Building with the 3D Printer, Young Talent for the Microchip: Stephan Weil Visits TU Braunschweig Prime Minister learns about digital building fabrication and microelectronics
Buildings are part of our cultural development. New technologies are now needed to make construction more environmentally friendly, faster and more economical. Researchers at Technische Universität Braunschweig see additive manufacturing, or 3D printing, as a key digital technology for the construction of the future. On 23 October, the researchers showed Lower Saxony’s Prime Minister Stephan Weil how they, together with the Technical University of Munich, are exploring the fundamentals of 3D printing in the Collaborative Research Centre “Additive Manufacturing in Construction”. He also got a glimpse of the future of microelectronics: at TU Braunschweig, the combination of photonics and electronics, i.e. the control of electricity and light in a single microchip, is a key area of research. To this end, a new semiconductor technology is being developed at the Nitride Technology Centre NTC.
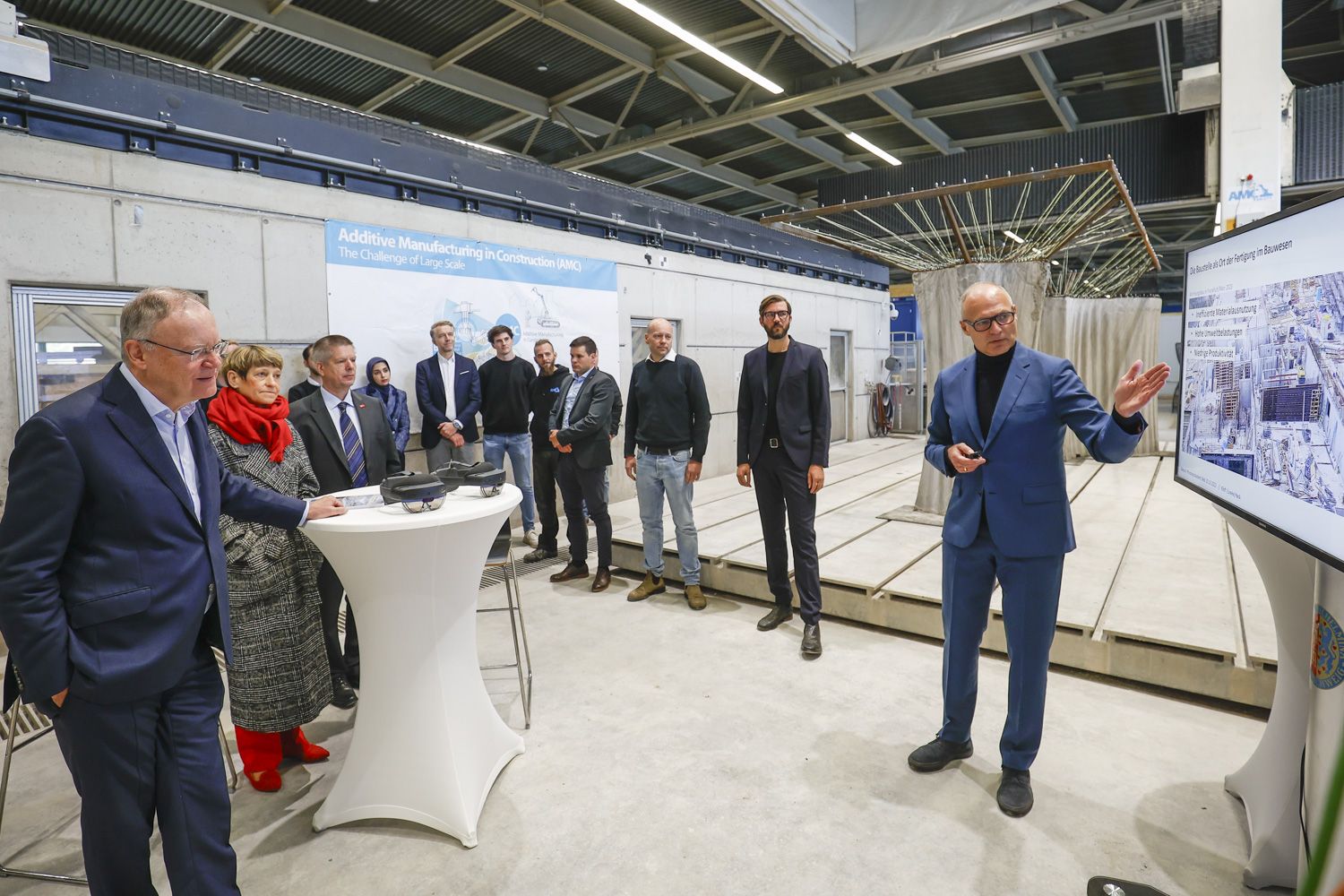
Professor Harald Kloft, head of the Institute of Structural Design (ITE) and spokesperson for the Collaborative Research Centre “Additive Manufacturing in Construction”, gives an insight into research on digital construction. Photo credit: Christian Bierwagen/TU Braunschweig
“Research from Lower Saxony is a real innovation driver, as I was able to see for myself once again today at Technische Universität Braunschweig. New technologies are being developed here that will make construction more environmentally friendly, faster and more economical – a real milestone. And research on semiconductor technologies promises advances in energy efficiency and performance,” says Stephan Weil, Minister President of Lower Saxony.
