Cool and clever Spin-off from TU Braunschweig enables energy and CO2 savings in cold rooms
Thick layers of ice in the freezer are an annoyance that most people know. But it is not only there that they take up space, cost energy and emit additional CO2—icing also causes problems in cold rooms, on aircraft, drones, wind turbines and in many other areas. Stephan Bansmer, Juan Velandia and David Burzynski have taken on this challenge as employees at the Institute of Fluid Mechanics at TU Braunschweig. Now they are setting up their own business with their idea and developing intelligent system solutions that prevent ice formation and control defrosting automatically. In the interview, they tell us more about their project and their spin-off from the university.
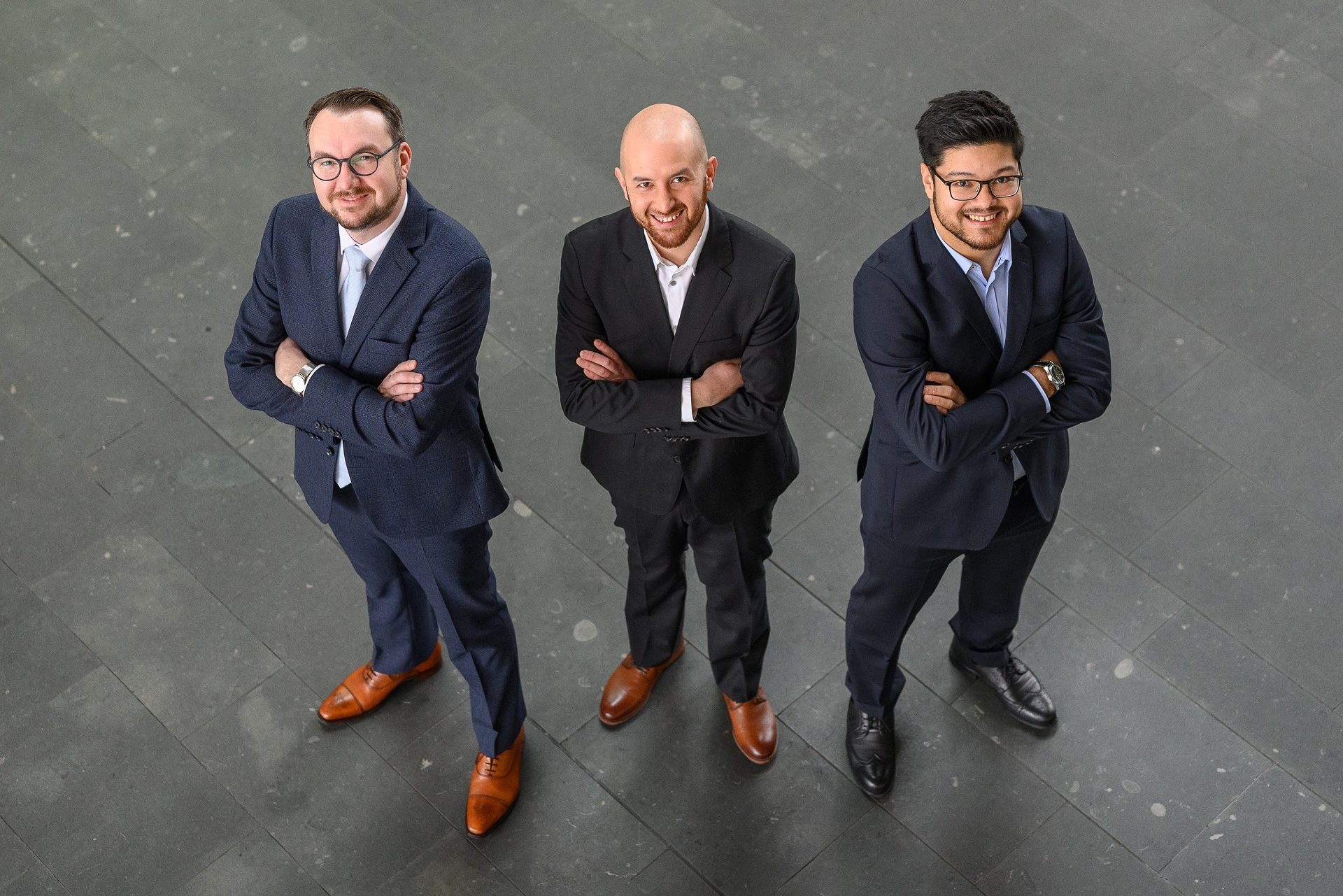
The founding team of Coldsense Technologies (from left to right): Stephan Bansmer, Juan Velandia and David Burzynski. Photo credit: Roman Brodel/Photostudio Roman Brodel
How did the idea for your project come about?
David Burzynski: The first idea came to us during lunch, because we had a constant icing problem at a deep-freezing facility at the TU. After numerous discussions with experts from the field of refrigeration technology about the current state of the art, we designed various system solutions to make the system safer and more efficient. Relatively quickly we realised that there was great potential behind it!
What is the exact benefit of your technology?
Stephan Bansmer: Cold rooms, refrigerators and freezer compartments have heat exchangers that tend to build up ice because they operate below the freezing point. This ice build-up reduces the cooling capacity, which in turn increases electricity consumption. It is therefore important to defrost heat exchangers regularly. The start and length of such defrost cycles in conventional systems are time-controlled and do not adapt to the demanding logistical processes of industry. This makes these systems inefficient. In contrast, we develop customised and intelligent system solutions that prevent ice formation and control defrosting automatically and as needed. This keeps the food cold chain intact. The energy and CO2 savings potential is great.
In which areas could your technology be used?
Stephan Bansmer: Our technology can be used in many areas, such as in the treatment of technical gases, in aircraft, drones, wind turbines or rail vehicles. In principle, wherever icing is an issue. At the moment, we are mainly focusing on optimising cooling systems, for example in the food, pharmaceutical and chemical industries as well as in airport logistics. In other words, where products have to be cooled.
How long have you been working on the project and what is the next step?
David Burzynski: We have actually been working on our startup since the beginning of 2019. Juan Velandia and I came up with the first business ideas after discussions about our and current research results. In parallel, Stephan Bansmer wanted to become more active in the start-up scene after a research stay in Cambridge, UK. Finally, we decided together to launch Coldsense. Since 1 January 2021, the EXIST start-up grant has been running, where we are financially supported by the Federal Ministry for Economic Affairs and Energy and the EU.
Juan Velandia: Next, we will offer our system solutions in many different applications in the food industry and develop new technologies with the data obtained. Next year, we will also work together with the Institute of Fluid Mechanics at TU Braunschweig and the professorship for laser-based methods of large-area surface structuring at TU Dresden as well as the Landwind Group in the research project ‘MicroIce’ on the development of non-stick coatings. Similar to an egg on a Teflon pan, this should reduce the amount of ice that sticks to wind turbine rotor blades. We also want to integrate this technology and other innovations from cutting-edge research in other sectors in order to increase the service life of the facilities.
Who accompanied you on the TU side?
Juan Velandia: On the TU side, our mentor Prof. Dr.-Ing. Rolf Radespiel from the Institute of Fluid Mechanics accompanies us on the technical and interdisciplinary issues. In addition, we have received continuous and very competent support from Dr. Manuela-Christina Hahn from the Technology Transfer Office since the application was submitted. We are very grateful to both of them.