When the Seabed Turns to Dough Virtual laboratory for offshore wind turbines simulates soil liquefactio
Around 1,500 wind turbines are spinning in the German North and Baltic Seas. And there are even more to come. By 2030, the capacity of offshore wind turbines is expected to increase from about 7.5 gigawatts to 20 gigawatts and 40 gigawatts in 2040. Floating wind turbines could also play a role in this. In order to optimally adapt the platforms to the conditions underwater, researchers in the international joint project NuLIMAS are investigating the interaction between waves, floating bodies and the seabed. With the help of computer models, they want to simulate the so-called bottom liquefaction around wind turbines. The project is coordinated by the Leichtweiß-Institute for Hydraulic Engineering and Water Resources at the Technische Universität Braunschweig.
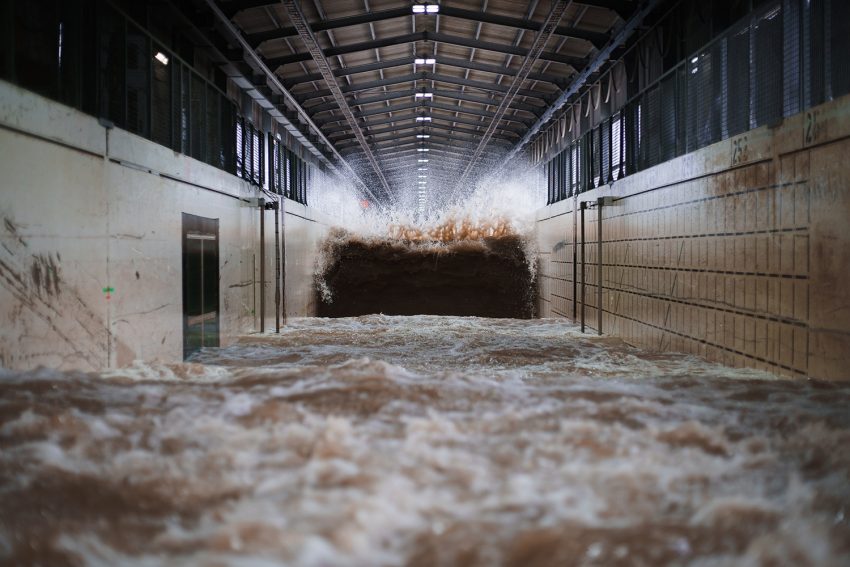
A large-scale experimental campaign is planned within the NuLIMAS project in the newly expanded Large Wave Flume at the Coastal Research Center in Hannover. Picture credit: Connor McBriarty/TU Braunschweig
Floating wind turbines could give wind energy another boost: Until now, the piles of permanently anchored offshore wind turbines could only be installed in water depths of up to 60 meters, and thus close to shore, to still be economically viable. Floating wind turbines, on the other hand, only require flexible anchoring to the bottom. This would allow wind farms to be erected far from the coast, where wind speeds are also higher.
Research into the new technology is still in its infancy. In 2017, Hywind Scotland, one of the first floating offshore wind farms with five wind turbines, was connected to the grid off the coast of Scotland. Other smaller prototypes also exist in Spain and Italy.
When the seabed turns to dough and anchor forces dwindle
One of the challenges of using floating wind turbines: How can the substructures be optimally adapted to the conditions underwater? To this end, researchers from the Leichtweiß-Institute for Hydraulic Engineering and Ocean Resources (LWI) at the Technische Universität Braunschweig, together with partners from Germany, Poland and Turkey, are investigating processes of soil liquefaction in the joint project NuLIMAS. “As coastal engineers, we have known about this phenomenon for a long time,” says Professor Nils Goseberg, head of the Department of Hydromechanics, Coastal and Ocean Engineering at LWI. “As a result, large structures, such as breakwaters, have previously sunk into the bottom during storms.” The scientists therefore want to avoid seabed liquefaction at all costs.
This could occur in floating wind turbines if the steel cables that connect the floats and gravity anchors cyclically wobble at the foundation due to strong wave action. “Certain bottoms then become like dough and can thus no longer transmit the anchor forces,” explains Professor Goseberg. In the worst case, the entire plant slides away. So the goal must be to keep the offshore wind turbine as stable as possible, Goseberg says. “The less often the wind turbine has to be shut down because of bad weather, high swells or too strong winds, the better it is for the energy yield, or the Levelized Cost of Energy, which is the price you have to pay to harvest that energy.”
Simulation in computer model and experiments in wave flume
The researchers plan to simulate this phenomenon in a computer model to develop a tool that will help planning engineers answer questions about anchor design, soil type and site selection. “With our tool, we show how the soil around an anchor of a floating offshore wind turbine liquefies and can then adapt and optimize the design of the turbine,” explains Dr. Christian Windt from LWI, who is coordinating the joint project.
The scientists are collecting initial comparative data sets through small-scale experiments with their partners in Poland, which they will then supplement with a large-scale experimental campaign in the newly expanded Large Wave Flume at the Coastal Research Center in Hannover. The large-scale model will use a patented multifunctional floating platform system from GICON as a model, which will be studied under different wave sizes and ocean currents, as well as with different bottoms. “The challenges are great: due to climate change, waves will get bigger, storms will increase. That’s where we need research to give the market the answers it needs now for the Energiewende,” Professor Goseberg said. The NuLIMAS toolbox will be publicly available once the project is complete.
Project Details:
The collaborative project “NuLIMAS – Numerical Modeling of Soil Liquefaction around Marine Structures” is funded by the ERA-NET Cofund MarTERA under the Horizon 2020 program of the European Union. Additional funding comes from the German Federal Ministry for Economic Affairs and Energy (BMWi), the Turkish Institute for Scientific and Technological Research (TÜBIKTAK) and the Polish Narodowe Centrum Badań i Rozwoju (NCBR). The total funding amounts to 1.4 million euros. The TU Braunschweig’s share of the funding is around 521,500 euros. In addition to the Leichtweiß-Institute for Hydraulic Engineering and Ocean Resources (LWI) of the TU Braunschweig, the Coastal Resarch Center (FZK), the Institute of Hydro-Engineering of Polish Academy of Sciences (IBW) as well as GICON, WIKKI and BM SUMER are involved as industrial partners.
Further information: http://nulimas.info