With bamboo and Lego bridges Vincent Oettel is the new Professor for Solid Construction at the Institute of Building Materials, Solid Construction and Fire Protection
Innovative materials, sustainable construction methods and automated production – civil engineer Vincent Oettel has a clear vision for the future of construction. After his time as a professor in Hannover, he is now returning to Technische Universität Braunschweig to head the Department of Solid Construction at the Institute of Building Materials, Solid Construction and Fire Protection (iBMB). In an interview with Bianca Loschinsky and Heiko Jacobs, he talks about his research on high-performance concrete, the use of bamboo as reinforcement and modular bridge systems reminiscent of Lego.
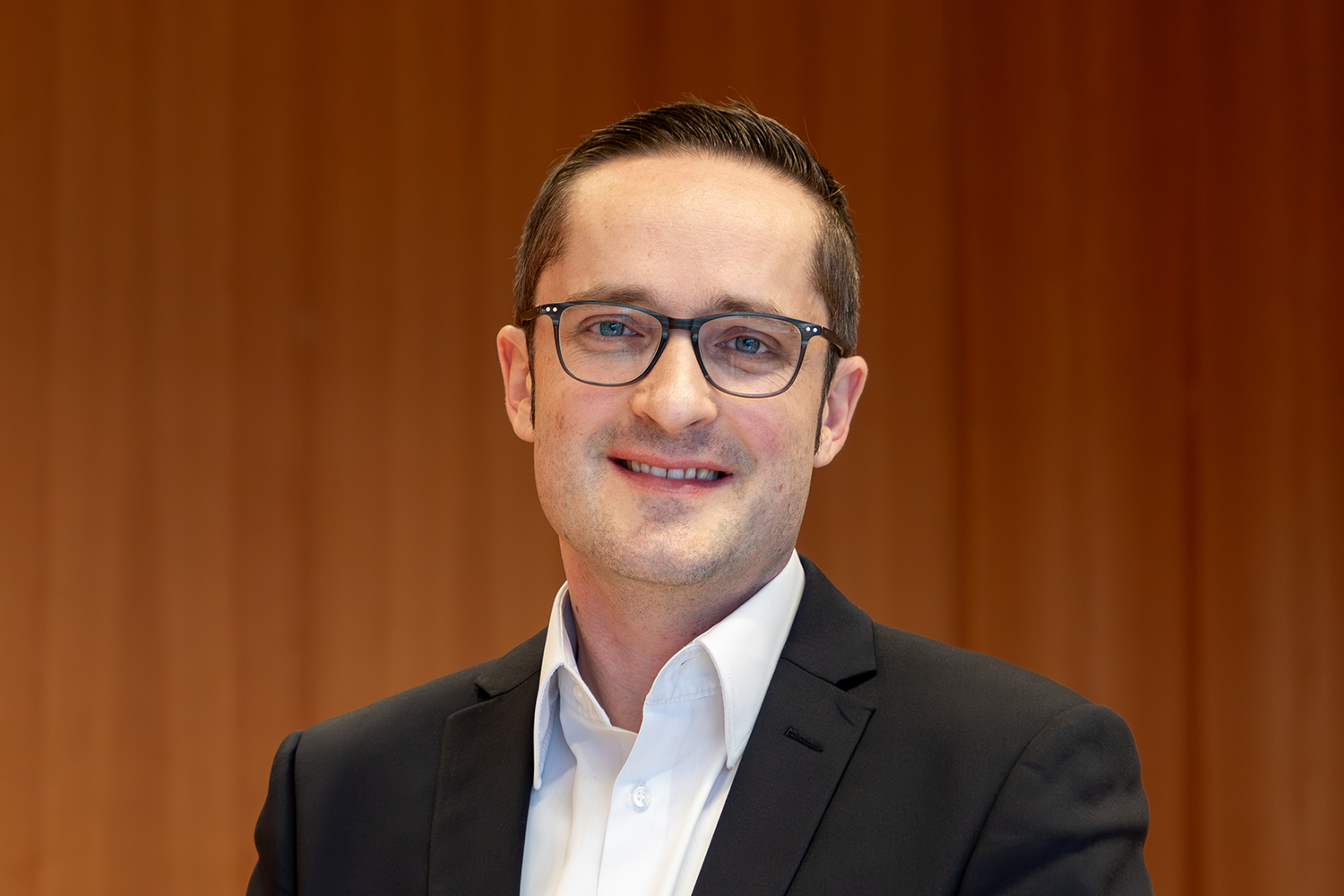
Professor Vincent Oettel heads the Department of Solid Construction at the Institute of Building Materials, Solid Construction and Fire Protection (iBMB). Photo credits: Kristina Rottig/TU Braunschweig
Professor Oettel, you know Braunschweig well: you studied here, submitted your dissertation here and were a senior engineer at the iBMB. After almost four years as a professor in Hannover, you are now returning to the institute as head of the Solid Construction Department. What are you looking forward to here in Braunschweig?