Research location for digital building fabrication
The quadrupling of the world’s population over the past 100 years has made construction a global driver of resource consumption and environmental impact. At the same time, the construction industry is suffering from stagnating productivity, and construction is becoming increasingly unaffordable for customers. While other industries, such as the automotive sector, have integrated technological developments into their production over the decades, the production of buildings on construction sites is still dominated by labour-intensive manual techniques.
This is where the researchers of the Collaborative Research Centre “Additive Manufacturing in Construction” (AMC) come in. In contrast to manual construction techniques, 3D printing builds up a component layer by layer and brings it into its three-dimensional form: there is no need for mould making, industrial pre-processing or complex adaptation processes of semi-finished products such as blanks. “At the dawn of the digital age, we have a great opportunity to use 3D printing to pave the way for a paradigm shift in construction, focusing on the value of the material rather than the labour costs of outdated construction techniques. Additive manufacturing has the potential to be a key digital construction technology to make construction more productive, environmentally friendly and affordable,” says Professor Harald Kloft, head of the Institute of Structural Design (ITE) and spokesperson for the Collaborative Research Centre. TU Braunschweig has been researching 3D printing processes for the construction industry for ten years and has established itself as a research centre for digital building fabrication.
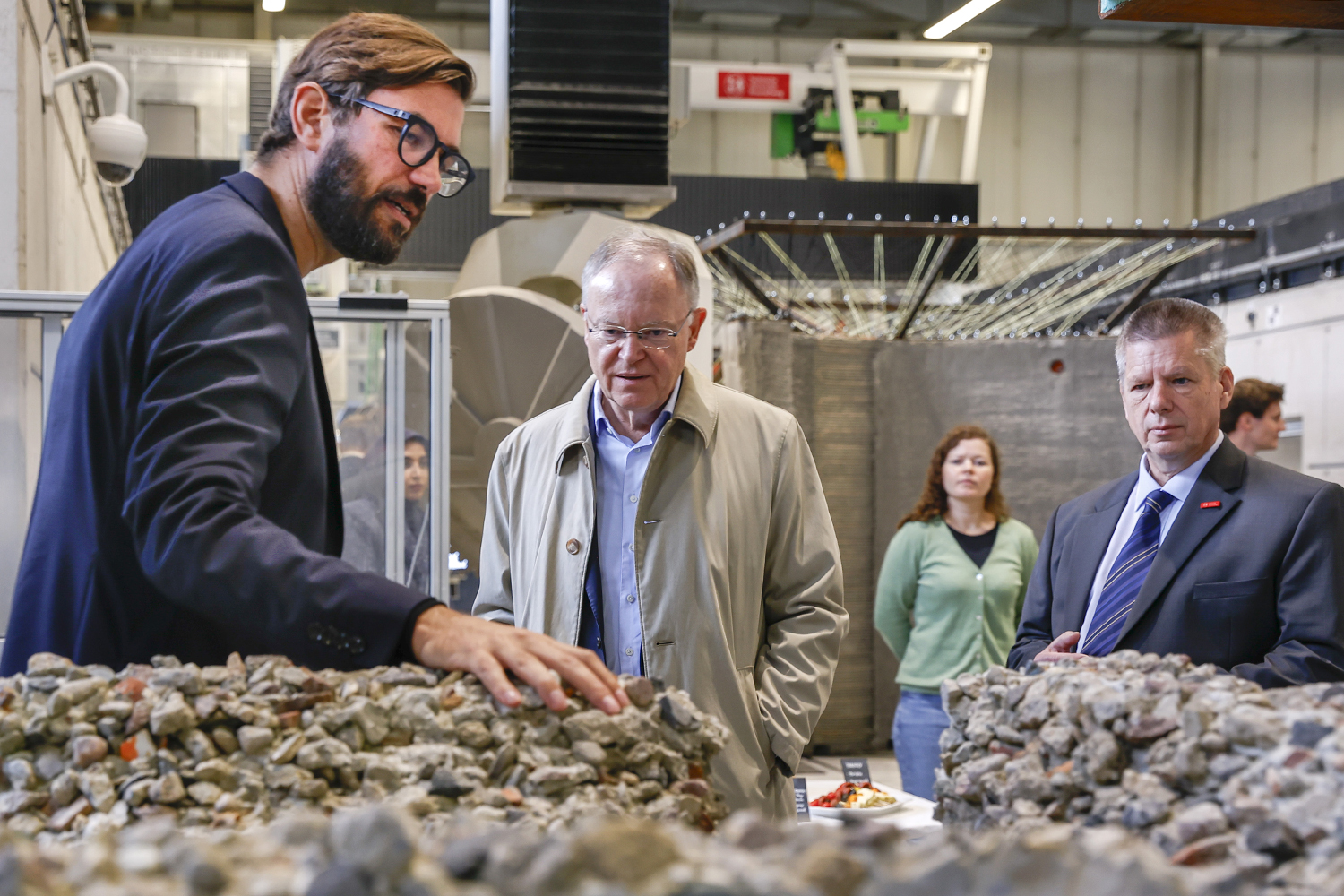
Norman Hack, Professor of Digital Construction at the Institute of Structural Design, explained to Minister President Stephan Weil and Prof. Peter Hecker, Vice President for Research and Early Career Scientists, how concrete components from existing buildings that are to be demolished can be reused. Photo credit: Christian Bierwagen/TU Braunschweig
