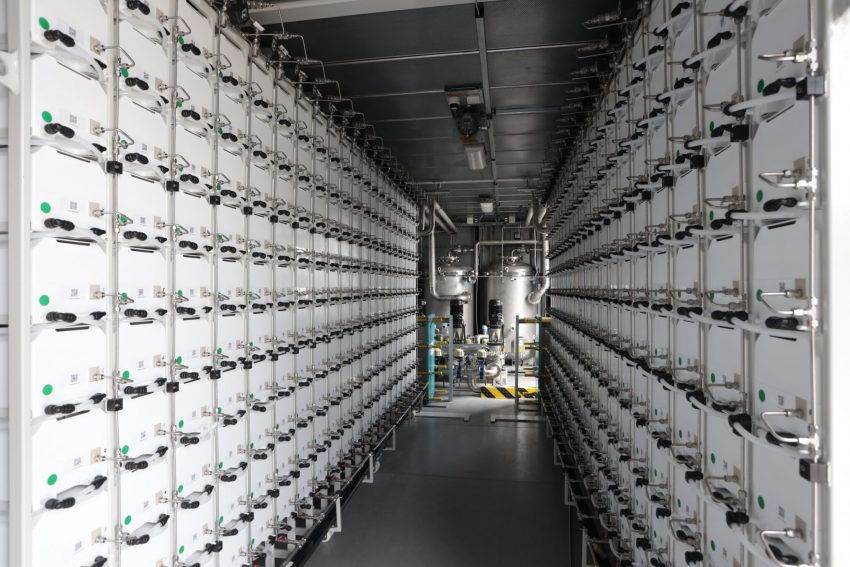
The heart of the system: a megawatt-scale AEM electrolyser. Photo credit: Sascha Gramann/siz energieplus
Another special feature is that we are buying our electrolyser from a company that is planning to move to automated production for its electrolysers. Until now, all electrolysers worldwide have been manufactured by hand in a labour-intensive process. The AEM electrolyser could offer further cost benefits through automated production. Incidentally, it is rare for a research facility to be able to test such a powerful electrolyser with a new electrolysis process as a prototype. To ensure that the electrolyser would be available in time for the opening, we ordered it three years ago and started building the infrastructure around it.
What does this infrastructure look like?
Sauss: Firstly, it was important for us to use the heat or waste heat generated during the electrolysis process. If it remains unused, the electrolyser only has an efficiency of 60 percent. But if we can extract another 30 per cent of the heat, we can increase the efficiency to over 90 per cent, which is very good. To do this, we need a heat pump, which we have developed in a long process with a company. It raises the temperature level. The heat then reaches the new Fraunhofer ZESS building via a local heating pipeline, where it can be used. If the heat pump works well, we will no longer need recoolers for the electrolysis.
And what about the use of hydrogen?
Sauss: After the hydrogen is produced in our AEM electrolyser, it first goes into a steel tank. It holds about one day’s production. From there, the hydrogen is transported via pipelines to three different applications. One of these is the mobility sector, with a hydrogen refuelling station for heavy goods vehicles, which we have built for research purposes on the site of the H2 Terminal in the immediate vicinity of the electrolyser. To be able to operate them, the hydrogen must first be compressed using a filling station compressor. Of course, we also need suitable vehicles for refuelling. We are fortunate that a haulage company in Wolfsburg has converted two lorries to fuel cells. They will then be refueled at our site, but we will also be able to test all the logistics involved in the conversion.
Another hydrogen pipeline leads to the neighbouring Automotive Research Centre Niedersachsen (NFF) with a small branch to the new Fraunhofer Centre for Energy Storage and Systems ZESS. The NFF will soon be home to the world’s largest metal hydride storage facility. Hydrogen will be stored, withdrawn and researched by the Institute of Internal Combustion Engines and Fuel Cells (IVB). The NFF will also use the hydrogen to supply its own engine test benches. The fact that the NFF will receive our green hydrogen via pipeline in the future also contributes to the decarbonisation and reduction of the carbon footprint of TU Braunschweig.
A third use path leads to the building next to the electrolyser at the H2 Terminal. This is where the Institute of Technical Chemistry carries out various tests with hydrogen, fuel cells and electrolysers.
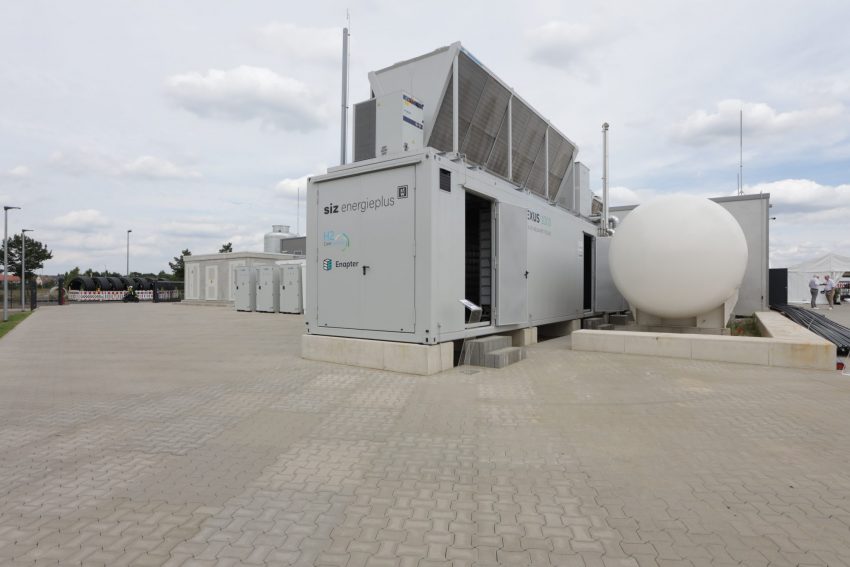
A complex H2 infrastructure is created around the electrolyser within a very short time. Photo credit: Sascha Gramann/siz energieplus
What exactly is tested there?