One major point is the Collaborative Research Centre Transregio (TRR) 277 ‘Additive Manufacturing in Construction’ (AMC), in whose application I was already involved. I believe that this is a huge topic: 3D concrete printing and also automated construction. Furthermore, the facilities here are very good, you can do excellent research and I have always felt very comfortable here. By facilities, I mean both the generously sized experimental laboratories of the iBMB and the testing halls of the Materialprüfanstalt (MPA) as well as the opportunities offered by the Collaborative Research Centre TRR 277. TRR 277 is one of the top teams worldwide in the field of 3D printing in construction. It has already made big waves.
If we go back even further, you initially worked as a journeyman carpenter for two years. How did you come to favour reinforced concrete over wood?
Originally, I started out in timber construction, then moved on to steel construction and only later to solid construction. I have always found it very interesting to use the building material where it can be best utilised according to its potential. Ultimately, it was always a challenge to push the material even further.
What motivated you to conduct research in this area?
It’s not just my daughters who ask me: What are we doing for the future, for the preservation of the planet? The aspect of sustainability is important to me, as is the fight against the housing shortage. Fast construction reduces costs and compensates for the shortage of skilled workers. So at some point we have to automate and, above all, do so sustainably.
I also find it inspiring to talk to other disciplines, for example mechanical engineering. You first have to learn the technical vocabulary, but then it becomes very exciting. And I believe that a great deal can be achieved by combining mechanical and civil engineering.
What are the main research areas and projects you will be working on at TU Braunschweig?
In addition to automated construction, we are investigating new possibilities for bridge renovation in the field of sustainable construction, for example, which have already been tested in our neighbouring countries but have not yet been investigated in Germany. We have many dilapidated bridges, but we cannot rebuild them all for reasons of cost and time. In addition, the preservation of existing structures almost always represents the most sustainable solution. That’s why we want to mill off the asphalt and apply a high-performance concrete that is the same height as the asphalt was before. So I’m not adding any dead weight of my own, but the high-performance concrete serves as a road surface and cross-section supplement that strengthens the bridge. This can be done in a very short construction time, which offers economic and ecological advantages.
When it comes to concrete printing, it is not always possible or economical to bring the machines to the construction site. You therefore talk about ‘Lego bridges’ when it comes to modular construction: what should we understand by that? Is there also a playful element involved?
We produce modules, ‘Lego bricks’ if you like, in a factory and deliver them to the construction site. Thanks to factory production, we can manufacture the modules automatically, protected from the weather and to a very high quality. If we manufacture them on site, we need a lot of additional safety measures and therefore more material due to the higher inaccuracies, which we do not need if we manufacture them in a factory.
On the construction site, we can then assemble the modules like Lego bricks or thread them like a string of pearls onto tendons and brace them, thus very quickly erecting a lift shaft, a wind turbine tower or a bridge girder. This way, we can, for example, demolish a dilapidated bridge that we can no longer reinforce and replace it very quickly. This way, we can shorten traffic detours and congestion times and save enormous amounts of CO₂ emissions. The difficulty lies in connecting these parts in a force-locked manner and designing the joints accordingly. Here, we are primarily concerned with the automated milling of profiled joints and various joining techniques for dry joints. Compared to glued or mortared joints, dry joints have the advantage that defective modules can be replaced and dismantling is much easier.