Digital building fabrication centre: “Thinking about buildings in a whole new way”
But what does it look like in practice? Minister President Stephan Weil was given a tour of the Digital Building Fabrication Laboratory (DBFL). The large research facility, 16 metres long and nine metres wide, is a digital building fabrication centre. It includes a CNC milling machine, a six-axis robotic arm and an automated concrete mixing plant. Components – such as walls, columns, ceilings and even bridges – are printed on a 1:1 scale and the interactions between material, process and design are studied: “3D printing allows us to think about buildings in a completely new way. More resource-efficient, less polluting, more efficient and with new design freedom for architecture,” says Norman Hack, Professor of Digital Construction at ITE.
Concrete, steel, clay
Using the DBFL, the researchers are printing not only concrete but also steel and clay, building up the material in layers, spraying it with a robot arm as in the Shotcrete 3D printing process, or injecting strands of material into a carrier medium to create filigree structures. “The interaction of material and 3D printing process is of fundamental importance for the quality of the printed components,” says Dirk Lowke, Professor at the Centre for Building Materials at the TU Munich. The researchers also showed how concrete components from existing buildings that are to be demolished can be reused. Here, real digital process chains help to extract concrete components from existing buildings and reuse them as “second components”. Research is also being carried out into the use of precision formwork made from 100 per cent recyclable industrial wax. The wax can be re-melted and offers completely new forms of formwork.
