Aviation: The future of aviation without air friction SE²A develops laminar wings using 3D-printed suction panels
At the SE²A Cluster of Excellence for Sustainable Aviation at Technical University of Braunschweig, researchers have succeeded in making aircraft wings more aerodynamically efficient. These specially developed, 3D-printed suction panels stabilise and optimise the boundary layer – the area of airflow directly adjacent to the wing – in a targeted manner.
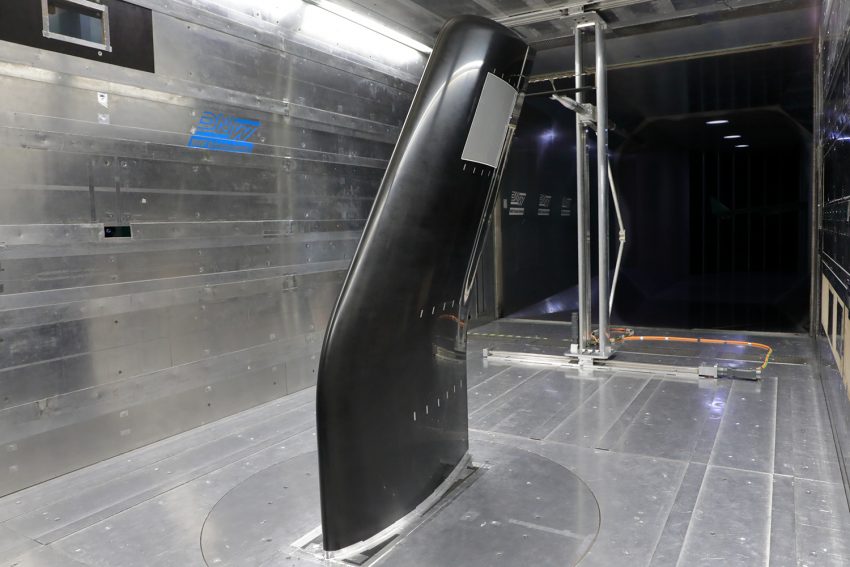
The crescent wing in the measurement section of the low-speed wind tunnel in Braunschweig. The 3D-printed suction panel, coloured grey, was installed in the upper third of the wing. Photo credit: Hendrik Traub/TU Braunschweig
The reduction of emissions and energy consumption is one of the goals of the Cluster of Excellence for Sustainable Aviation. Understanding the flow behaviour of aircraft, especially at the wings, is key to achieving this. The researchers use the low-speed wind tunnel in Braunschweig (NWB) of the German-Dutch Wind Tunnel Foundation (DNW) for experiments. This wind tunnel enables a very low degree of turbulence, so that boundary layer behaviour similar to that in free flight experiments can be simulated here.
Last year, SE²A Cluster of Excellence researchers, in cooperation with the German Aerospace Center (DLR), demonstrated the potential of 3D-printed panels for boundary layer extraction in wind tunnels. They proved that laminarisation of the boundary layer can be achieved using microperforated extraction panels produced by a 3D printer, i.e. panels with tiny holes. In this process, a small part of the boundary layer is extracted through the microperforated surface, thereby stabilising it.
In May 2025, researchers Lajos Fohlmeister and Jan Kube achieved the first successful creation of a laminar boundary layer on a 3D wing using integrated, 3D-printed extraction panels. These new suction panels enable the boundary layer on aerodynamic bodies to be modified so that the laminar-turbulent transition shifts further downstream, significantly increasing the proportion of the laminar boundary layer. The laminar boundary layer causes up to 90 per cent less air friction than the turbulent boundary layer. Air friction accounts for around half of the total drag on modern commercial aircraft. “Laminar flow control is therefore a promising way to significantly reduce the fuel consumption – and thus the emissions – of commercial aircraft,” says Jan Kube, from TU Braunschweig, who is responsible for manufacturing the 3D-printed extraction panels.
The sickle wing
A particular highlight of the new study is the 3D sickle wing, which was developed at the Institute of Fluid Mechanics in the SE²A Cluster of Excellence. “The wing’s unique sickle-shaped geometry enables us to study various aerodynamic states and, in particular, the transitions between them,” explains Lajos Fohlmeister, who led the development of the sickle wing and conducted the wind tunnel tests. The sickle wing was designed to simulate a newly designed airfoil under realistic conditions. The findings will therefore also help improve numerical methods for predicting various transition scenarios, such as the laminar-turbulent transition of the boundary layer.
Interesting for the construction of sailing boats, light aircraft and commercial aircraft
Producing the particularly fine microperforation with a diameter of less than 250 micrometres presented a challenge to the printers. Hendrik Traub comments, “Finding a suitable perforation geometry accounted for a large part of our research work. The ability to print such surfaces now enables three-dimensional curved extraction surfaces to be produced quickly and cost-effectively. This is interesting for sailing boats, light aircraft and commercial aircraft, as well as for scientific applications.”
About the project
While the concept and production of the extraction panels were developed at the Institute of Mechanics and Adaptronics (Jan Kube, Hendrik Traub, Prof. Christian Hühne, TU Braunschweig), the ongoing preliminary aerodynamic tests of the extraction panels were carried out in cooperation with the DLR Institute of Aerodynamics and Flow Technology. The sickle wing was developed and built entirely at the Institute of Fluid Mechanics (Lajos, Fohlmeister, Prof. Rolf Radespiel, TU Braunschweig). The final wind tunnel test was conducted in collaboration with the Institute of Fluid Mechanics and the Institute of Mechanics and Adaptronics at TU Braunschweig, using the low-speed wind tunnel (NWB) of the German-Dutch Wind Tunnel Foundation in Braunschweig.