Research for sustainable aviation: ‘Commitment and passion’ Interview with PhD student Michelangelo Grappadelli about SE2A
Michelangelo Grappadelli is a PhD student at the Institute of Fluid Mechanics at Technische Universität Braunschweig. He has investigated the laminar boundary layer of aircraft wings for the SE2A Cluster of Excellence for Sustainable Aviation. As a wind tunnel researcher, Grappadelli aims to find solutions for reducing the specific fuel consumption of civil transport aircraft through the use of new technologies. However, he says in an interview that for him, this is more than just research.
How did you get into research?
Even as a child, I had a passion for building things in my parents’ garage. At the age of 18, I built my first small wind tunnel. During my studies, this experimental side of me became even stronger, and it all felt very natural. During my master’s thesis, I realised that I wanted to pursue a career in aerospace research with a focus on experimental aerodynamics.
What is your SE2A project about?
During my time in the SE2A cluster, I worked on a research project that focused on wind tunnel testing of laminar boundary layer suction for aerospace applications. My work involved the design, construction and testing of two test setups: a flat plate and a 2D wing, both equipped with laminar boundary layer suction systems. The main objective was to measure the energy savings achieved by reducing drag through laminar boundary layer suction.
I believe that it has become both a personal commitment to drive forward the reduction of aircraft emissions and a deeply fascinating passion that continues to fuel me with boundless energy.
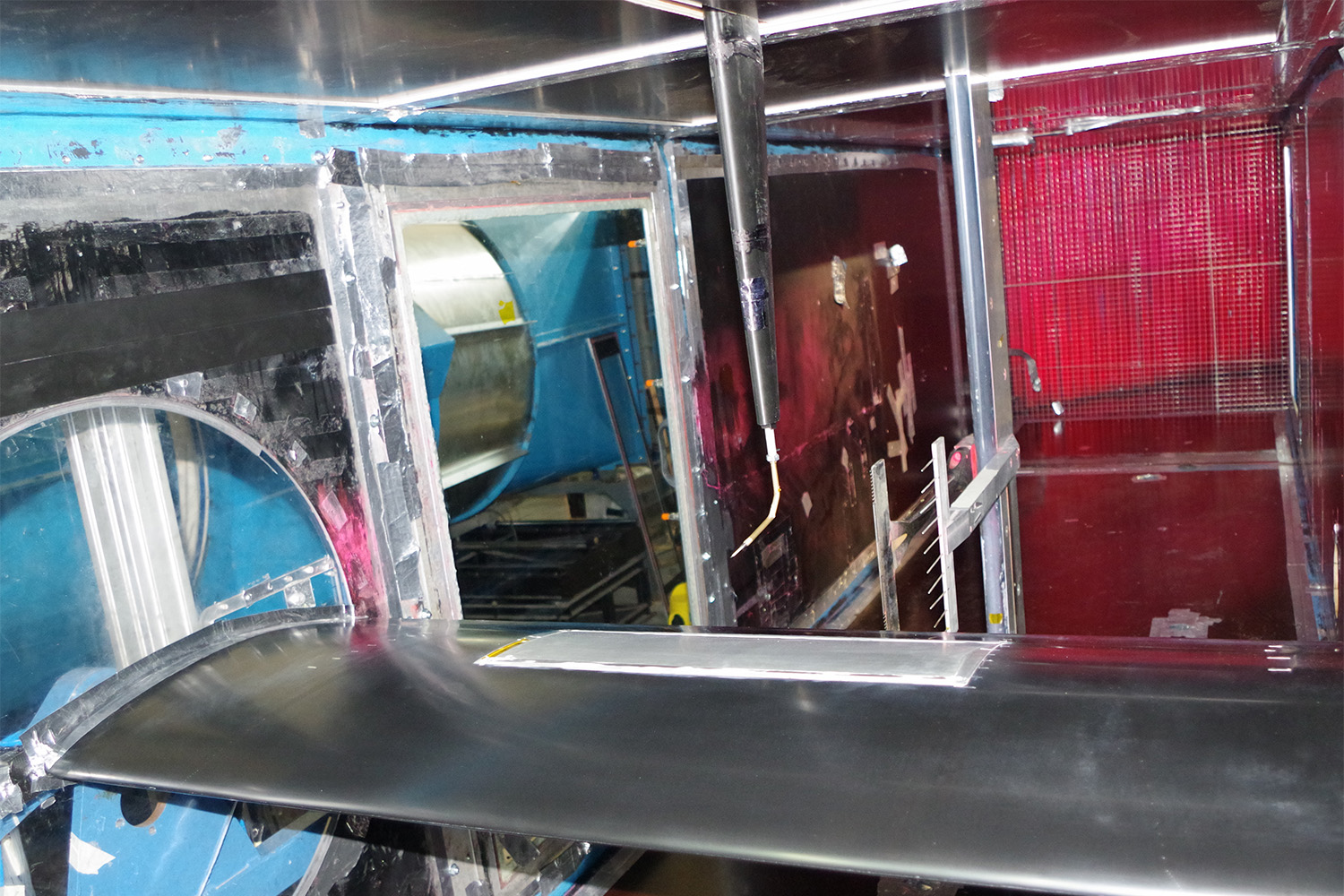
A wing in the wind tunnel. Photo credits: Michelangelo Corelli Grappadelli
How will SE2A benefit from your research?
My contributions to the SE2A cluster are mainly experimental data for calibrating and refining calculation models used in the wing design phase. These data sets increase the accuracy of simulations for future applications. For the first time, it has been demonstrated that a hybrid laminar flow control (HLFC) solution works under unfavourable pressure gradients and significantly improves the efficiency of a laminar wing section. The original design goal of a 33 percent reduction in drag was confirmed, supporting the feasibility and effectiveness of the laminar boundary layer suction technique. Methods for investigating boundary layer phenomena were also developed, such as the use of pressure measurement points through the porous skin for precise pressure measurements in the suction area, the development of a new hot-wire traverse probe on the porous skin, the construction of glass fibre surfaces with controllable heating through the skin, and suction boxes for sucking in the boundary layer with less than two percent maximum deviation along the entire suction surface.
In your opinion, what is the strength of aviation research in Braunschweig?
The strengths of research in Braunschweig lie in the presence of all the necessary research departments at TU Braunschweig – from aircraft construction and aerodynamics to engines and navigation systems – just like in a real aviation company. This constellation promotes strong scientific interaction, especially in Hermann-Blenk-Straße at Braunschweig Research Airport. In addition, Braunschweig has always been one of the most important centres for the development of aerospace, especially for aircraft and gliders.
What are your plans, what are you working on next?
I am currently working on a project that focuses on the implementation of fuel cells in aircraft. Specifically, the aim is to reduce viscous drag by supplying heat to the boundary layer, thereby reducing aerodynamic drag and improving heat dissipation, which ultimately increases the overall efficiency of the aircraft. I am confident that I will continue to conduct research in the field of aerospace, particularly in wind tunnel testing, with a focus on applications for aircraft.