Picture of the month: “Press it!” 3D printing steel for the buildings of the future
In order to complement traditional steel construction with complex geometries, individual components are being produced using the Wire Arc Additive Manufacturing (WAAM) 3D printing process. To ensure the safe use of these components in buildings, it is necessary to understand their behaviour under tensile and compressive stress. Marc Müggenburg, Dr. Julian Unglaub and Professor Klaus Thiele from the Institute of Steel Construction at TU Braunschweig are therefore investigating the use of 3D printing of steel in the construction industry and its component behaviour. The picture of the month shows a special steel pipe printed using the WAAM process in a load test.
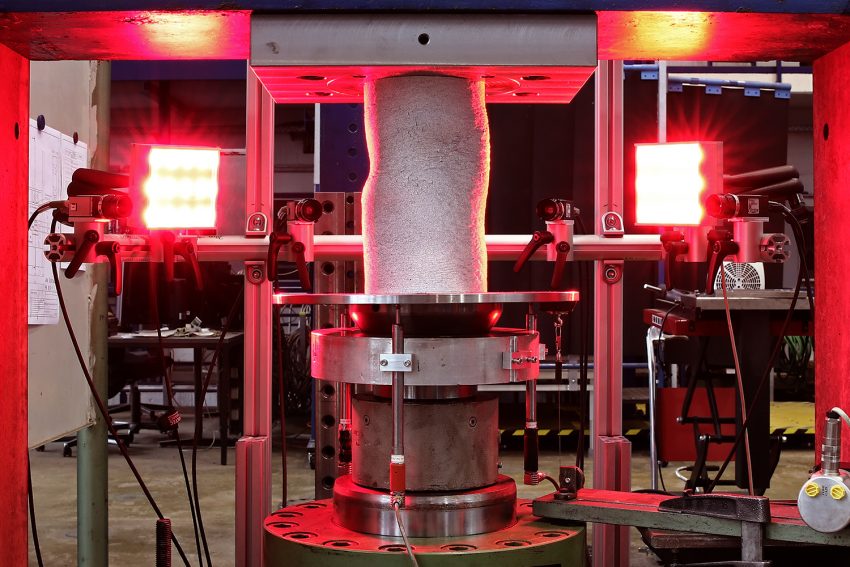
At the Institute of Steel Construction, pressure tests are carried out on additively manufactured pipes. Photo credit: Institute of steel construction/TU Braunschweig
Additive manufacturing, also known as 3D printing, allows the use of a wide range of materials. In the construction industry, steel is mainly printed using Wire Arc Additive Manufacturing (WAAM). This process combines a welding machine with a robotic arm. The wire-shaped feedstock is melted by an arc and deposited in layers. The WAAM process makes it possible to produce individual components with complex geometries that can be more than a metre long in any direction. These components can be used to complement traditional steel structures, for example with innovative facade nodes, tree-shaped support structures or to reinforce existing structures.
Additively manufactured steel pipes in a pressure test
Before these components can be used safely in buildings, their behaviour under tensile and compressive stress needs to be understood. For this reason, the scientists printed special steel tubes using the WAAM process and then subjected them to load tests at the Institute of Steel Construction. In the tests, the tubes were vertically compressed in a controlled manner using a high force. The researchers recorded the deformation of the tubes using four high-resolution cameras. To highlight the contrasts on the undulating surface of the component during the compression tests, the tubes were illuminated with two intense red lights.
Component behaviour under pressure
The pressure tests on the additively manufactured pipes have shown that the steel used is suitable for use in the construction industry, as the components exhibit high strength and large deformation before failure. The extent to which the findings from the printed pipes can be applied to larger steel components is currently being investigated. In addition, the aim is to create a ‘digital twin’ of the steel components during 3D printing in the future. This ‘digital twin’ will make it possible to predict component behaviour without the need for destructive testing.
The background
The research work of the Institute of Steel Construction presented in this article is part of the project ‘Wire Arc Additive Manufacturing (WAAM) of High Strength and Individualised Steel Components (A07)’. The project is part of the Collaborative Research Centre Transregio 277 ‘Additive Manufacturing in Construction’ (AMC) – project number 414265976.