Making aircraft more efficient – with distributed propellers New aircraft configuration being tested in the wind tunnel
Three propellers rotate in front of an aircraft wing in the wind tunnel at Technische Universität Braunschweig. A series of tests at the “Propulsor Test Facility” at Braunschweig’s Research Airport will show how much better several distributed drives are compared to individual propellers.
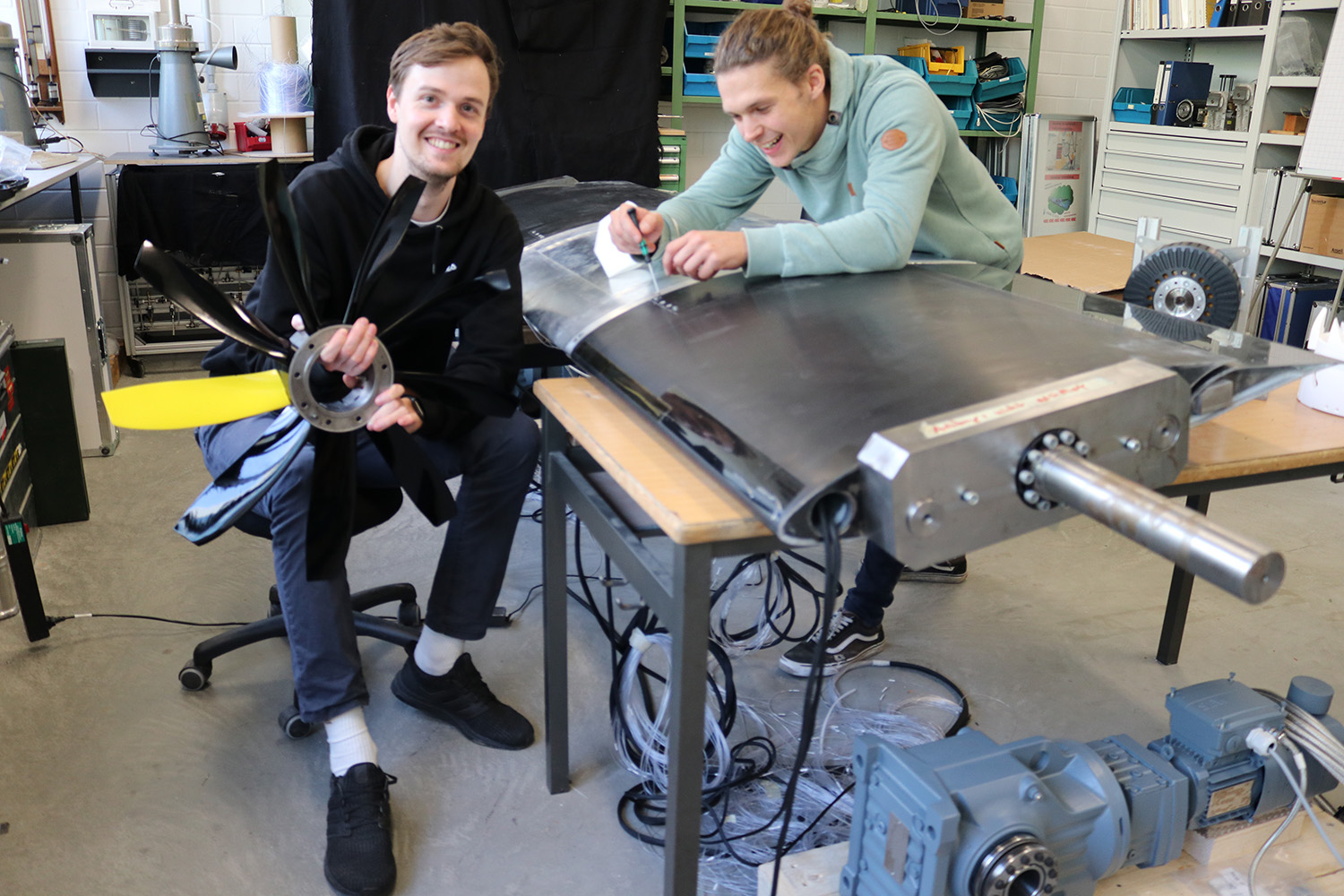
The propeller and wings are currently being prepared for the measurements. Photo credit: Till Lindner/TU Braunschweig
The familiar image of aircraft has hardly changed for decades: the cylindrical fuselage with elongated wings that are swept backwards. Two engines hang under the wing on the left and right. As far as Till Lindner from the Institute for Fluid Mechanics at Braunschweig Airport is concerned, this image could soon change:
“Electric motors are easier to integrate into the aircraft structure than conventional turbines.”
This allows the position of the drives to be much more flexible. One way to take advantage of this flexibility is to position many small propellers in front of the wing.
The propellers accelerate the air and generate the necessary thrust. At the same time, the accelerated air sweeps over the wing wherever a propeller sits in front of the wing. Due to the faster air in the propeller jet, the wing generates more lift than a comparable aircraft with only two propellers would. This is of great benefit to aerodynamicists at TU Brauschweig, because the increased lift means that the wing can be made smaller. A smaller wing causes less drag during cruising and thus leads to lower energy requirements for the aircraft, regardless of whether it is powered by paraffin, battery or fuel cell.