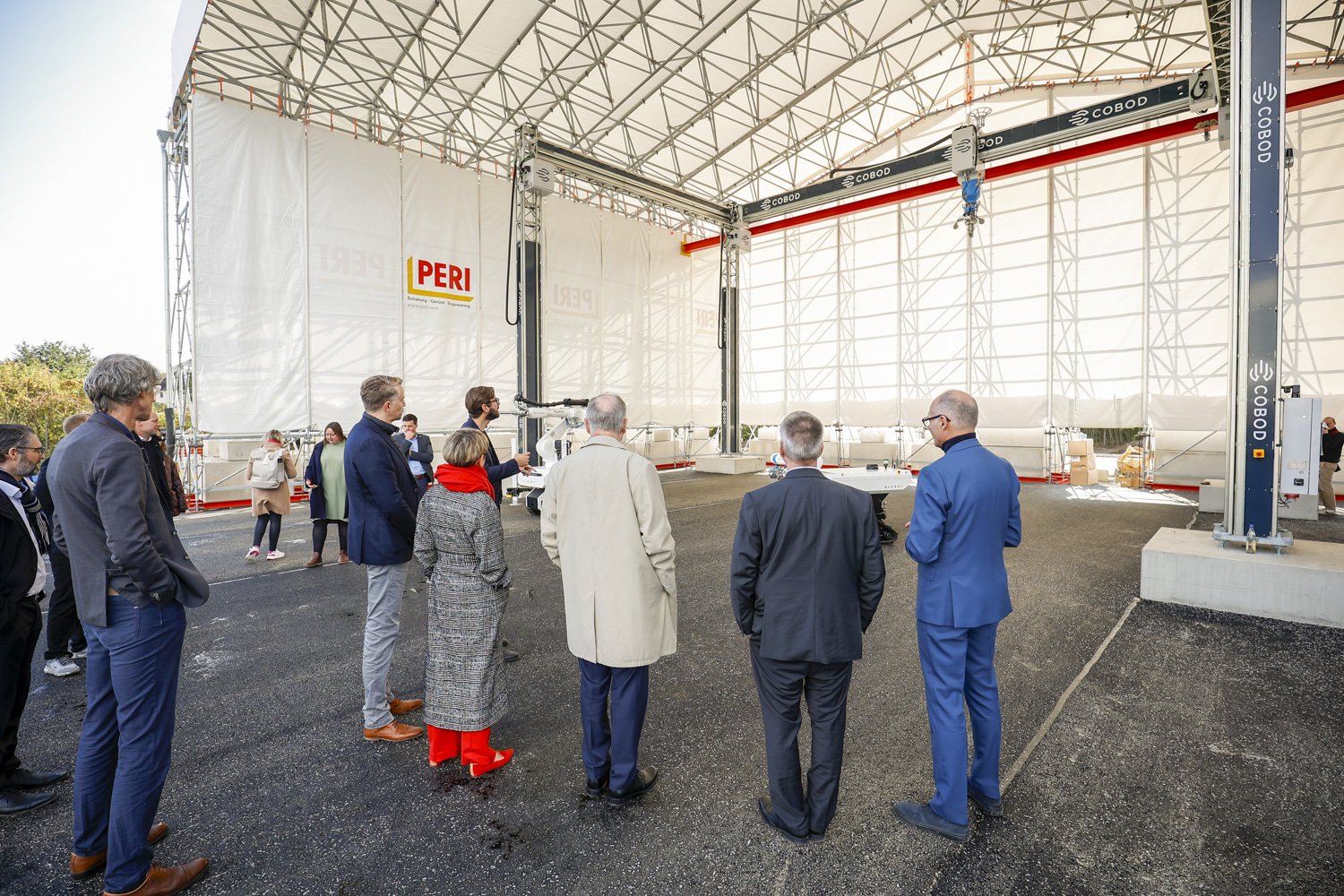
A visit to the digital construction site currently under construction at TU Braunschweig’s East Campus. Photo credit: Christian Bierwagen/TU Braunschweig
“The achievements of the DFG Collaborative Research Centre TRR 277 ‘Additive Manufacturing in Construction’ are groundbreaking for the construction industry and society. The work of this powerful research area will fundamentally revolutionise the construction industry,” summarises TU Braunschweig President Angela Ittel. “The research group is also an excellent example of how successful and enriching cross-university and interdisciplinary cooperation can be. We plan to expand this cooperation in the future. Together with the Technical University of Munich, for example, we have launched a draft for a joint cluster of excellence that will explore further research into new building technologies and their integration into the economy and society”.
