Aircraft Construction and Maintenance: Automated with Mobile Robots Hi-Digit-Pro 4.0: Automated assembly of landing flap modules
Aircraft operation is responsible for the lion’s share of emissions and resource consumption in aviation. To make flying more environmentally friendly and climate-friendly in the future, not only the aircraft but also production, maintenance and repair should be optimized. In the Hi-Digit-Pro 4.0 project, researchers from TU Braunschweig and DLR have developed a new concept that combines mobile robot units with lightweight assembly devices. How it works exactly, we will explain here. Includes a video!
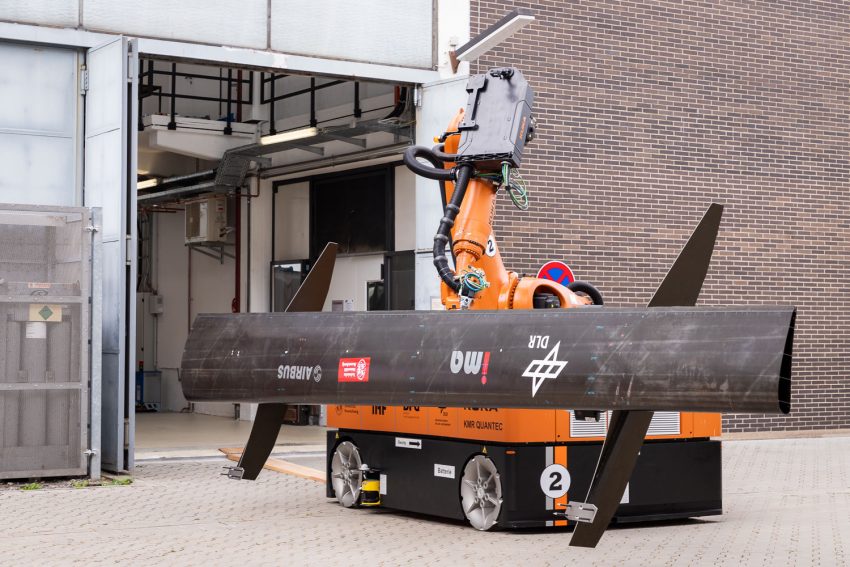
Hi-Digit-Pro 4.0 is a joint project of the Institute of Mechanics and Adaptronics at TU Braunschweig and the Institute of Composite Structures and Adaptive Systems at DLR. Picture credit: Markus Hörster/TU Braunschweig
Many structural components in aircraft are thin-walled and made of lightweight carbon fiber reinforced polymer (CFRP) composites. If such structures are also particularly long and slim, as is the case with landing flaps on wings, for example, their inherent rigidity is often low. As a result, the components already deform strongly under their own weight during the assembly processes without additional measures. Highly rigid steel fixtures provide a remedy. They fix the components in their intended shape and allow trouble-free assembly. Due to their high weight, however, these fixtures cannot be moved by mobile robots, but require much more complex and specialized processes.
In the Hi-Digit-Pro 4.0 research project, a new assembly concept has been developed that enables lightweight assembly fixtures with so-called actuators to compensate for tolerance deviations and ensure precise positioning. The new assembly fixture is so light that it can be used on mobile robots. This guarantees the greatest possible flexibility of the production process. This enables automated assembly of large structures of low rigidity such as the landing flap modules, which consist of the landing flap as well as the connecting elements towards the wing box.
New assembly process: how it works exactly
First, the mobile robot transports the flap module to the assembly line. Once there, it moves to the aircraft wing and roughly aligns the flap module with the assembly points on the wing. A 3D camera system captures the position of the wing and reference points from all components to be assembled. Six actuators integrated into the assembly fixture then compensate for gravitational effects and manufacturing tolerances. The robot arm mounts the flap module on the wing of the aircraft. Finally, the mobile robot uncouples the assembly fixture and is ready for the next assembly task.
The student initiative Wissenschaftliche Arbeitsgemeinschaft für Studio- und Senderfragen (ags) of the TU Braunschweig has visually documented the assembly process in this video:
Future perspective: assembly with machine learning
In the future, the assembly process is set to become even faster and more efficient. Real-time capable robot control using neural networks is planned. An algorithm based on machine learning will provide information on the assemblability and set the assembly parameters on its own. The geometry will be measured, the data will be transmitted to the algorithm, and the constructive compensation element will be adjusted so that the assembly of the flap module can take place immediately and without delay.