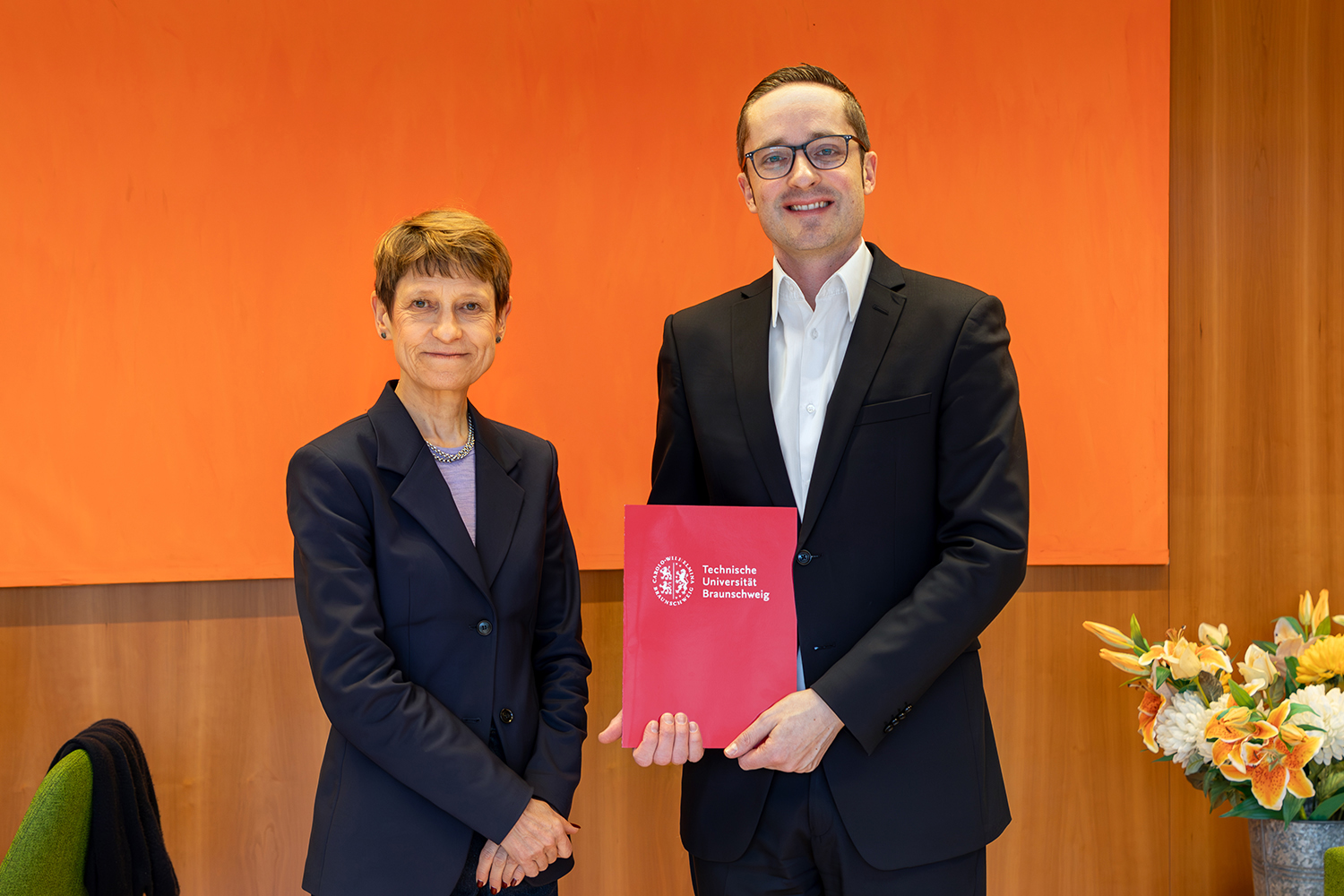
TU President Angela Ittel and Professor Vincent Oettel. Photo credits: Kristina Rottig/TU Braunschweig
What can the area of solid construction contribute to a climate-neutral construction industry? Where are the limits of your field?
When we manufacture something, we consume resources and produce emissions. So there are limits, but we have to keep pushing them back to be as sustainable as possible. And to do that, we adapt the material, the design and the construction method.
This is how we develop resource-optimised load-bearing structures, for example thin-walled concrete structures with ribs that are more reminiscent of steel construction. We save as much material as possible through targeted topology optimisation. As an alternative to steel reinforcement, we are trying to incorporate bamboo rods into concrete. This would also help in emerging markets where steel is usually not produced locally but has to be purchased on the world market. Bamboo is a plant that grows in many parts of the world and, depending on the variety, can grow by an average of 20 to 30 centimetres per day. We still have to solve problems, such as the swelling of the dried material when it is embedded in the concrete.
What can our students expect in your teaching? How do you balance traditional topics in solid construction with the future-oriented topics of digital, robotic construction in your teaching?
First of all, the traditional topics: our students should understand the basics. How does reinforced concrete work, how is a design carried out, how do I have to construct that – these are the basics. In the master’s programme, we then move on to computer-based design, for example in bridge construction. There are traditional lectures, but also exercises in which students model and design a bridge using software. In the subsequent exercise, we use plausibility checks and estimates to determine whether the computer results are correct. We don’t want our students to rely too heavily on the software. It always produces a result, but that depends very much on the modelling and doesn’t have to correspond to reality, and that’s where we have to sensitise them and also prepare them.
We familiarise students with innovative building materials such as high-performance concrete and non-metallic reinforcement, and also teach how to manufacture, dimension and construct. How can I build in a way that optimises materials and resources, and what are the consequences of all this? How do you actually do a life cycle assessment and how do we make it ecologically justifiable? Our students are the people who will later take the innovations into the offices and companies. After all, we can’t go on as we have done in the past.
How would you describe your typical working day in three words?
Interesting. Challenging. Diverse.