Picture of the month: From engine construction to pharmaceutical application Nanoporous membranes from the Institute for Materials Science
When metallic materials are exposed to stresses such as high temperatures and tensions over a long period of time, changes occur in their microstructure. In turbine blades, these lead to potential material damage, but researchers from the Institute of Materials Science are taking advantage of precisely this mechanism. They are using it to produce nanoporous membranes made of a nickel base superalloy that could be used in pharmaceuticals. What these membranes look like under the microscope is shown in our picture of the month.
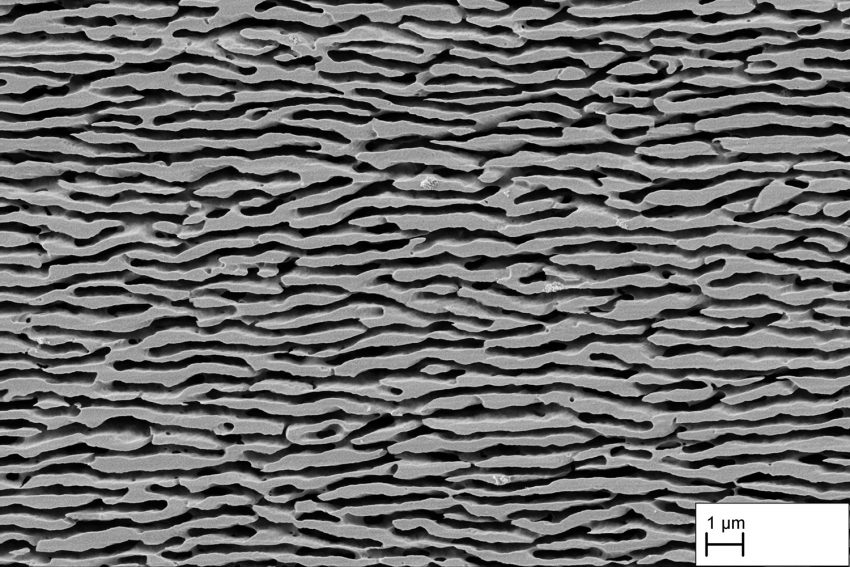
The pore size of the superalloy membrane in the picture of the month is 250 nanometres in diameter. The aim is to reduce this to 100 nanometres. Photo credit: Marius Lück/TU Braunschweig
Nickel-based superalloys are particularly resistant to material fatigue at high temperatures. This makes them a popular material in engine construction. Nevertheless, changes in the microstructure also occur here under permanent load and increasing temperature, which can potentially lead to material failure. To investigate these changes, the material is tested in creep tests. In these tests, the samples are permanently subjected to a mechanical stress at a temperature of approx. 1000 °C over a long period of time.
Possible applications in pharmacy
What serves to test material behaviour in engine construction is used by Marius Lück, a research associate at the Institute of Materials Science, to generate targeted changes in the microstructure of the superalloy CMSX-4. He loads an alloy sample at 1000 °C for several hundred hours with a stress of up to 250 MPa, which corresponds to a load of about 2.5 tonnes on one square centimetre, until a three-dimensional network of two phases is formed by the coarsening process. In the next step, the matrix phase is extracted from the sample to form a nanoporous membrane, as seen here in the picture of the month.
This membrane is the focus of the DFG project “Targeted design of superalloy membranes and their application processes for the production of colloidal lipid-based drug carrier systems” in which the Institute for Particle Technology and the Institute of Pharmaceutical Technology are involved in addition to the Institute of Materials Science. The aim of the project is to produce nanoporous membranes that can be used as an alternative to the polymer membranes commonly used in pharmacy so far. Up to now, polymer membranes have been used in pharmaceutical nanoemulsification applications. In an emulsification application, a liquid is distributed in fine droplets in a second, immiscible liquid. The membranes are responsible for distribution and droplet size. This process can be used, for example, to bring poorly water-soluble drugs into a form that can be applied.
Advantages of metal membranes
“Metallic membranes are very rare so far and have advantages over polymer membranes,” explains Marius Lück. “Their pore size, for example, is smaller and more uniform. They thus produce a significantly smaller droplet size when liquids flow through them. This means that drugs can be distributed in smaller drops and later be better administered intravenously. In addition, superalloy membranes are more heat-resistant. This allows you to burn them out at high temperatures to clean them. So they can be used much longer.” So-called “fouling”, i.e. the clogging of the membrane pores, prevents the flow and is often the limiting factor in the durability of polymer membranes. This effect does not occur with superalloy membranes because of the cleanability.
In the DFG project, the various possible applications of the membranes are being investigated first. “We are also working on solutions for two more decisive disadvantages of the superalloy membranes. On the one hand, they are comparatively expensive and on the other hand, they are carcinogenic due to their nickel content,” says Lück. There is still a long way to go before nanoporous membranes made of metal can be used in medicine. But the DFG project wants to pave this way with its basic research.