A vision for the Ägidienmarkt TU Braunschweig Architecture graduate designs floating venue
What if the Ägidienmarkt in Braunschweig became one again? If the market were once again a place of urban life? That is Janna Vollrath’s vision. In her Master’s thesis, the Architecture graduate from Technische Universität Braunschweig has designed a square that picks up on the history of the area and at the same time points to the future: an event space high above the street, made using new 3D printing techniques.
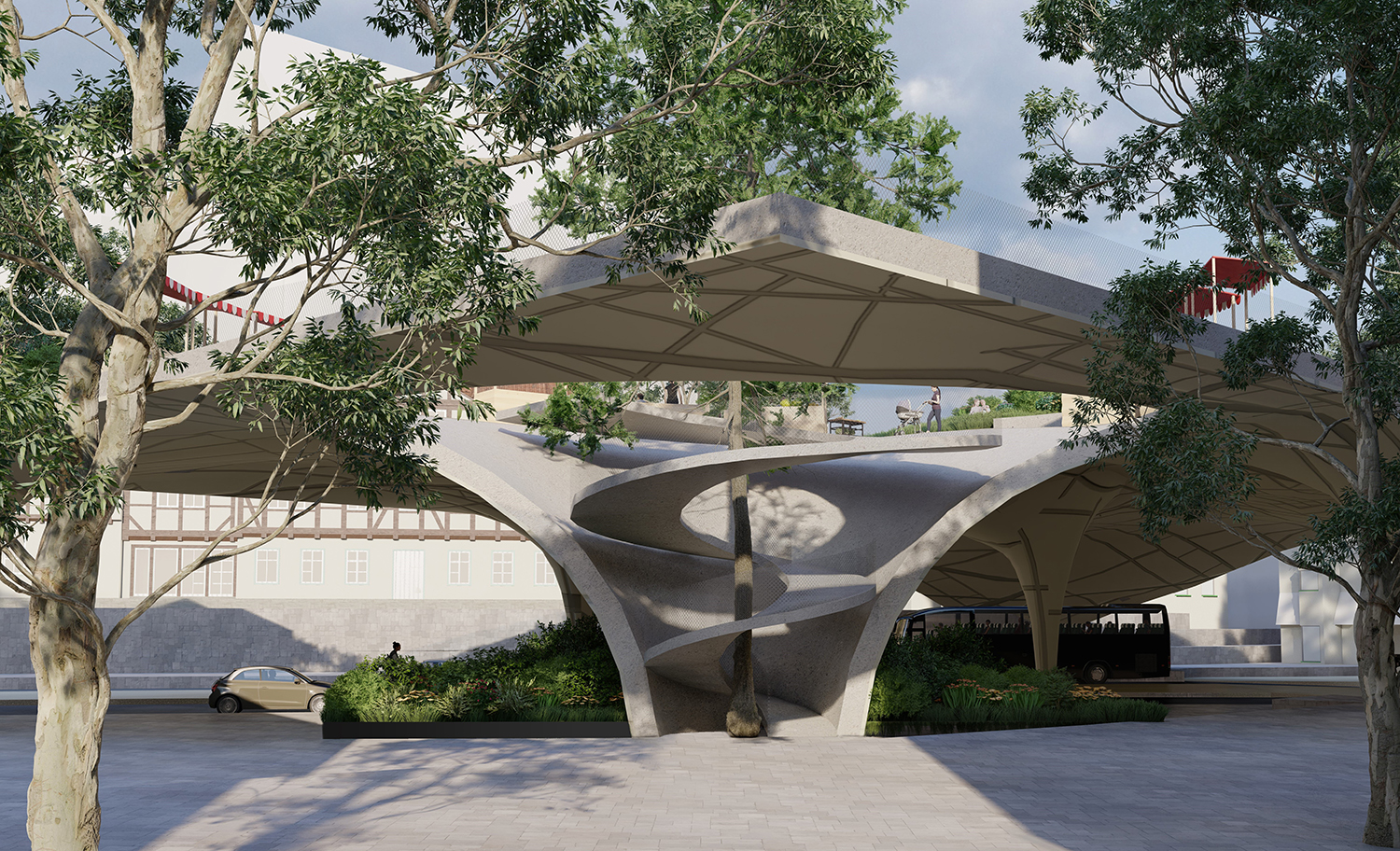
For the Ägidienmarkt, Janna Vollrath has designed an event space that floats above the street. Photo credit: Janna Vollrath/TU Braunschweig
Braunschweig’s Ägidienmarkt was divided into two areas by traffic routing after the Second World War. The historic marketplace situation is no longer recognisable as such, and the connection to the medieval Magniviertel is interrupted. In order to bring the site back together, Janna Vollrath’s design spans the busy Auguststraße with an event area: She has planned a market square with a green area, café and stage. Existing trees are integrated.
The future of building
For this almost floating surface above the street, the budding architect has familiarised herself with the methods of additive manufacturing. She combined three different processes in her work: Automated Shotcrete 3D Printing, Knitcrete and Core Winding. These techniques are being researched at the Institute of Structural Design (ITE) and the Collaborative Research Centre TR277 “Additive Manufacturing in Construction (AMC)” of TU Braunschweig and TU Munich. “Additive manufacturing is part of the future for architecture and construction,” believes Janna Vollrath. The Architecture graduate, who is currently employed at the ITE, sees the possibilities of saving material with concrete and the freedom of form as decisive advantages. This is one of the reasons why she was excited to be able to deal with these topics in her Master’s thesis. She was supervised by Professor Helga Blocksdorf from the Institute of Technology and Design and Professor Norman Hack from ITE.
