3D printing with concrete: “Pushing the limits of kinematics” Robot-controlled production in unique facility
It sounds extraordinary: building with concrete without formwork boards, scaffolding and trowels! What if this work were done by a robot and a milling machine? Scientists at Technische Universität Braunschweig are researching 3D concrete printing in the Digital Building Fabrication Laboratory (DBFL) at the Institute of Structural Design (ITE). I met Hendrik Lindemann, who is very familiar with the facility.
“Can we really talk about 3D concrete printing here?” I ask Hendrik Lindemann, who is currently writing his doctoral thesis on generative manufacturing at TU Braunschweig. “What is often understood as 3D printing is, strictly speaking, only 2.5D printing. Our robotic arm can spray the concrete from all directions, so it’s 3D.” While a conventional 3D printer applies material layer by layer, the system at DFBL can control the concrete nozzle via a total of nine axes.
The process is called “Shotcrete 3D Printing”, SC3DP for short, and was developed at ITE in collaboration with the Institute of Building Materials, Concrete Construction and Fire Safety (iBMB) and the Institute of Machine Tools and Production Technology (IWF, both TU Braunschweig) as well as the Institute of Assembly Technology (MATCH) at Leibniz University Hannover.
The system is based on a CNC milling machine with five degrees of freedom from the marble industry company OMAG. This is joined by a six-axis robot arm, a Stäubli TX200, on a three-axis kinematic system. This combination is unique. With these two machining heads, which can be oriented freely in space, the DBFL allows both additive construction in the concrete spraying process and subtractive finishing, for example by sawing or milling to produce joints accurate to the millimetre.
Shuttering before pouring concrete, which everyone knows from the construction site, seems to be a thing of the past. The advantages are obvious: more cost-effective, sustainable production of individual components with high precision and short changeover times.
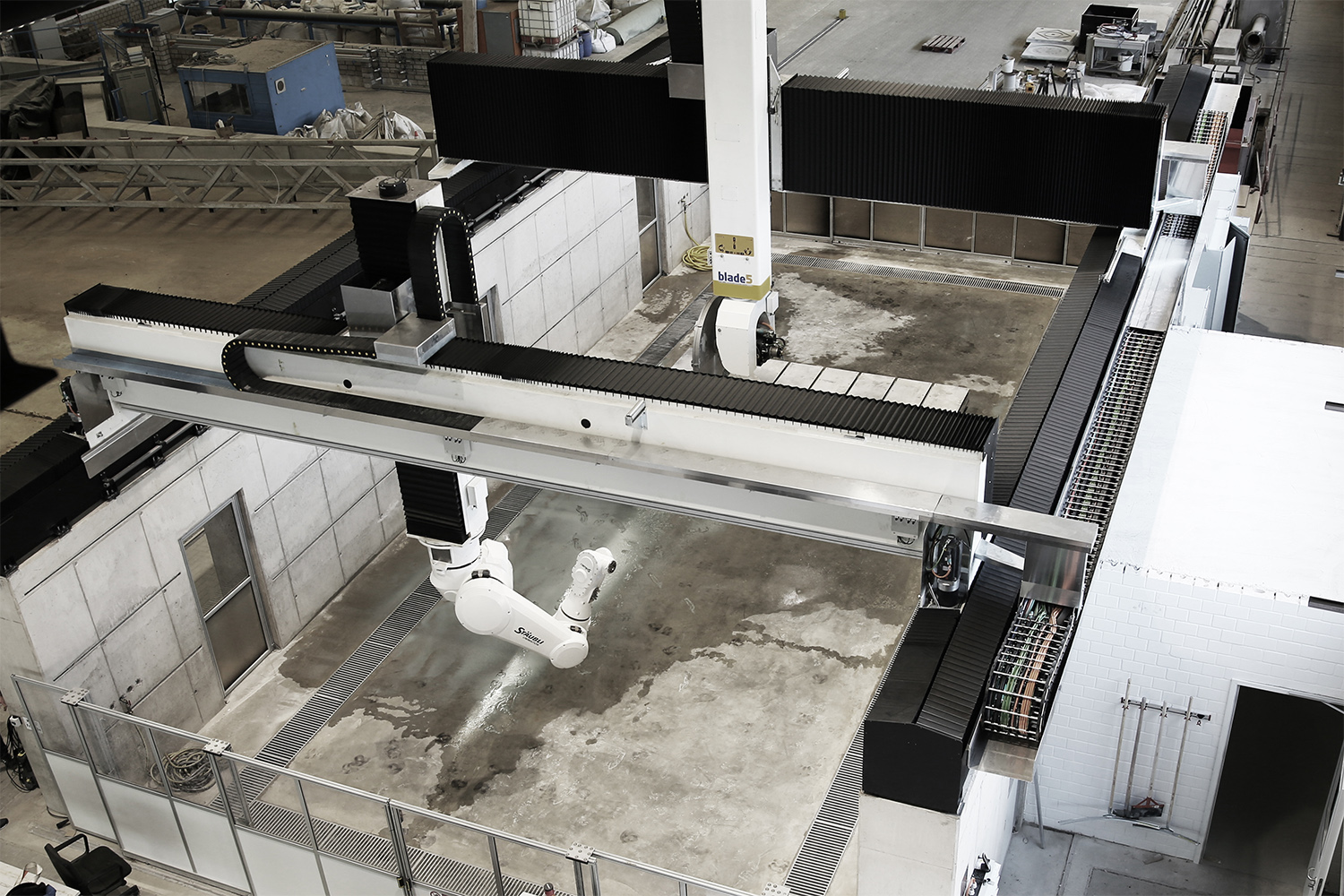
View of the DBFL from above: the two axis paths of the two portals for the CNC milling machine and robot arm are clearly visible, photo credit: Justus Hoven/TU Braunschweig
Not yet fully automated
As I stand in front of the DBFL, I look down on a facility over 16 metres long and over seven metres wide, clad in high concrete walls on the two long sides and protected by transparent gates on the short ones. Inside are two so-called portals that support the processing heads and give them even more possibilities for movement.