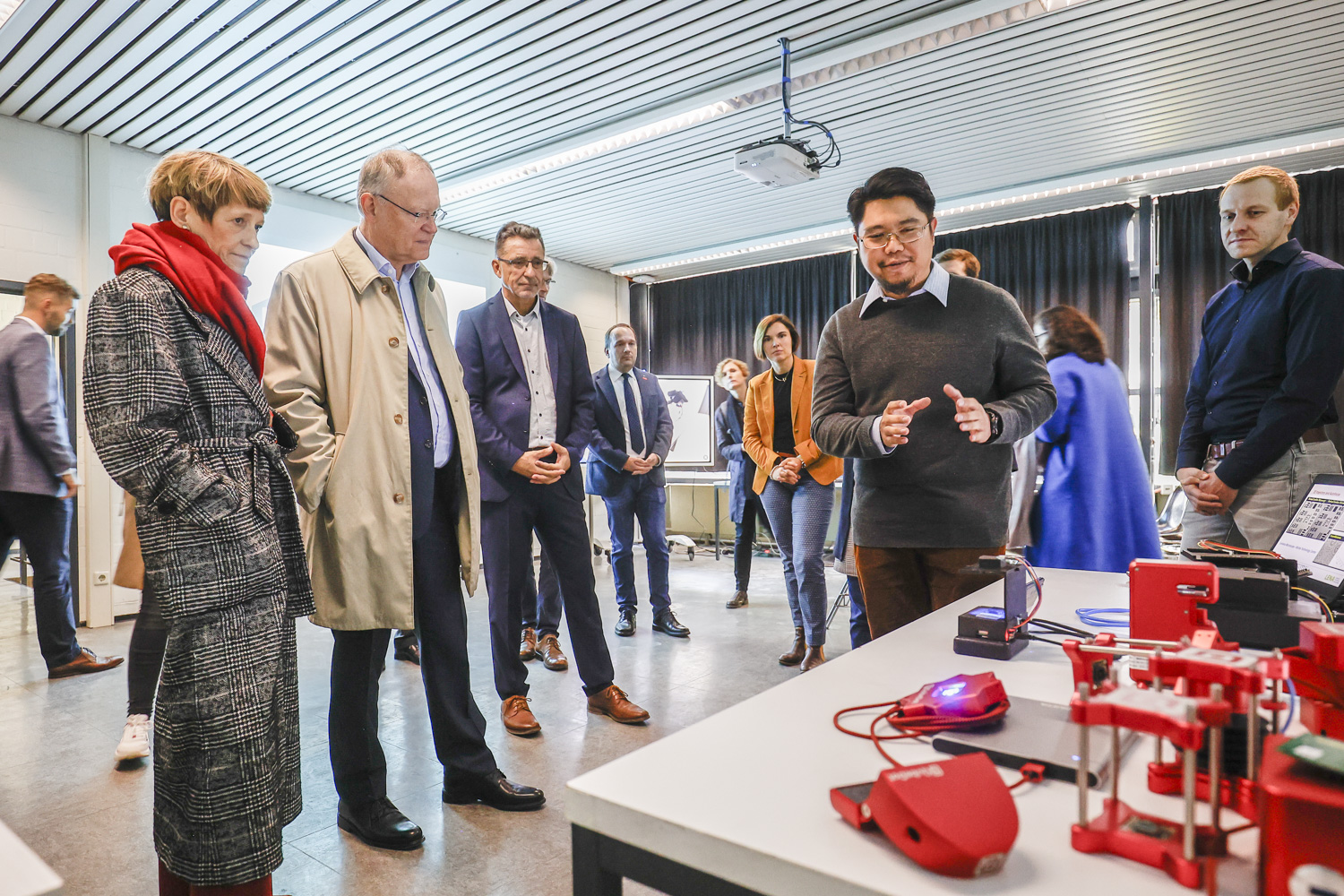
Another area of research at TU Braunschweig is gallium nitride technology. The Nitride Technology Centre (NTC), which was presented by Professor Andreas Waag, head of the Institute of Semiconductor Technology, and other researchers, will bring all the threads together. Photo credit: Christian Bierwagen/TU Braunschweig
Another stop on the tour: the Nitride Technology Centre
Another area of research at TU Braunschweig is gallium nitride technology. The Nitride Technology Centre (NTC) is where all the threads come together. Semiconductor chips that control light as well as electricity are being researched at the NTC. Optical processors are the basis for energy-efficient and powerful AI processors. Between the training of urgently needed specialists for semiconductor production and the development of quantum technologies, the Minister President was presented with a field of the future for Lower Saxony’s research and industry.
“In recent years, we have developed Braunschweig and the surrounding region into an internationally visible centre for gallium nitride research. Unlike silicon, gallium nitride can emit light and is therefore playing an increasingly important role in microelectronics. With the NTC, we are now concentrating these research activities and thus also the training of specialists in Lower Saxony – in close cooperation with regional initiatives such as Quantum Valley Lower Saxony and global players such as Intel, Infineon, ams Osram and Global Foundries,” says Professor Andreas Waag from the Institute of Semiconductor Technology at TU Braunschweig.