Picture of the month: Shape memory plastic from a 4D printer Institute for Mechanics and Adaptronics investigates printed shape memory structures made from thermoplastic polymers
The image shows a strand being deposited during 4D printing. 4D printing? The term refers to the additive manufacturing of active structures, in this case a shape memory structure. This is achieved by process parameters that cause the material – in this case a thermoplastic polymer, i.e. plastic – to stretch and then freeze as it cools. Subsequent activation by heating the structure releases the strain and the structure changes shape. The detailed image shows what happens to the polymer melt during printing.
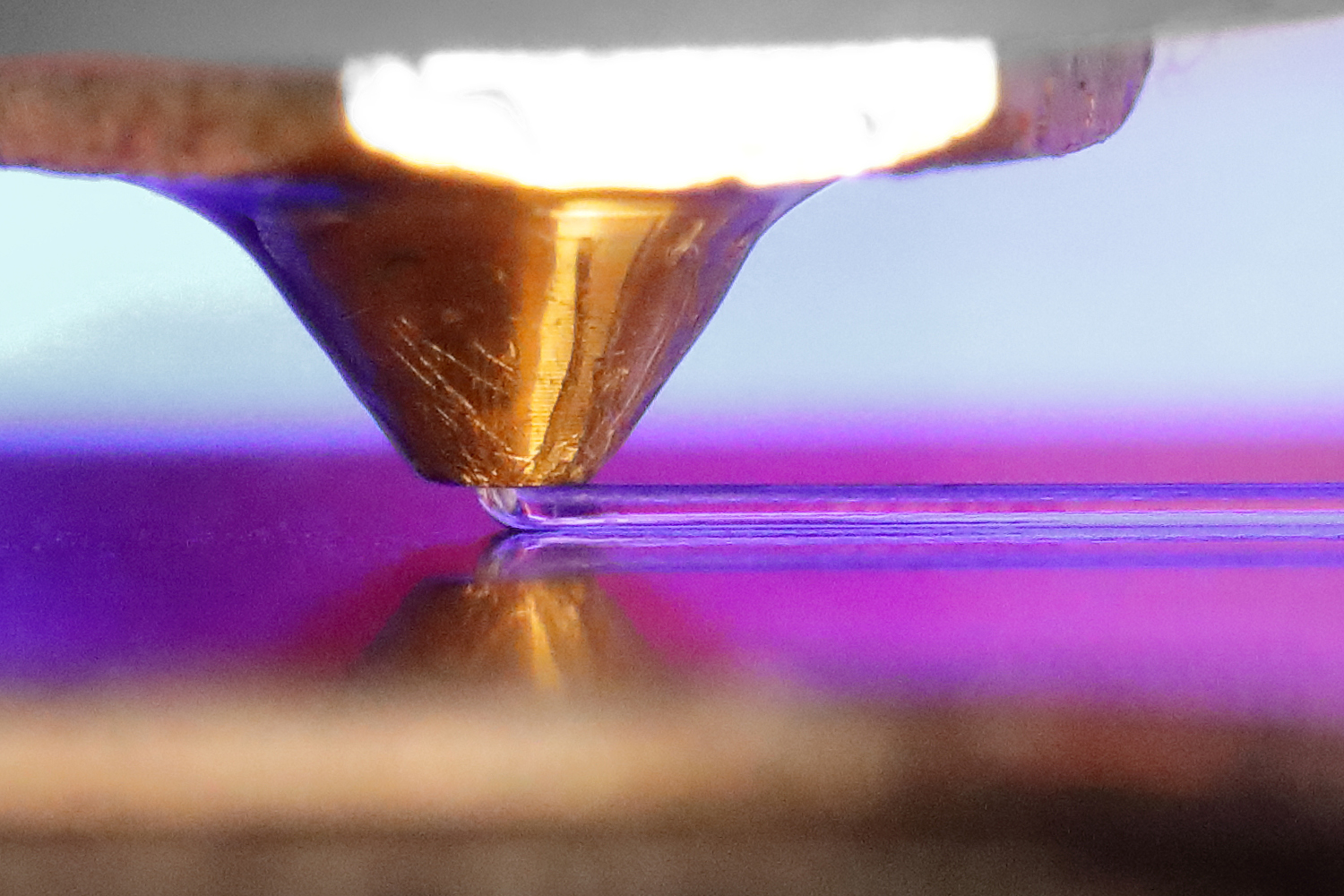
Depositing a strand during 4D printing. Image: Ferdinand Linus Maria Cerbe/TU Braunschweig
Shape memory allows a shape to change in response to external stimuli. These stimuli can be temperature, electric or magnetic fields, radiation or light. In the DFG-funded research project ‘Printed Polymer Shape Memory Structures’, the Institute of Mechanics and Adaptronics is specifically investigating the influence of various parameters on the shape change of thermoplastic polymers. Thermoplastics are plastics that become soft and malleable when heated and harden again when cooled, without changing their chemical structure. This property makes them repeatedly deformable.
To ensure reliable shape memory, the material is characterised using thermo-mechanical tests. During the 4D printing process, the polymer is melted, pre-stressed and cooled. This requires knowledge of the deformation and flow behaviour, i.e. the rheology of the material.
The aim of the TU scientists is to be able to simulate shape memory behaviour and to enable the constructive design and identification of process parameters for 4D-printed shape memory structures. To this end, the process chain from material selection, design, printing process parameters and stimulus activation parameters will be investigated. This should bring 4D printing one step closer to the industrial process chain.
The technology is still in its infancy, but there are already theoretical applications at various scales. In medical technology, patient-specific stents (blood vessel support implants) made of polymers in the millimetre to centimetre range offer advantages in terms of compatibility and adaptability. In the aerospace industry, the effect could be used to unfold large structures measuring several metres, such as solar sails or satellites. Such folding mechanisms can also be extended to textile technology, for example for tents. In the Earth’s gravitational field, however, the small forces with which shape memory polymers deform pose a major challenge. The potential applications for printed polymer shape-memory structures are therefore many and varied, but still raise exciting scientific questions.