To the right is a control room from which I can overlook the work area. There is hardly any dust and no dried concrete residue. It certainly won’t always be like this. “The cleaning is still very time-consuming. A lot of people work to make sure that the facility is clean again after each test,” says Lindemann. I ask if there are any other practical challenges. We go behind the facility, where everything needed to mix the concrete is stored: a special concrete mix as bagged goods, a compulsory mixer, a pump. “We are still mixing the concrete manually at the moment. When the mixture is ready to be stirred, three student assistants shovel the mortar into the pump. It’s hard work and definitely an area where automation still needs to be developed.”
This is how the robot is programmed
Before a manufacturing process, Lindemann creates a line model on the computer based on the shape of the object. The lines represent the movements of the robot head, which applies concrete at a distance of 20 centimetres from the object to be manufactured. “The special thing is that the robot’s journey can be simulated” — Lindemann shows me the virtual workspace with the robot travelling along the previously drawn lines.
He then sets many parameters in another visual programming software, for example for the air pressure or the amount of drying accelerator that is fed into the nozzle. The parameter values and their dependencies on each other seem to be the trickiest thing about concrete printing. “Parametric design” is what Lindemann and his colleagues call it, which they explore in many experiments in order to be able to produce complicated shapes, a desired stiffness or surface. This is because the research facility is one that was not built for one specific purpose. The researchers can try out many processes before they become specialised for industrial use. “We have often pushed the limits of the kinematics of the six-axis robot,” Lindemann recalls, for example when building overhangs.
Production adaptable at any time
Shotcrete has been known as a process for about 100 years and is used in tunnel rehabilitation, in the stabilisation of rock faces or in the construction of climbing facilities. The work of the nozzle operator is certified and is a physically demanding activity. Companies offer the technique as a special service. Good, so robots will do that in the future? Better to have it explained to me one more time. The Braunschweig researchers do not see “Shotcrete 3D Printing” as a substitute for the conventional approach. They are combining the best methods—tried and tested technology with automation and precision—to create a new process.
“This is only possible if we question previous manufacturing processes,” says Lindemann. While usually a design would be available at the beginning, for which a suitable production method would be determined, with SC3DP the approach would be exactly the opposite. Here, production can be adapted in such a way that the required design can be implemented. “The idea behind this is that production itself becomes a design factor.”
