Picture of the month: 3D printing in space Institute of Space Systems investigates printing strategies using satellites
This is a macro image of a strand of printed plastic reinforced with continuous carbon fibres. It was produced using a 3D printer that allows the mixing and production of thermoplastic material with continuous carbon fibres. The purpose of the sample was to get an idea of the impregnation of the fibres, i.e. how well the polymer, which is liquefied during the printing process, was able to penetrate the fibres. The sample is then bent to assess the mixing of the materials and thus the stability.
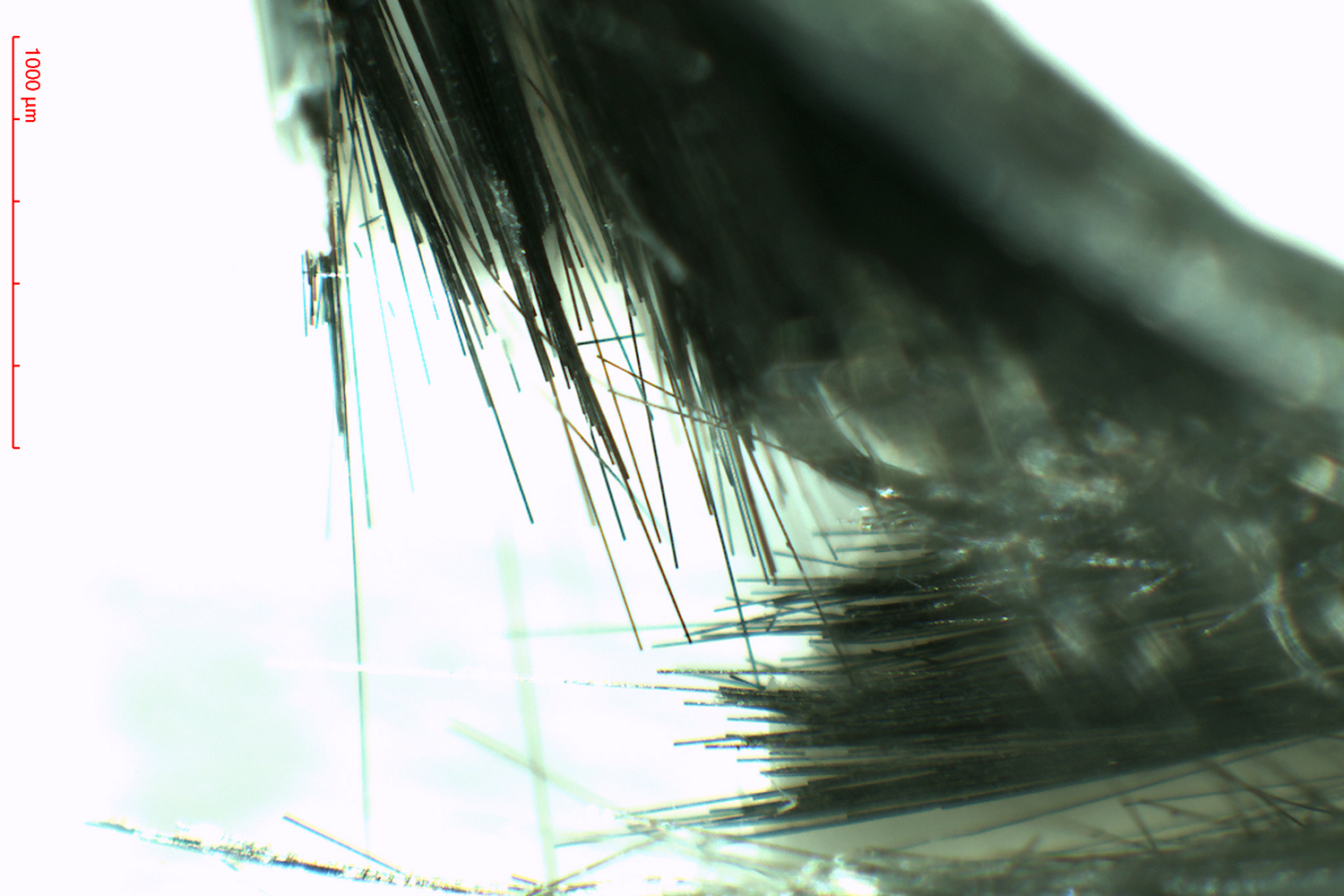
Macro image of a strand of printed plastic reinforced with endless carbon fibres. Picture credits: Niklas Kyriazis/IRAS
The image was taken as part of the work of the Junior Research Group ‘In-Space Manufacturing’. The group is investigating manufacturing technologies for use in space. The aim is to produce structures or even entire spacecraft and stations in space in order to avoid the mass and size restrictions of launch vehicles and to save mass by eliminating high launch loads.
Additive manufacturing processes – such as classic, widely used 3D printing with thermoplastics – are the main production methods under consideration. This technology needs to be adapted to space conditions. The group is investigating two aspects: printing with high-temperature thermoplastics in a vacuum, and printing strategies on free-floating satellites as a carrier for the printer.
For the latter, the filament polylactic acid (PLA) is used as the printing material, since the aim is not to investigate the material properties but rather to validate the printing process, and PLA is much cheaper than the high-temperature thermoplastics. As the aim is to produce load-bearing structures for use in space, it is important that these have sufficient strength. A project has therefore been set up to investigate the introduction of carbon fibres into the process. There are several ways in which carbon fibres can be used in a 3D printing process. As chopped short fibres added to the thermoplastic filament and as continuous long fibres. Both are typically used as pre-mixed filaments. The continuous filaments are generally more stable than the short filaments, but also more difficult to process. Both types of filament have the disadvantage that they have to be purchased pre-mixed with thermoplastic material, and the material combinations available on the market are extremely limited.
The classic 3D printing process has therefore been modified so that the carbon fibre is drawn endlessly into the print head’s heating block during printing, where it mixes with the thermoplastic material and is coextruded.
The better the carbon fibres mix with the PLA, the stronger the extruded strand. The image shows a large number of ‘dry’ fibres after the printed strand has broken, indicating that the mixing was not optimal for this sample.