Propeller positions tested in the wind tunnel
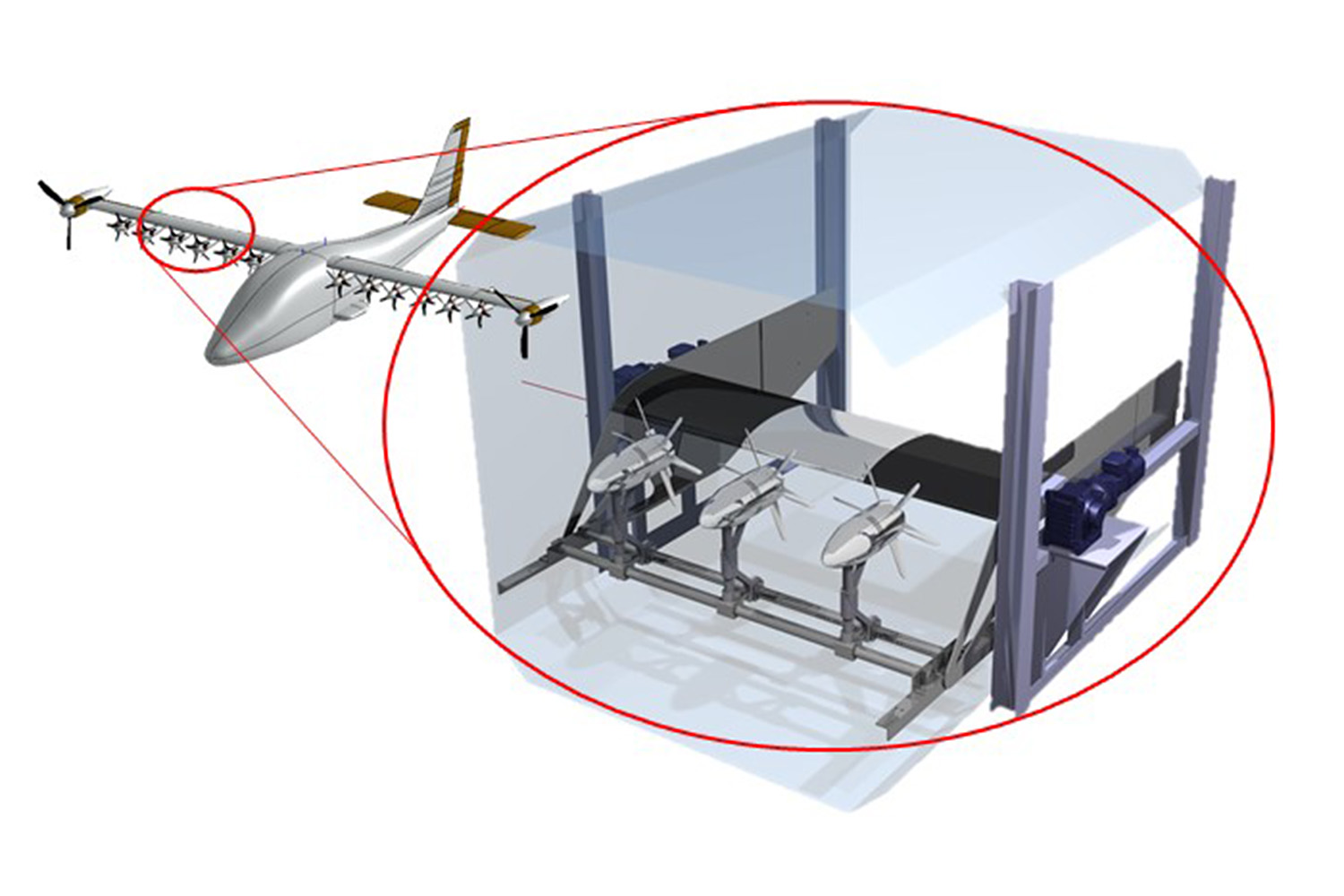
The wind tunnel model is a section of an aircraft with distributed drives. Photo credit: Till Lindner/TU Braunschweig
The flexibility that electric motors bring with them is used to position drives where they are most effective. This is precisely where the experiment by Jonas Oldeweme and Till Lindner comes in: In the wind tunnel experiment, the position of three propellers is varied and thereby lift and drag are measured. If the propellers are positioned unfavourably, nothing remains of the efficiency gain from the distributed drives. During take-off and landing, the optimal propeller position is different than during cruise flight. Where exactly a propeller should be positioned so that the aircraft requires less energy is the question to be answered by the experiment.
The ability to quickly change propeller thrust, position, flap angle and angle of attack is key to an insightful series of measurements. A model has been developed over the last two years precisely for this purpose.
For an aviation of the future powered by sustainable energy sources, such increases in efficiency are necessary through further thought-out aircraft configurations. With its research, TU Braunschweig is helping to ensure that this ambitious goal is met.
Authors: Jonas Oldeweme, Till Lindner