A test bench within a test bench Experimental infrastructure to investigate new rotor concepts, engine intakes and their interaction
The desire for more efficient, low-emission flying calls for engines with a special feature in civil aviation: they have a high bypass ratio and are therefore called UHBR or ultra-high bypass ratio engines. The main thrust of the engine is generated by the bypass flow. In this way, the efficiency of the engine can be increased and the exhaust stream is relieved. By mixing the two flows, the velocity at the exit and thus the noise pollution is reduced. These requirements naturally also have consequences for the design of engines. Following this trend, a new test setup was put into operation at the Institute of Jet Propulsion and Turbomachinery at TU Braunschweig in December 2022.

Jonas Grubert, Patrick Brunow and Prof. Jens Friedrichs (from left to right) in front of the finished construction. Photo credit: Marco Diedrich/TU Braunschweig
To ensure a high bypass flow, the engine nacelles or inlet geometries have an enlarged outer diameter compared to classic jet engines. The reason for this is the first compressor stage, also known as the propulsor or fan stage (here large air masses are sucked in and compressed), which requires a correspondingly large outer diameter with a simultaneously small hub diameter (outer diameter of the drive shaft to which the rotor blades are attached). The resulting increase in drag and weight due to the large nacelle is countered, among other things, by shortening the inlet length and thus directly reducing the distance between the fan and the engine inlet.
The new test bench at the Institute of Jet Propulsion and Turbomachinery serves this development with regard to high bypass ratios and shorter, aerodynamically more aggressive inlet geometries. With the INFRa rig, short for Integrated Nacelle Fan Rig Assembly, the institute’s own side-wind capable wind tunnel was upgraded. The INFRa rig is a model propulsor and comprises the front part of a UHBR engine, i.e. only the fan and the inlet – without combustion chamber, nozzle, primary circuit. Jonas Grubert and Patrick Brunow have thus added a key component to the wind tunnel for research into the thrust-generating propulsor of modern UHBR engines in interaction with current inlet designs.
Under the direction of Professor Jens Friedrichs, complex experiments will be carried out here in the future to investigate the interaction between compressor and air intake and also completely new fan concepts. On the rig side, the entire characteristic map of the compressor can be run by means of a throttle and at the same time an inhomogeneous inflow can be provided by the wind tunnel. The unstable limit ranges of the characteristic map are of great interest, especially from an aeroelastic point of view, as well as for fan design and fan performance. This applies to both the efficiency and the safe operation of this design.
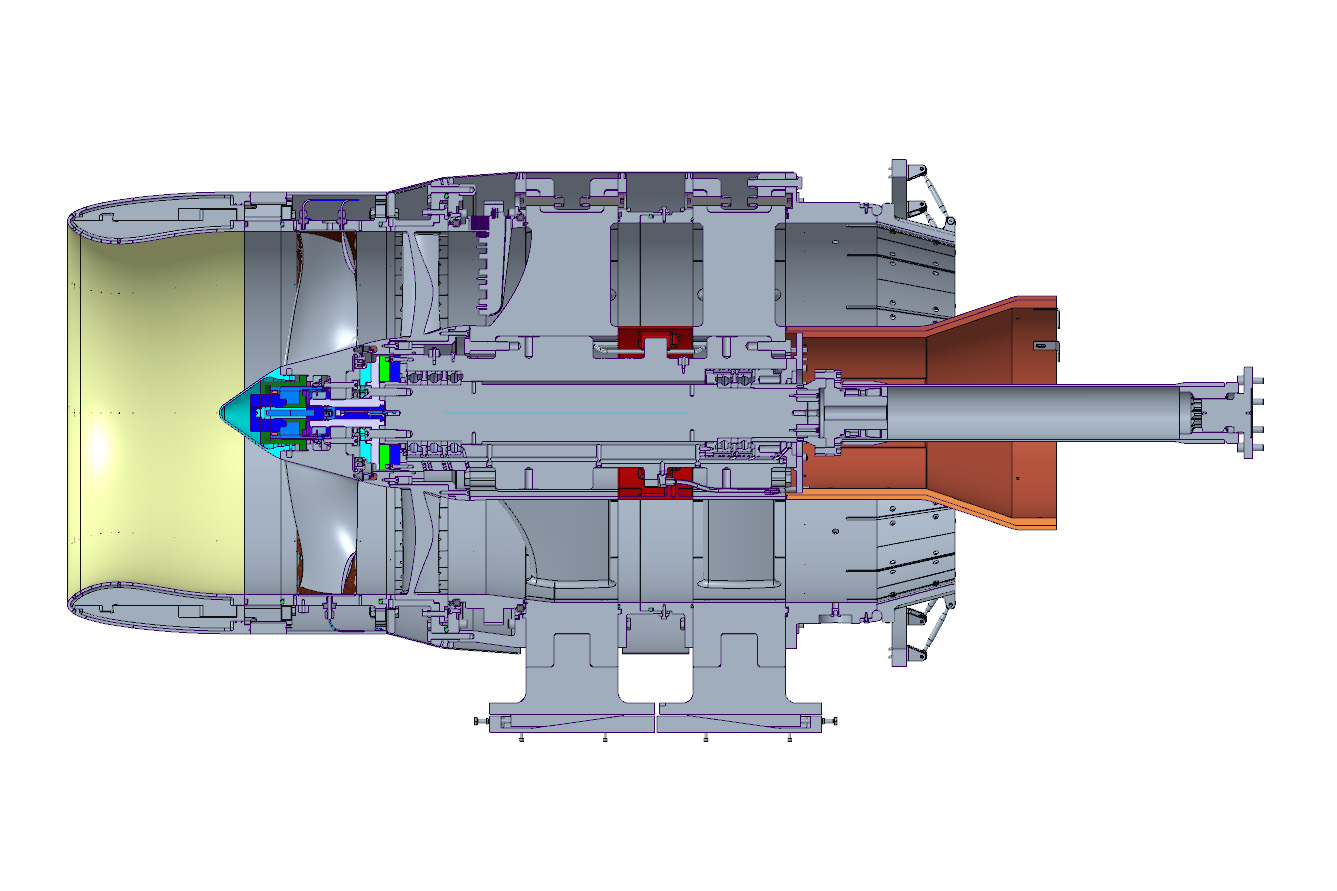
Sectional view of the construction model of the INFRa rig. Photo credit: Patrick Brunow/TU Braunschweig
Model propulsor for experiments
The test specimen (INFRa-Rig) is a joint EU-funded development with DLR and Rolls Royce Germany. With a fan diameter of 650 millimetres, it represents the highly instrumented replica of a modern fan stage on a scale of one to three. The rig replicates the pure secondary flow without the hot circuit of a conventional UHBR engine and is coupled to the drive train of the wind tunnel for operation.
Test specimen with telemetry for the acquisition of rotor measurement data
In addition to conventional stationary and transient pressure measurement technology, especially in the area of the inlet, the test specimen has telemetry to transfer measured values from the rotating to the stationary system. In this case, mainly the data from strain gauges on the blades. They are used to analyse deformations and vibrations during operation. In addition, the movements and gap dimensions of the rotor blades are permanently monitored by means of “blade tip timing” and “blade tip clearance” probes.
Further measurement campaign planned for May 2023
At the moment, the new test bench is still undergoing some modifications so that it can be set up again in the wind tunnel in May 2023 for further measurement campaigns. Then, the design speed of about 8100 rpm will also be approached, which was still undercut by three percent for safety reasons during the initial commissioning. Under full load, the rig delivers mass flows of over 60kg/s with a motor output of 2MW.
Text: Patrick Brunow