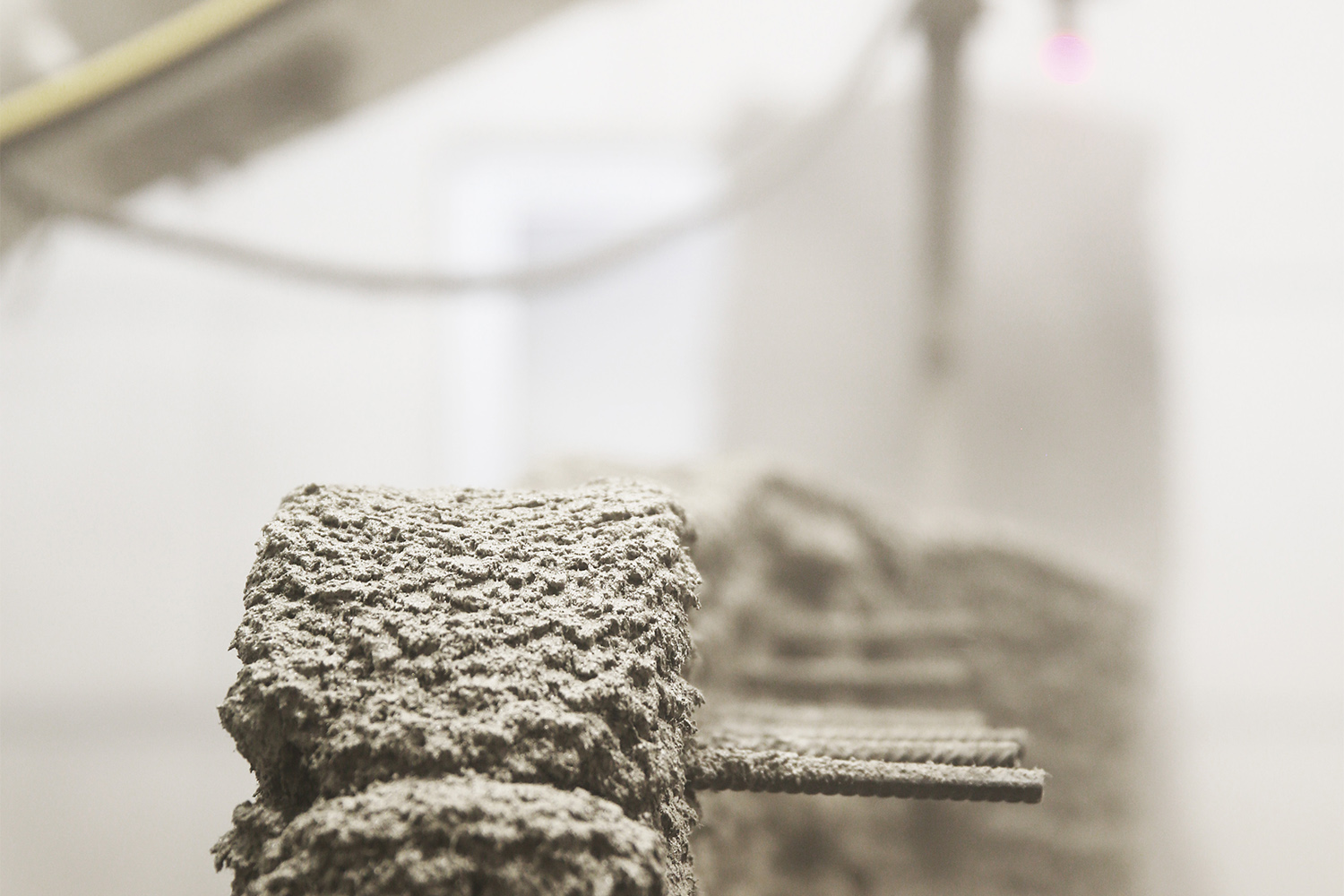
Peaks with concrete: detail of an additive construction; photo credit: Jan Leonard Goldenbaum/TU Braunschweig
New challenges
With the construction of the production hall, ITE has taken a first big step in this direction. The researchers have plenty of plans for the future. For example, a laser measurement could help to regulate the amount of concrete delivered at the nozzle in case of unevenness on the object. ITE is working on this together with colleagues from IWF at TU Braunschweig and MATCH at Leibniz University Hannover.
Until now, one type of concrete has been fed into a production process. But what if in places a firmer or finer material would be more suitable? And while we are on the subject of materials: What additives, what mixing ratios are optimal? The DBFL team would also like to research this together with teams from the iBMB at TU Braunschweig and the Institute of Non-Metallic Materials at TU Clausthal. The desire for more effective surface finishing is also particularly obvious: when is the best time to smooth the shotcrete – in the earth-moist state, half-dried or fully dried? Which milling disk is best suited for this?
What still takes up a lot of time is the object-related production of reinforcement, i.e. reinforcing the concrete with steel to ensure a high load-bearing capacity. I ask whether this could also be automated. Lindemann then shows me something that has just been delivered and adds a whole new function to the facility: an industrial welder. It looks like the term “3D concrete printing” will soon hardly suffice.

The robotic arm, equipped with a camera and laser measuring unit to compensate for unevenness during spiking; photo credit: Jan Leonard Goldenbaum/TU Braunschweig