Knitted truss pattern
Janna Vollrath believes it is very possible that her idea will no longer be a vision in a few years, but could be realised. To achieve the desired shape, she used the still young Knitcrete process by Mariana Popescu, architect and professor at TU Delft, together with Shotcrete 3D printing technology. This involves dividing the shape of the structure into different panels, which are knitted from technical yarns using a CNC knitting machine. “Knitting with the machine allows for a completely individual pattern,” says Janna Vollrath. In this case, she has developed a truss pattern in different colourings of the textile – as a reminder of the half-timbered houses that stood around the Ägidienmarkt, and that were destroyed during the Second World War. In addition, the pattern picks up on the position of the old buildings and thus recalls the former square situation.
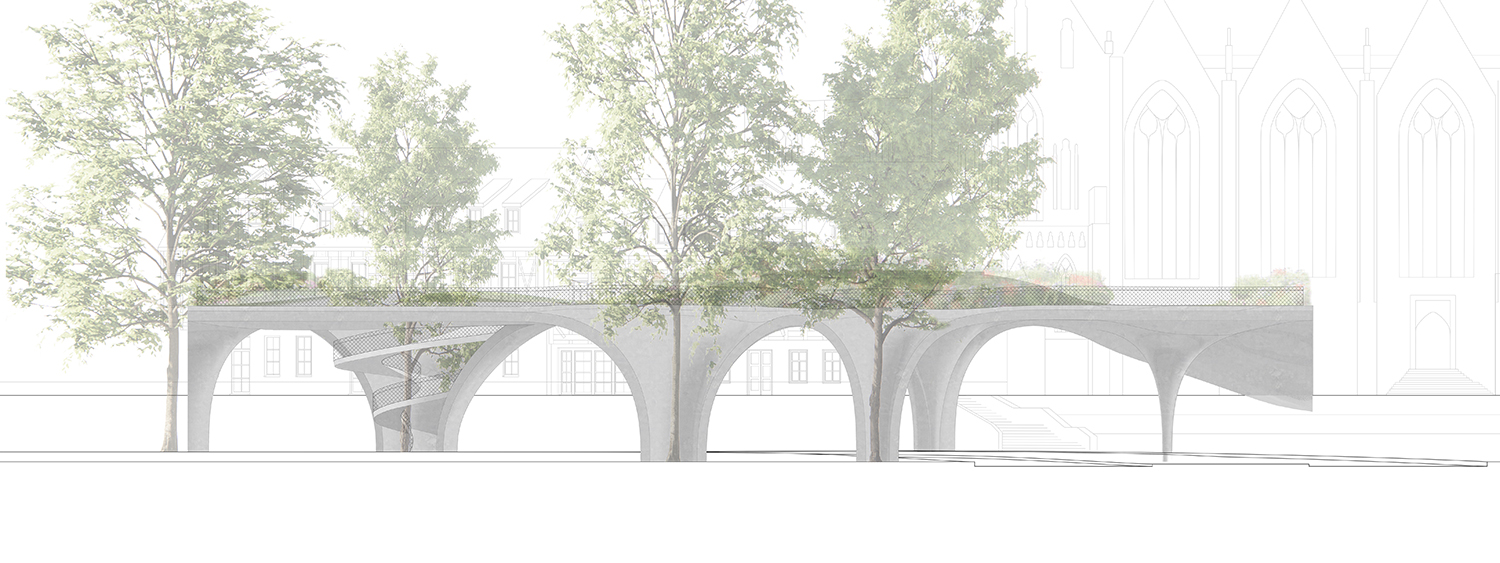
Additive manufacturing methods could be used to create a floating venue at the Ägidienmarkt. Photo credit: Janna Vollrath/TU Braunschweig
The pattern is translated into a code, which the machine then implements. Afterwards, the panels knitted in this way can be packed together and transported to the construction site in a space-saving manner, where everything is joined together and stretched. “This is followed by a first thin and light layer to fix the textile formwork. Various coating materials such as polymers, resins and cement-bound materials can be used for this,” Janna Vollrath explains the rest of the process.
“Structurally, this initially opens up a contradiction, because the truss typologically belongs to the filigree construction with horizontal beam layers as the primary construction, denser transverse layers secondarily and bracing via struts,” explains Professor Helga Blocksdorf. “The exciting research question, which follows directly from this, is therefore to what extent this principle can be transferred to the knitted structure of the shell? Does a heterogeneous construction develop due to the load-optimised reinforcement courses, and if so, what division of tasks between ‘rod’ and ‘panel’ is generated for the purpose of material savings?”
Less material and weight
The next step is also not reminiscent of conventional construction methods. The textile is knitted in such a way that air pockets are formed between the fabric layers in structurally less stressed areas, which are left out during the subsequent concrete pressure. “By optimising the shape and applying the material only where it is structurally needed, we significantly reduce material consumption, weight and thus CO2 emissions,” explains Professor Norman Hack.
After two thin full-surface layers of concrete and a fibre reinforcement optimised according to force progression, all stressing devices can be removed. If everything goes as planned by Janna Vollrath, the final result will be an event area made of a relatively thin layer of concrete with the knitted fabric still visible on the underside. “Such a structure has never been printed before, but I could imagine it working,” says the graduate. On a smaller scale, the Institute of Structural Design has already printed a similar bridge based on a design from the cross-location seminar “Computational Design and Digital Fabrication” of TU Braunschweig, TU Munich and TU Delft. “So it is feasible.”