Sauss: On the one hand, we have fuel cell test benches there. The fuel cell uses the hydrogen to generate heat and electricity. How well and efficiently it does this depends heavily on the ambient conditions. This is why ageing tests are carried out on the fuel cell test benches, in which we test on a small scale how chemistry, materiality and membrane coating can best be combined to increase the lifetime and efficiency of the fuel cells. We are also testing the production of hydrogen by pyrolysis of hydrocarbon-containing starting materials in order to further develop the feeding of plastic pellets, for example. And then we want to test other electrolysis processes in the building.
Why is this necessary?
Sauss: The different electrolysis processes all react very differently and also have different advantages and disadvantages. It is therefore important to compare these electrolysis processes. We also have a PEM electrolyser as a test stand. And in the next few months we will also have a zinc interstage electrolyser as a prototype. A battery is already built into this new process. You feed electricity into it, but you don’t get hydrogen immediately – it takes four to eight hours.
What energy sources are actually used to produce hydrogen at the H2 Terminal?
Engel: The hydrogen comes from 100 per cent renewable energy sources.
Sauss: Exactly, that’s why we have covered every possible area of the H2 Terminal with photovoltaic panels. However, this is not nearly enough to operate such an electrolyser. For the time being, we buy the rest from the local supplier. It is important that the green electricity is certified, because only then can the hydrogen be labelled as green hydrogen. Construction of a three-megawatt photovoltaic plant on the airport site is due to start at the end of the year, which will cover our needs. We have already done all the groundwork. The cables have already been laid and a feed-in field is planned in our medium-voltage grid.
And where does the water for hydrogen production come from?
Sauss: A normal tap water connection is actually sufficient. However, the tap water has to be filtered, demineralised and passed through an ion exchanger so that we can operate the electrolyser with the purest water.
How does the elenia Institute support the project?
Engel: We are responsible for the overall coordination of the TU institutes in the construction and supervision of the H2 Terminal. A total of seven institutes and the Division 3 Facilities Management team are involved. We are also responsible for the grid integration and grid stabilisation mentioned above, as well as energy management. In other words, how can we run the whole hydrogen terminal economically if we generate the energy from renewable sources that sometimes produce too much and sometimes too little.
What was the biggest challenge in setting up the H2 Terminal?
Engel: The main challenge was to build this living lab in a relatively short space of time. The technical complexity of the project goes far beyond the construction of a private home and consists of so many different components, some of which are unique in the world, that have to work together.
Sauss: Yes, that’s right, and we wanted to build our infrastructure not only for current research projects, but also for many different projects that will come up in the future. And it’s not easy to plan such a large infrastructure without really knowing what projects the institutes will be doing there in the future.
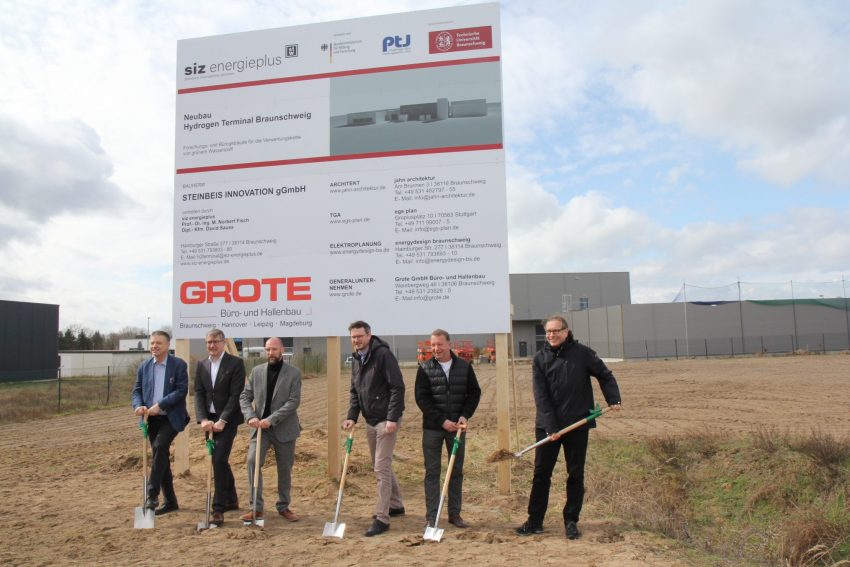
On 23 March 2023, the ground-breaking ceremony for the construction of the now opened living lab took place: from left to right: Prof. Bernd Engel (elenia, TU Braunschweig), Gerold Leppa (Head of Economic Affairs, City of Braunschweig), David Sauss (siz energieplus), Maximilian Bohr (BS Energy), Oliver Mocker (Grote), Thorsten Markgräfe (Head of Facilities Management, TU Braunschweig). Photo credit: David Sauss/siz energieplus
Could the concept of such an energy centre not only be used for research, but also for the future supply of industrial areas or settlements?
Sauss: Absolutely, such a supply is also applicable to areas outside of research.
Engel: There are many different concepts being developed in this direction. A centralised hydrogen infrastructure is already emerging, with large 100 megawatt electrolysers connected to the main water network and large consumers. There will also be decentralised hydrogen networks to supply industrial and residential areas.
Thank you very much!